Rayon precursor fibers were pyrolyzed to form the first high-strength carbon fibers. However, currently less than 1 percent of all carbon fibers are produced this way. The molecular structure of cellulose, a naturally occurring polymer found in wood pulp and cotton, is shown in figure 7.
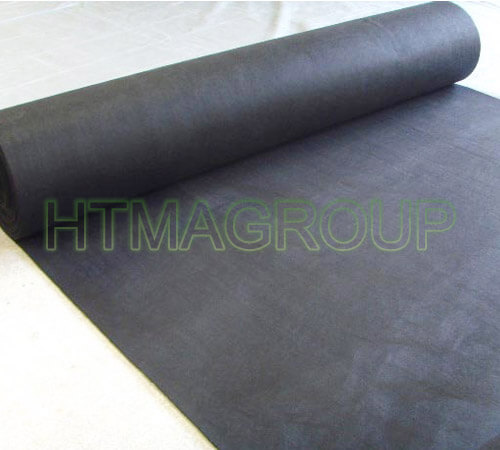
rayon based graphite felt
A wet-spinning process produces these cellulose precursor fibers. To form the solution needed for wet spinning, raw cellulose is dissolved in a basic solution and then treated with CS2 to form cellulose xanthate. This soluble derivative of cellulose then is dissolved in NaOH and extruded through a spinnerette into a coagulation bath containing 10-15 percent sulfuric acid. As the cellulose xanthate enters the acidic bath, it is hydrolyzed, and cellulose filaments precipitate. The surface of these precipitated cellulose filaments is crenulated, a characteristic of wet-spun fibers.
Unlike PAN precursor fiber, cellulose fiber does not need to be oxidized in order to render it infusible. Nevertheless, because oxidation significantly improves its carbon yield, the cellulose precursor fiber is oxidized by heating it in air to temperatures as high as 400C. Initially, as the fiber is heated, the physically absorbed water is desorbed. As heating continues, additional water is evolved because of the reaction of hydroxyl groups in the cellulose. Finally, as the cellulose begins to decompose, CO2, CO, and water are given off, and aromatization of the structure begins. Because the cellulose polymer decomposes as it is stabilized, prestretching or stabilizing under tension is ineffective.
After being stabilized, cellulose precursor fibers are carbonized and graphitized in an inert atmosphere at temperatures similar to those used for PAN. However, because the cellulose molecules in the precursor fiber lose most of their axial orientation during pyrolysis, the fibers are strained at this temperature to increase the preferred orientation and improve the final mechanical properties. The filaments are quit plastic at high temperatures and can be stretched as much as 150 percent. When stretched 100 percent during graphitization at 2800C, fibers with a modulus approaching 720Gpa can be formed. However, if the same fibers are graphitized (but not stretched) at the same temperature, they attain a modulus of only 72Gpa.
The overall yield for converting the cellulose precursor fiber to carbon fiber ranges from 10 to 30 percent, compared with 40-50 percent for the PAN precursor. This low yield is the direct result of the low carbon content of cellulose and the extensive decomposition that occurs during stabilization. This low conversion, especially when coupled with the expense of the stretch-graphitization, accounts for the high cost of rayon-based carbon fibers.
related news /articles:
Introduction of manufacturing of carbon fibers-Pan-based carbon fibers
Carbon fiber reinforced silicon carbide composites (C/SiC, C/C-SiC)-(1)
Introduction of carbon carbon composite, CFC, Carbon composite, C/C,
Continuous and discontinuous carbon fiber composites