Revolutionizing Extreme Environments: High-Performance Coatings for Carbon-Carbon Composites
*2025-05-16 | CFC CARBON CO., LTD*
1. What Are Coatings on Carbon-Carbon Composites?
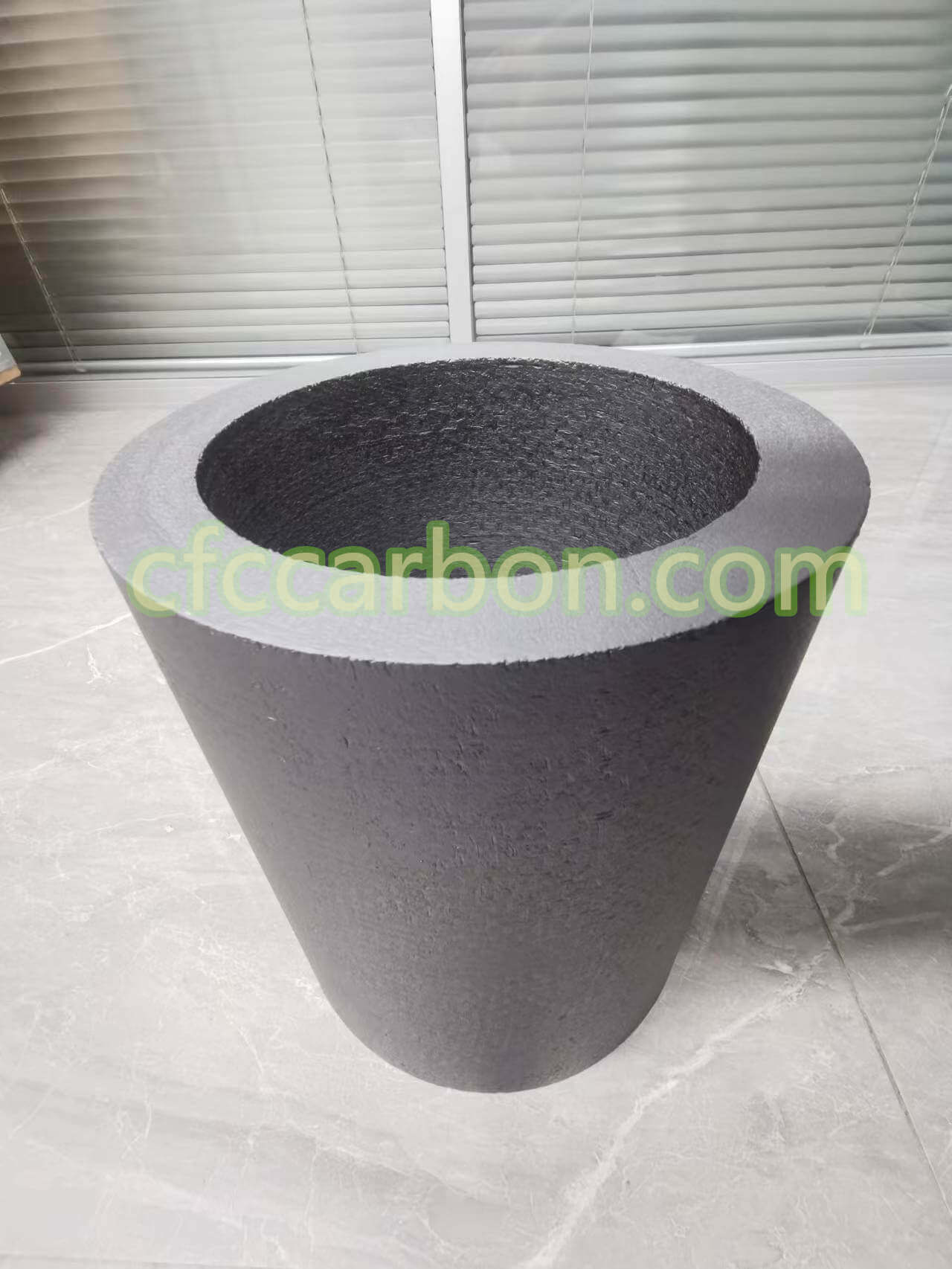
SiC coating carbon fiber composite material-CC-CFC (2)
Carbon-carbon (C/C) composites, formed by reinforcing carbon matrices with carbon fibers, are renowned for their lightweight nature (density <2.0 g/cm³) and exceptional thermal stability up to 2500°C9. However, their susceptibility to oxidation above 400°C limits long-term use in aerospace and hypersonic systems. To address this, high-temperature coatings—such as silicon carbide (SiC), hafnium carbide (HfC), and multilayer ceramics—are applied to create oxygen diffusion barriers while preserving mechanical strength.
2. Manufacturing & Classification of Coatings
Production Techniques
-
Chemical Vapor Deposition (CVD): Dominates industrial applications, depositing uniform SiC or HfC layers at 1100–1300°C using precursors like CH₃SiCl.
-
Preceramic Polymer Coating (PPC): Ethyl Corporation’s polymer-based method offers crack-resistant layers, outperforming traditional CVD in thermal cycling tests.
-
Slurry Coating: Combines boron-rich inner layers with SiC outer coatings to seal microcracks, enhancing oxidation resistance up to 1700°C.
Coating Types
Coating Material | Key Properties | Application Temperature |
---|---|---|
SiC | High oxidation resistance, CTE matched to C/C | ≤1700°C |
HfC | Ultra-high melting point (3900°C), ablation resistance | ≥2200°C |
B₄C/SiC | Self-healing via B₂O₃ glass formation | 1200–1600°C |
Iridium | Noble metal barrier against oxygen diffusion | ≤2100°C |
3. Performance Advantages & Applications
Critical Attributes
-
Thermal Shock Resistance: Graded SiC coatings reduce CTE mismatch, preventing delamination during rapid temperature shifts.
-
Ablation Resistance: HfC nanowire-reinforced C/C composites retain 70% interlaminar shear strength at 2450°C.
-
Mechanical Integrity: Coatings mitigate matrix cracking caused by pyrolysis shrinkage, preserving 50% flexural strength post-thermal shock.
Industry Applications
-
Aerospace: Rocket nozzles, re-entry vehicle nose tips (e.g., Galileo probe heat shields).
-
Defense: Hypersonic missile components, aircraft brake systems (30% weight reduction vs. steel).
-
Energy: Thermal insulation for nuclear reactors and high-temperature furnaces.
4. Innovations in Coating Technology
CFC Carbon Co., Ltd. has pioneered 3D-structured coatings for C/C composites, achieving:
-
Multilayer Design: Alternating PyC (pyrolytic carbon) and SiC layers improve fracture toughness by 59%.
-
Nanowire Reinforcement: HfC nanowires in-situ grown on carbon fibers enhance compressive strength by 32%.
-
Eco-Friendly Processing: Renewable lignin-based precursors reduce production costs by 20% while maintaining >99% carbon purity.
5. Case Study: Coated C/C in Aerospace
A recent collaboration with NASA validated CFC’s SiC-B₄C graded coating on C/C composites for the Next Generation Launch Vehicle:
-
Test Conditions: 30,000 kW/cm² heat flux (simulating Jupiter atmospheric entry).
-
Results: Zero mass loss after 120s exposure, outperforming traditional graphite by 300%.
6. Future Directions
-
Smart Coatings: Integration of sensors for real-time oxidation monitoring.
-
Additive Manufacturing: 3D-printed C/C components with embedded coating layers.
-
Bio-Derived Materials: Cellulose-based carbon fibers for improved CTE matching.
About CFC Carbon Co., Ltd
As a global leader in carbon-carbon composites, CFC Carbon specializes in custom-designed coatings for extreme environments. Our products, certified to MIL-STD-810, serve 40+ countries across aerospace, energy, and defense sectors.
Explore our solutions:
related news /articles:
Introduction of high-temperature coatings on CC composite material
Advanced Coatings for Carbon fiber Carbon Composites
Matrix inhibition / coating of CC composite material
pyrolytic graphite crucible plates sheets