Innovations in Carbon-Carbon Composite Internal Coatings: Enhancing Oxidation Resistance for Extreme Environments
By CFC Carbon R&D Team | May 17, 2025
1. What Are Carbon-Carbon Composite Internal Coatings?
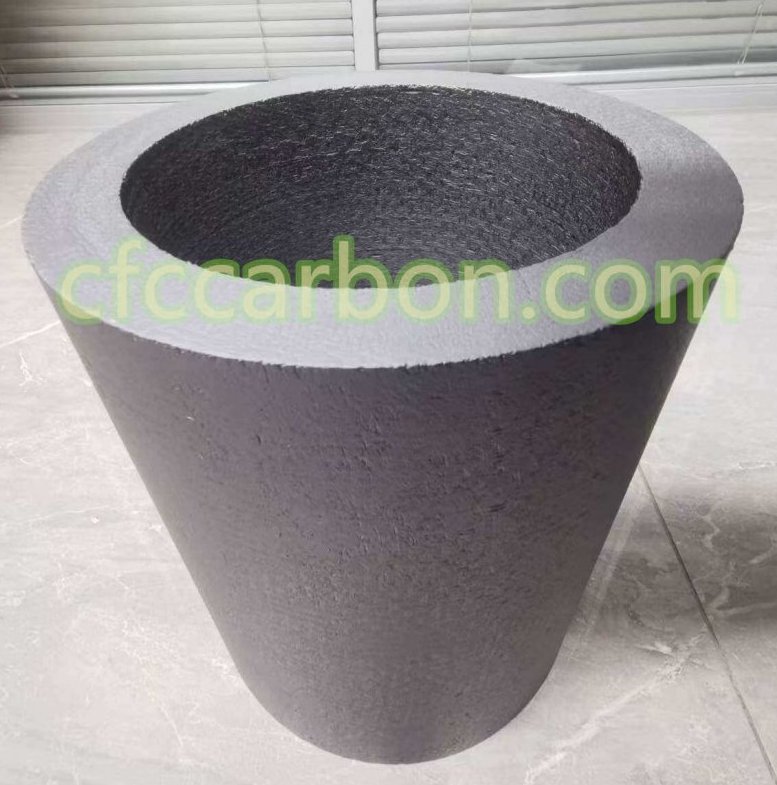
SiC coating carbon fiber composite material-CC-CFC (2)
Carbon-carbon (C/C) composite internal coatings refer to advanced protective layers applied to the porous microstructure of carbon-fiber-reinforced carbon matrices. Unlike traditional surface coatings, these treatments penetrate the material’s internal voids and channels, forming diffusion barriers that inhibit oxidation at temperatures ranging from 750°C to 2,300°C79. At CFC Carbon, we specialize in integrating such coatings through methods like chemical vapor infiltration (CVI) and liquid precursor impregnation, ensuring full densification and thermal stability for aerospace and industrial applications.
2. Manufacturing Techniques: Precision Engineering for Maximum Durability
2.1 Core Production Methods
-
Liquid Precursor Impregnation: Enables deposition of boride/phosphorus-based glass layers within pores, blocking reactive oxidation sites. This method supports diverse inorganic coatings, including B₂O₃-rich glasses that self-heal under thermal stress.
-
Chemical Matrix Modification: Transforms the carbon substrate by introducing silicon carbide (SiC) or zirconium diboride (ZrB₂) transition layers via in-situ reactions, enhancing interfacial adhesion.
-
Chemical Vapor Deposition (CVD): Ideal for creating non-oxide ceramic coatings (e.g., TaC, HfC) within thick-section components, ensuring uniform protection without compromising structural integrity.
CFC Carbon’s proprietary hybrid densification process combines resin prepregging with CVI cycles, achieving material densities up to 1.95 g/cm³—a benchmark in high-performance C/C composites.
3. Product Classification: Tailored Solutions for Diverse Needs
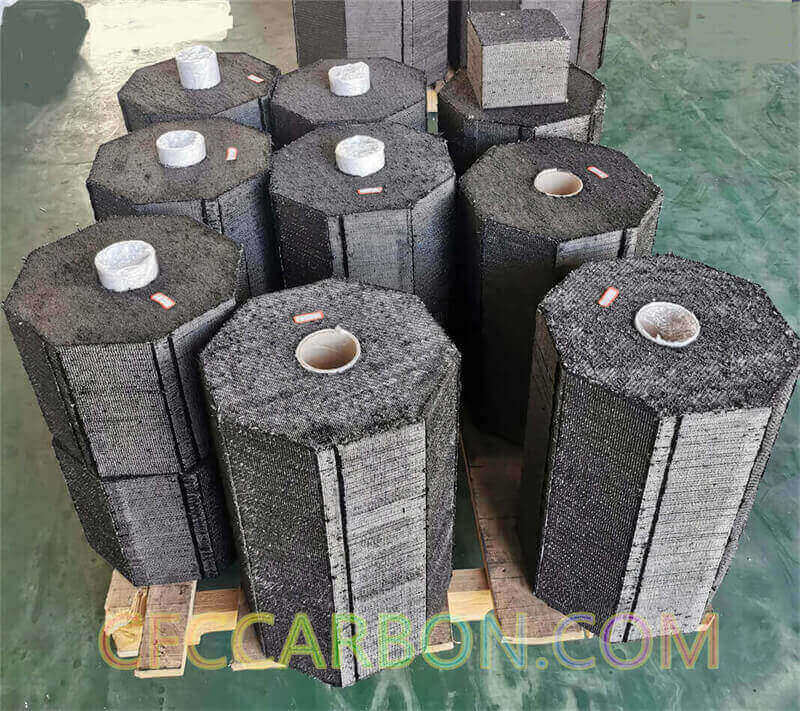
3D 4D CFC carbon fiber composite preform-preforming-Prefab (3)
3.1 By Coating Material
-
Ceramic-Based: SiC/ZrB₂ multilayer coatings for hypersonic vehicle leading edges (2,000°C+ resistance).
-
Glass-Forming: Boro-phosphatic glasses for low-temperature applications (500–900°C), used in brake discs and industrial seals.
-
Metallic Infiltration: Copper-impregnated graphite for mechanical bearings, combining lubrication and oxidation resistance.
3.2 By Fiber Architecture
-
3D Orthogonal Weave: Standard for thermal structural components, offering balanced strength and cost efficiency.
-
4D/5D Reinforced Preforms: Enhanced interlaminar shear strength for rocket nozzles and nuclear reactor cores.
4. Performance Advantages: Why Internal Coatings Matter
-
Oxidation Resistance: Multi-phase coatings reduce mass loss by 80% at 1,500°C compared to uncoated C/C.
-
Thermal Shock Tolerance: Gradient SiC-ZrB₂ layers minimize CTE mismatch, surviving 100+ thermal cycles.
-
Mechanical Stability: Nanotube-doped coatings improve interlaminar shear strength by 40%.
-
Cost Efficiency: CFC Carbon’s optimized CVI cycles cut production time by 30% while maintaining densities >1.9 g/cm³.
5. Industrial Applications: From Aerospace to Energy
-
Aerospace: Leading edges, nose cones, and re-entry shields for spacecraft (e.g., legacy Space Shuttle RCC panels).
-
Automotive: Next-gen carbon-ceramic brake systems for hypercars like Bugatti Chiron.
-
Energy: Nuclear reactor moderators and plasma-facing components in fusion reactors.
-
Industrial: High-temperature fasteners and furnace components with copper-resin hybrid coatings.
6. Future Outlook: Smart Coatings and Sustainable Production
CFC Carbon is pioneering self-monitoring coatings embedded with carbon nanotubes (CNTs), enabling real-time oxidation tracking via electrical conductivity changes13. Additionally, our R&D team is advancing eco-friendly precursor systems to reduce pyrolysis emissions by 50% by 2030.
About CFC Carbon
As a global leader in carbon composite manufacturing, CFC Carbon (cfccarbon.com) provides cutting-edge C/C solutions for defense, aerospace, and energy sectors. Our ISO-certified facilities in Beijing utilize AI-driven quality control to deliver products with ≤0.1% porosity—meeting the strictest MIL-STD specifications.
Explore our technical portfolio:
related news /articles:
High-Performance Coatings for Carbon fiber Carbon Composites
Introduction of high-temperature coatings on CC composite material
Advanced Protective Coatings for Carbon-Carbon Composites
Advanced Coatings for Carbon fiber Carbon Composites