The need to increase the payload capacity of the current launchers drives rocket engine manufacturers to seek higher thrust level, specific impulse and thrust to weight ratio. The use of high temperature C-C composite materials is an efficient way to reach these objectives by allowing use of high expansion ratio nozzle extensions benefiting of the outstanding thermal, mechanical and fatigue resistance of these materials to decrease mass and featuring high temperature margins.
Up to the mid 90s, the use of 3D carbon-carbon composite or carbon-silicon carbon composite (C-SiC) nozzles was limited to solid rocket motors, but challenging performance requirements led to C-C nozzle extension flight qualification on the RL10B-2 engine of the Delta IV upper stage, in the late 90’s, and both materials are planed for use on the next Airiane 5ECB upper stage generation powered with the liquid Vinci engine. Both engines are equipped with very large extendible composite nozzles developed and produced by ASFRAN group.
This article describes the technological background of Snecma Propulsion Solide in the design, materials and manufacturing of high temperature composite nozzles inherited from solid rocket motors and extended to liquid rocket engines. It provides an up-to-date status of the demonstrations already performed on different liquid rocket engines and details all of the recent progress on technical and manufacturing performance. The manufacturing process has also been improved and simplified in order to allow the manufacturing of large scale nozzles at lower cost.
Finally, this paper establishes that this high temperature composite technology of Snecma Propulsion Solid is efficient compare to metallic alloys in competition, mature and industrial to be implemented on existing or future rocket engines.
To increase the performance of its solid rocket motors for strategic ballistic missiles, Snecma Propulsion Solide started to develop carbon-carbon composites back in the early 70’s. Carbon-carbon was developed at first for brake applications. The performance of the material appeared to be of high interest for rocket engines, not only for large nozzle throats of SRM, but also for lightweight exit cones for both liquid rocket engines and solid rocket motors. In particular the manufacturing process was found very promising to manufacture large and thick nozzle throat components on one hand and large and thin bell shape exit cones on the other hand, with integrated stiffener capability.
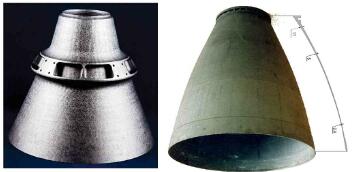
CC nozzle extensions with integrated stiffener(left) and wall thickness variation (right)
In 1989, carbon-carbon/silicon carbide nozzle extension was evaluated for the first time on an operational cryogenic rocket engine. A scale one carbon-carbon/silicon carbide nozzle extension has been tested on the HM7 engine. Tests were successfully conducted at simulated altitude, during 1650 sec cumulated duration in two burns. No active cooling was implemented and a wall temperature up to 2000K was observed although no material degradation was noticeable.
Although the introduction of a large nozzle extension was considered as the most risky element among the development of the RL10B-2 components, finally, thanks to the selection of the C-C the development of the nozzle extension has been by far smoother and quicker than all of the other modifications of the RL10 engine elements.
An huge new industrial furnace was set up and become operational in less than 18 months. A total of 76 carbon-carbon nozzle extensions have been manufactured and shipped to the customer in support of the RL10 B-2 program without experiencing any critical flaw.
Up today this C-C nozzle extension has contributed to the success of al Delta IV missions, including the Heavy version, mostly for US government satellites.