The CVI (Chemical Vapor Infiltration) process for carbon deposition uses volatile hydrocarbon compounds such as methane, propane, or benzene as precursor gases. Thermal decomposition of any of these gases is achieved on the hot surfaces of the C/C composite, resulting in a deposit of pyrolytic carbon and the emission of volatile by-products, which consist mainly of hydrogen.
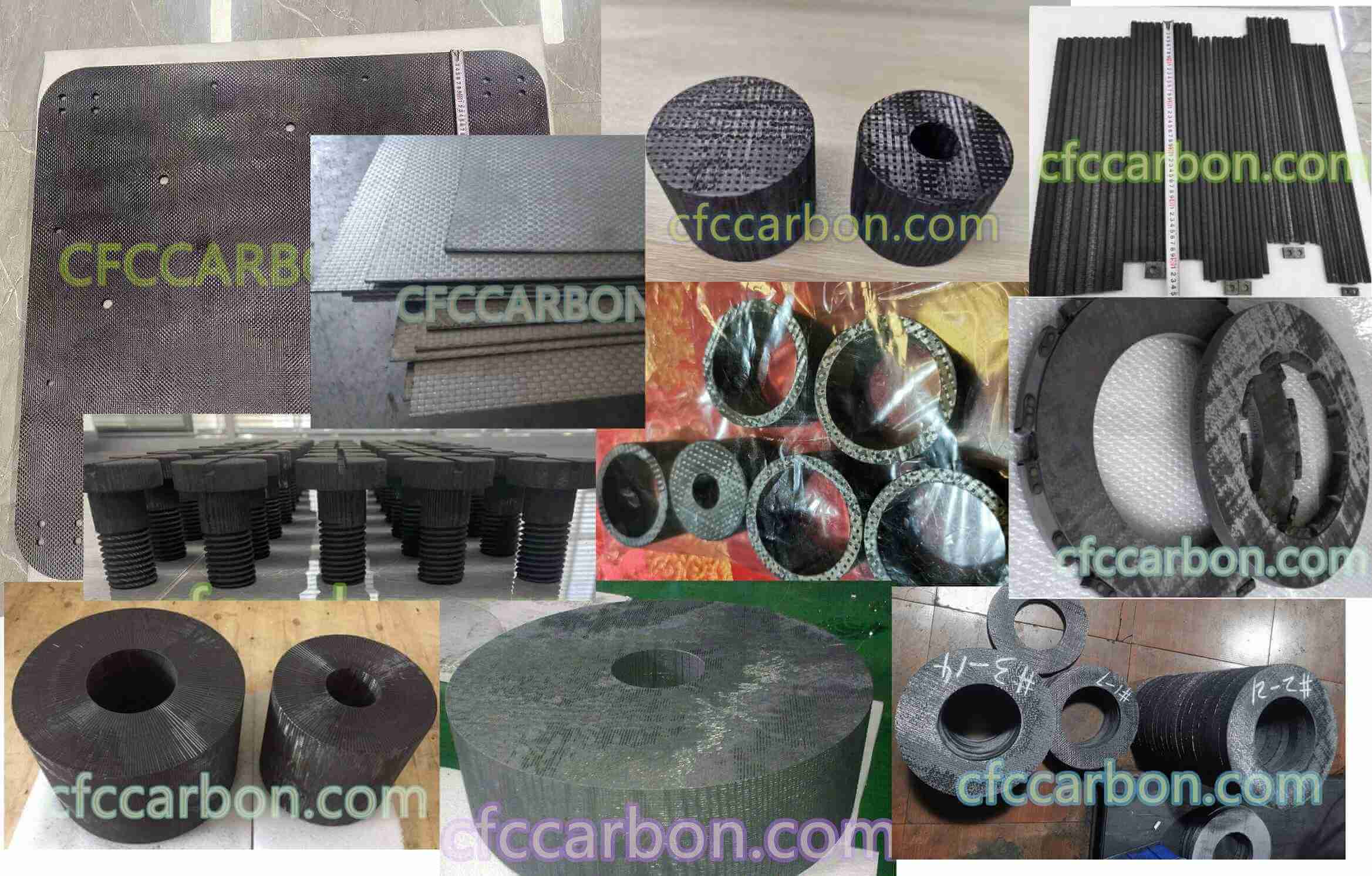
carbon fiber composite material manufacturer in China(1)
One of the problems associated with CVI is that under isothermal conditions, pyrolytic carbon deposits preferentially on the surface of the C/C composite; such deposits change open porosity to closed porosity and make the filling of internal pores difficult. Surface deposits always tend to build up rapidly if diffusion of the reacting gases to the deposition surface is allowed to control the overall reaction rate. This effect can be reduced, however, if chemical reaction on the external surface and inner surface is the rate controlling step. Studies indicate that low temperatures tend to limit reaction while having relatively little effect on diffusional transport. Reaction rate control of the deposition process and hence more complete densification is therefore favored by low temperatures. Factors that influence the structure, uniformity, and rate of deposition of the CVI matrix include the nature of the C/C composite, the carrier gas temperature, the composition, the pressure, and the geometry (particularly the thickness) of the final structure.
Typical effects, illustrate how the microstructure of the CVI carbon deposit can be made to vary from columnar
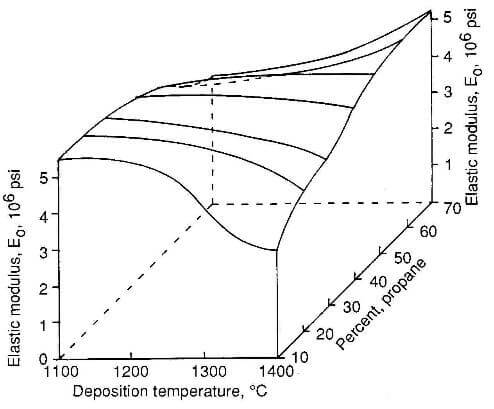
variation of elastic modulus with depositon conditions from propane
through laminar to isotropic by altering the gaseous composition and deposition temperature. Essentially, high-temperature, low-propane concentrations favor isotropic deposits, and low-temperature, high-propane concentrates favor a columnar structure. Others showed that isotropic deposits can be formed at temperatures less than those indicated (<1000C). Figure 6 also illustrates how the elastic modulus of the CVI deposit varies with processing conditions. A smooth laminar deposit seems to be the preferred deposit if the modulus is maximized.
The effect of pressure has been studied. In this case, the required laminar deposit can be maintained at higher temperatures if deposition is carried out at higher pressure. cfccarbon.com. There are three methods of forming CVI carbon: isothermal, thermal gradient, and pressure gradient.
Isothermal chemical vapor deposition
In this process, a woven structure is placed within a furnace susceptor and is heated uniformly. The pressure and the temperature of the furnace are kept constant at typical values of 1psi and 1100C, respectively. The flow rate of hydrocarbon gas is predetermined depending on the surface area of the C/C composite. Intermittent machining of the surface is required because area of the chemical vapor deposition technique leaves a crust on the outer surface of the C/C composite. The machining cycle is repeated until the desired density is achieved.
Thermal-gradient chemical vapor deposition
In this technique, a carbon preform is supported on a mandel. Inductive coils heat the surface of the mandel to a temperature of about 1100C. The hottest portion of the C/C composite is in contact with the mandrel, while the other side, in contact with the reacting gas, is cooler, a thermal gradient through the C/C composite thickness is created. As the hydrocarbon passes through the furnace at atmospheric pressure, carbon is deposited on the hottest region of the woven structure. This hot section migrates through the thickness of the structure as the densified region grows toward the colder surface. This technique prevents the formation of a crust on the outer surface of the preform; thus, the machining step is eliminated. Unfortunately, the process tends to be restricted to large individual parts.
Differential pressure chemical vapor deposition
Differential pressure CVD is a variation of the isothermal technique in which the inner portion of the fiber preform is sealed off from the furnace chamber at the base. Hydrocarbon gases are fed into the inner cavity at a positive pressure with respect to the furnace chamber. A pressure difference that forces the hydrocarbon to flow through the pores depositing carbon and exiting as hydrogen is created across the wall of the structure. This technique also prevents the formation of an outer crust on the surface of the preform and facilitates densification uniformity.
Different kinds of Chemical Vapor Deposition –CVD
Methods of processing carbon-carbon materials (1)- gas phase
Recommended terminology for the description of carbon as a solid (5)
CVI CVD Carbon Carbon Composite Material, Manufacturer in China