Topography of friction surface: the measurements of surface roughness, arithmetic average roughness(Ra), of a friction surface after
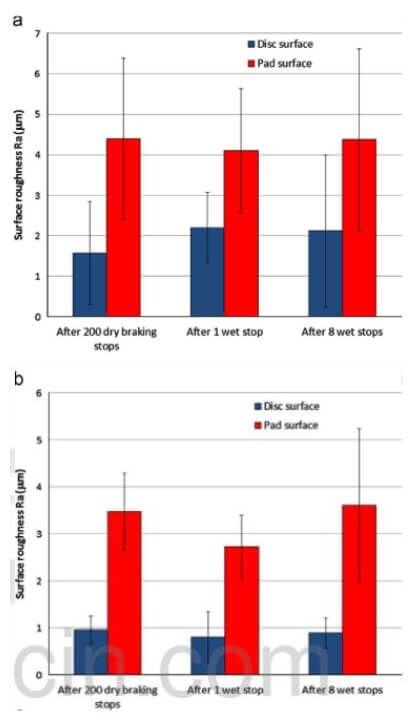
fig.11-roughness of Ra measured on the disc and pad fraction surfaces of Brake-H and Brake-L
testing in wet environment are presented in Fig.11 for both disc and pad of a brake. For Brake-H, the Ra of the disc friction surface increased from 1.8 to 2.1 μm when the test in wet was started. As the test proceeded, there was little change, whilst the standard deviation increased from the first to the last braking stop. The Ra for the pad had virtually no change, maintaining a level of 4.1-4.3 μm. For Brake-L, it seems the Ra of the brake disc had a little reduction from 1.0 μm to a level between 0.8 μm and 0.9 μm after wet tests. The Ra of the friction surface of pad reduced from 3.5 to 2.8 μm when the water spray was applied, but increased to 3.5 μm at the end of wet test.
It is noted that the measurements of Ra had a large variation, accompanied by a large standard deviation. This might be due to a fact that the carbon composites for both brake disc and pad are highly heterogeneous at a macro-scale level, which is comparable to the sampled range by the stylus. It is therefore highly likely that one measurement was heavily weighted by one particular feature on the surface. For instance, the voids and friction plateaus can contribute differently from one measurement to another. Having this accounted, and based on the measurement of the Ra, we do not believe that water spray had any radical change of the surface tomography in such large scale, i.e. the friction plateaus developed through bedding in ambient air were approximately maintained in the same format. The only exception is that the Ra for composite H had small increase after the wet tests probably due to the removal of transfer materials, particularly these deposited in C/C regions, If the hydrodynamic lubrication had associated with roughness of friction surface at such a scale, the variation of friction coefficient with the sliding speed would not have varied, or even showed an increasing trend, from one braking stop to another one. Assume each braking cycle removes a certain amount of friction transfer layer off from the friction surface, and the consequence of this cyclical dynamic braking process would make the friction surface rougher, leading to more boundary friction and therefore increased friction coefficient.
Under such circumstance, the fall of friction coefficient with braking stop in water spray must be associated to the change of friction contact regions, rather than the macro-scale topographic structure of friction surface. For the composite disc, these plateaus were identified in Section 3.2, and are examined further after braking in water spray environment.
related news /articles:
Friction performance of C/SiC brakes in different environment (8)
Friction performance of C/SiC brakes in different environment (7)
Friction performance of C/SiC brakes in different environment (5)
Friction performance of C/SiC brakes in different environment (3)