Addition of a matrix to carbon fiber, either through the carbonization of an organic precursor or by the deposition of pyrolytic carbon, is conducted at 800-1500C. Subsequent heat treatment of the composite material may involve temperature to 3000C.
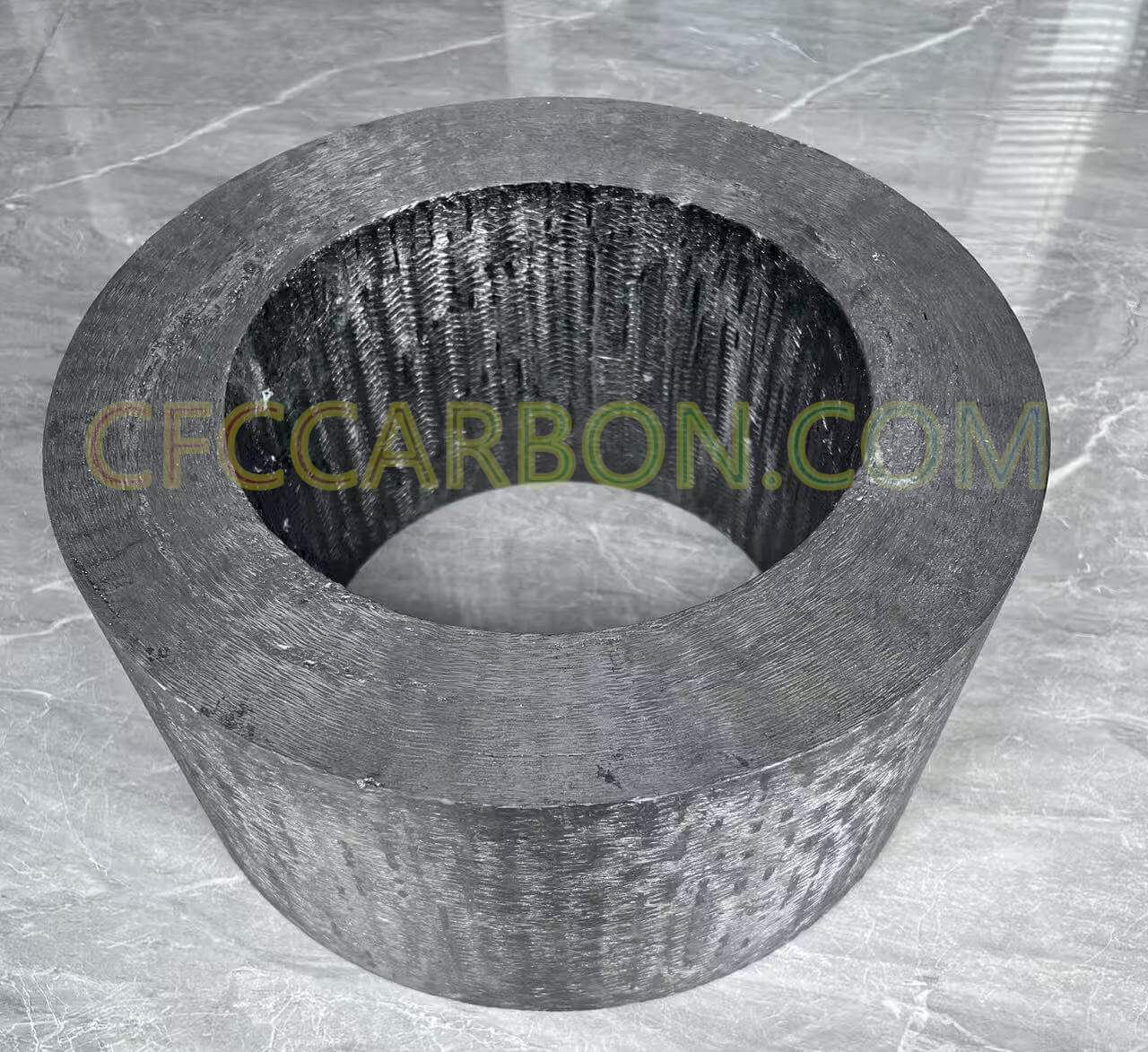
high performance carbon fiber composite mould-2D structure-material manufacturer China
Discontinuous fiber composites:
Fabrication of discontinuous fiber composites uses short carbon fibers conbined with either a pyrolytic carbon or pyrolyzed organic matrix. This approach to CC composites generally does not have true fiber reinforcement as an objective. Rather, discontinuous fiber substrates have been used to: (1) increase fabrication capability of large-scale structures, (2) achieve a more nearly isotropic material, (3) increase the composite interlaminar tensile strength, and (4) along with continuous filament substrates, abtain a stronger composite by providing additional nucleation sites that serve to reduce composite porosity.
The fabrication techniques most widely applied are carbonized, rayon felt substrate with a pyrolytic carbon matrix, and short, chopped fibers in a pitch-based matrix. Felt is produced through the mechanical carding of viscous rayon fibers to produce a continuous web of fibers. The webs are folded one on top of another to produce a batt. The batts are then cut, stacked, and needled to produce the required felt. The rayon felt is subjected to a controlled carbonization cycle in an inert atmosphere or vacuum; The maximum temperature determines such factors as shrinkage, weight loss, and chemical composition of the felt. A maximum carbonization temperature of 1200C is a nominal standard; the length of the carbonization cycle and rate of temperature rise are dictated by the thickness of the felt. Carbon content in the fibers is about 98%. Carbon-carbon composites have also been fabricated from short carbon fibers using isotropic casting, flocking lay-up, spray lay-up, and pulp-molding techniques. The rationale for using these short fibers is to reduce composite properties of anisotropy, specifically, the effect that relatively long fibers used in other discontinuous fiber substrates produce fiber alignment during processing resulting in anisotropic composite properties.
Continuous fiber composites:
Continuous filament substrates use either the properties of high-strength filaments or achieve a high degree of
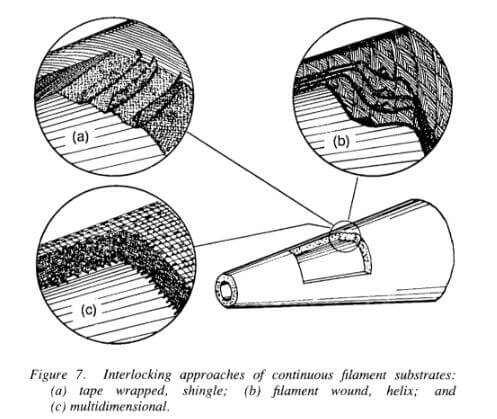
intelocking approches of continuous filament substrates
preferred orientation on the macroscale of the matrix. The fabrication complexity involving continuous-filament substrates is by two parameters: the dirctionality of the filaments and the amount of layer interlocking achieved in the substrate. The plies and filament winding of unidirectional tapes can be used to achieve a highly oriented substrate, usually with no interlocking between layers. Woven fabrics are used to form a two-dimensional laminate with no interlocking between layers. Helical filament winding, which is directional, results in continuous, adjacent layer interlocking. Multilayer locking is achieved through complex weaving patterns or yarn placement resulting in “multidirectional” substrates. (fig 7)
CFCCARBON LTD is the top manufacturer of carbon carbon composite | C/C composite in china, with stable and reliable quality. Our products: 2D,2.5D,3D,4D carbon composite, with density from 1.40-1.95g/cm3, with CVD, CVI processing, or pitch based carbon composite. also, we produce carbon ceramic composite material and products.
related news /articles:
Discontinuous reinforcement of CC composite materials
Filament wound carbon carbon (C/C) composite
Carbon fiber reinforced silicon carbide composites (C/SiC, C/C-SiC)-(1)
Classification of carbon-carbon composite preforms / structures