Impact of sliding speed on friction performance in water spray environment: If water spray during braking brings the non-boundary friction, i.e. hydrostatic friction, into the process, i.e. water acts as a lubricant between contact surfaces of a brake, sliding speed of the friction pair should have a significant impact on the coefficient of friction against the velocity (v), or a parameter including velocity, viscosity of lubricant (η), and contact pressure (p). This type of plot is widely called Stribeck plot.
For each braking stop, the sliding speed started from the highest and ended at the lowest. Having η=8.9*10-4 Pas for water and p as the nominal pressure of braking, we can plot the instantly logged friction coefficient inside a braking stop against log (Vη/p). Representative plots are shown in Fig.10 (a) and (b) for Brake-H and Brake-L, respectively.
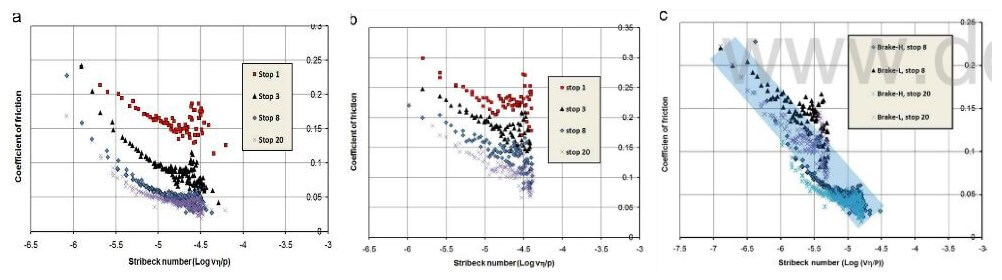
fig.10-representative plots of fricton coefficient versus stribeck number log
From the shape of the curves, the following points can be drawn:
- Around the low sliding speed end with smaller values of log (Vη/p), which was near the end of each braking stop, there was no plateau showing that friction coefficient was insensitive to sliding speed. This fact implies that there was no full boundary friction (also called boundary lubrication), during braking for all braking stops of both brakes.
carbon ceramic composite (C-SiC) brakes for racing car-3
- Around the higher sliding speed end with larger values of log (Vη/p), which was around the start of each braking stop, most curves had not reached a flattened stage, apart from a large fluctuation among the data, which is deemed due to vibration of testing rig at high rotation speed. However, as the braking number increased to 20, there was a tendency to become flattened, and this tendency became more obvious for Brake-H. Such flattening, or even slightly ascending trend, implies that hydrodynamic friction tended to become in dominant at the initial stage of braking when enough braking stops were applied in water spray environment.
- In between the low and high speed regime, all braking stops showed a continuous fall of friction coefficient as the sliding speed, or log (Vη/p), increased. Such trend indicates without ambiguity that the friction in this region was governed by a mixed mechanism of boundary and hydrodynamic friction, and the friction surfaces had a partial contact only. As the braking proceeded, contribution by hydrodynamic friction reduced continuously, and boundary friction increased at the same time, owing to the reduction of sliding speed.
Based on the above analysis, it is apparent that water spray immediately changes full boundary friction operated in ambient air into partial boundary one, and the appearance of hydrodynamic friction brings the friction coefficient down significantly. To understand the variation of averaged friction coefficient with the number of braking stop and the difference between Brake-H and Brake-L, we need to examine the friction surface further.
related news /articles:
Friction performance of C/SiC brakes in different environment (7)
Friction performance of C/SiC brakes in different environment (5)
Friction performance of C/SiC brakes in different environment (3)
Applications of carbon fiber reinforced composite (3)-airplane brake discs