Two types of liquid impregnants are used to density CC composite preforms. The first includes pitch, which may be coal tar or petroleum
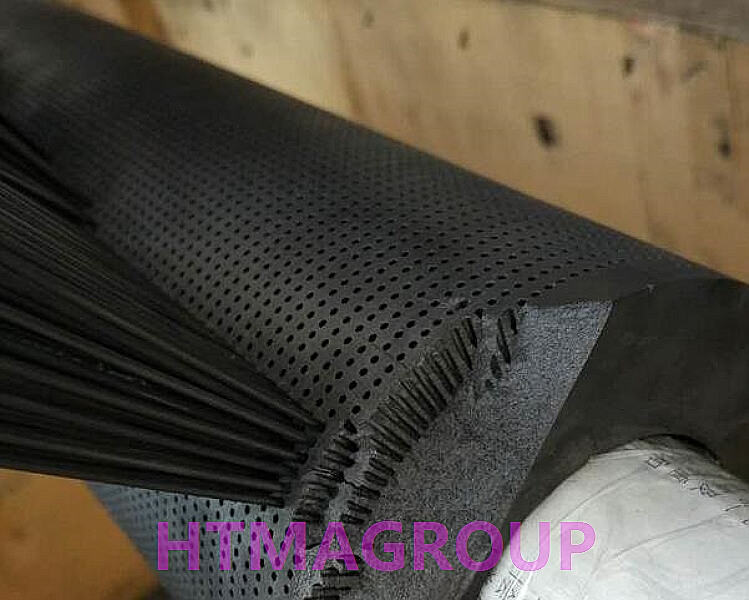
pitch coke carbon composite
based, and the other is derived from resins or polymers. Both are used because they have suitable viscosities and the carbon yields are high enough to provide high-density CC composites up to 1.9g/cm3.
Pitch matrices
The basic fabrication method for producing pitch matrix CC composites is to use pressure to force pitch into an evacuated cavity that contains the dry fiber preform. The chemical composition of the pitch is believed to control the microstructure and reactivity of the resulting CC solid. It is known, for example, the while most pitches produce graphitic matrices, other pitches cannot be graphitized because some of the molecules are not capable of forming a hexagonal-type 3D graphitic network. In other pitches, side chains exist, for example, alkyl side chains, which distort the crystal structure and render the resulting carbonized material somewhat reactive. Conversely, many pitches contain trace metal impurities that catalyze graphitization locally, while others are known to catalyze high-temperature oxidation reactions.
The infiltration-carbonization cycle can be performed at atmospheric pressure or at pressures up to 3000 pounds
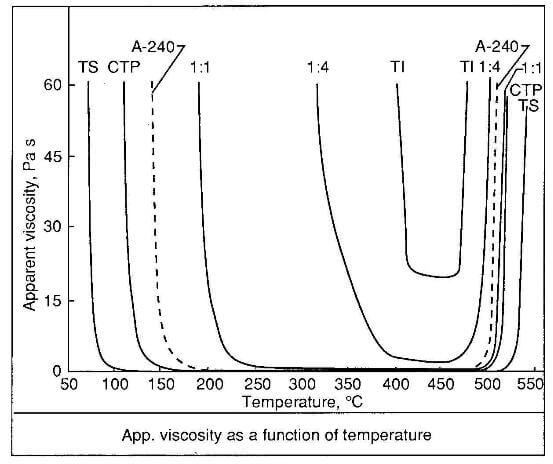
viscosity as a function of temperature
per inch. At atmospheric pressure, the carbonization of the pitch matrix is carried out by heating to 1000C under a very slight partial pressure of nitrogen. This carbonization process can be characterized by the viscosity changes experienced by the pitch. Depending upon the elemental composition and the thermal history, the matrix softens until oxygenated functional groups and their sulfur and nitrogen equivalents are released, subsequently resulting in minimum viscosity. Typical viscosity temperature relationships for pitches are shown in figure 1. cfccarbon.com. Essentially, heating isotropic pitch from room temperature results in the melting of solid pitch and in low viscosity. Continued increase of temperature causes relatively insignificant changes in viscosity although devolatilization of the pitch continues until, at a critical temperature, the viscosity of the pitch increased reapidly.
The kinetics of mesophase formation depend on the composition, reaction temperature, degree of agitation, and the removal rate of the lower molecular weight fractions. In general, however, as the temperature of the pitch is increased, the rate of mesophase formation and viscosity increase. Mesophase spheres similar to those shown in figure 3 begin to appear at temperatures greater then 400C, growing until they coalesce to become a
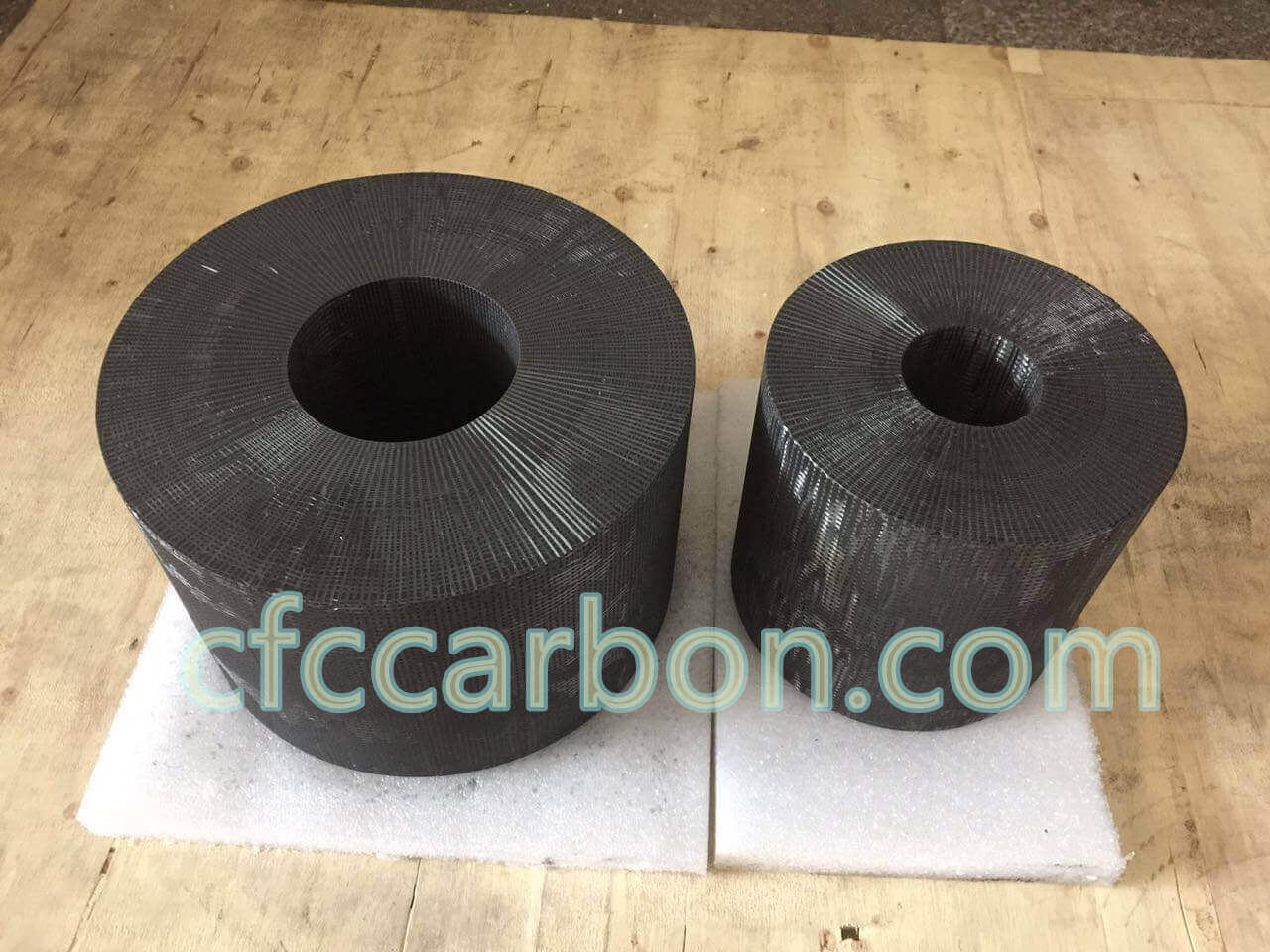
3D 4D 5D Hoops, Loop, weaving, stucture, drawing, carbon fiber, carbon, composite, CFC, CC, manufacturer, China, (1)
continuous phase. At this stage, a preferred orientation of large numbers of these liquid crystals imparts a directionality or anisotropy to the properties of the resultant coke. Maintaining the temperature for longer times results in the viscosity increasing rapidly until the pitch becomes a brittle, predominantly crystalline solid. Pitch-based matrices, when graphitized, are dense (about 1.9g/cm3)
Carbonization of isotropic coal tar or petroleum pitch produces a 50- or 60- percent coke yield under atmospheric conditions. However, if the carbonization is performed very slowly or under high pressure (200Mpa), the coke yield can be increased to 70-80 percent. If the 100-percent mesophase pitch, first produced from an initially isotropic pitch, is stabilized before carbonization, an even greater yield, up to 92 percent, can be achieved.
The microstructure of carbonized cokes is influenced by the temperature and pressure history used in the processing. Previous studies have shown that low pressure carbonization, 6.9Mpa, of coal tar pitch produces a needle-like coke texture, in which the mesophase is deformed through bubble percolation. However, under high pressure (68Mpa), the coke has a mosaic anisotropic texture, and gas formation is suppressed. Under high pressures the mesophase forms at lower temperatures. At even higher , 200Mpa, coalescence of the mesophase does not occur.
High-pressure impregnation/carbonization forces thermoplastic pitch into very small fissures and cracks generated during previous carbonization/graphitization steps. Using pressures up to 207Mpa reduces the temperature associated with the thermal degradation and improves the carbon yield by reducing the loss of volatiles. The effect of pressure increased the viscosity of any liquid. The effect produces a less compliant thermoplastic, more matrix cracks, and a smaller and more reactive graphitic structure. Conversely, the retention of the volatiles tends to decrease the viscosity, producing a more compliant matrix.
related news /articles:
Liquid phase infiltration of CC composites (2)—thermoset resin matrices
Methods of processing carbon-carbon materials (1)- gas phase
Gas phase infiltration of carbon carbon composites-CFCCARBON LTD
3D carbon-carbon composite application for liquid rocket engine (1)