Refractory High-Temperature Resistant Material – Graphite Insulation Felt: A Breakthrough in Thermal Management Solutions
Introduction to Graphite Insulation Felt
Graphite insulation felt, a cutting-edge refractory material, is engineered to withstand extreme temperatures while delivering superior thermal insulation. Composed of high-purity graphite fibers or expanded graphite flakes bonded into a flexible felt structure, this material excels in applications requiring heat resistance up to 3,000°C in inert environments. Classified into carbon-based and graphite-enhanced
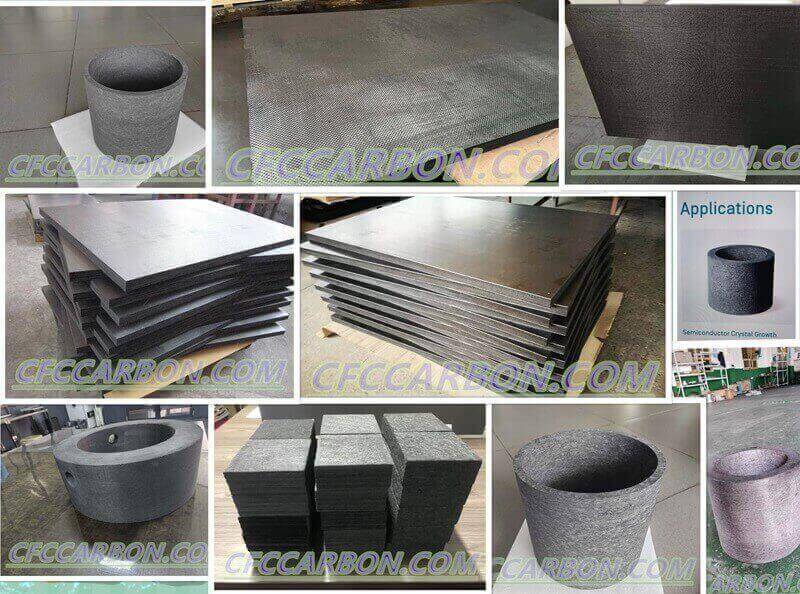
carbon graphite felt insulation soft hard rigid board short long fiber chopped material manufacturer factory China (s)
variants, it combines lightweight flexibility with exceptional thermal stability. As industries such as aerospace, metallurgy, and renewable energy demand more efficient thermal barriers, graphite insulation felt is evolving toward enhanced durability, eco-friendly production methods, and multifunctional integration (source: www.cfccarbon.com).
Production Process: Precision and Innovation
The manufacturing of graphite insulation felt involves a meticulous multi-stage process:
- Raw Material Preparation: High-quality polyacrylonitrile (PAN) fibers or petroleum pitch-based carbon fibers are selected for their purity and thermal properties.
- Pre-Oxidation: Fibers undergo stabilization at 200–300°C in an oxygen-rich environment to ensure structural integrity.
- Carbonization: Treated fibers are heated to 1,200–1,500°C in an inert atmosphere, converting organic components into carbon.
- Graphitization: A critical step where temperatures exceed 2,500°C, transforming amorphous carbon into crystalline graphite for enhanced conductivity and stability.
- Felt Formation: Fibers are needle-punched or laminated into sheets, creating a porous yet cohesive structure.
Unique to this process is the precise control of graphitization, which optimizes the material’s thermal and mechanical performance. Advanced techniques like chemical vapor deposition (CVD) may further enhance density and oxidation resistance.
Unparalleled Properties of Graphite Insulation Felt
- Extreme Temperature Resistance: Withstands temperatures up to 3,000°C in non-oxidizing environments, outperforming traditional ceramics.
- Low Thermal Conductivity: Achieves thermal conductivity as low as 0.03 W/m·K, minimizing heat transfer.
- Lightweight and Flexible: Density ranges from 0.1–0.5 g/cm³, enabling easy installation in complex geometries.
- Chemical Inertness: Resists corrosion from acids, alkalis, and molten metals.
- Thermal Shock Resistance: Maintains structural integrity under rapid temperature fluctuations.
These properties make it indispensable for furnace linings, battery thermal management, and spacecraft heat shields.
Product features:Graphite insulation felt can be stable, long fiber, tensile strength, less slag ball and so on.
1、Low heat capacity, low thermal conductivity
2、High quality thermal stability
3、High quality thermal shock resistance
4、High quality chemical stability
5、Does not contain a conclusion agent and aggressive objects
6、Acoustic quality
Laying fiber usually has two methods: one is to find a layer of plaster, and bolt riveting, generally use the high temperature metal bolt rod in 1222 degrees below 1223 DEG C, using ceramic riveting pieces. On one end of the heating surface is filled with bulk fiber and heat resistant cement. The use of ceramic materials can prevent the carbon deposition caused by fiber modification. The second method is the use of prefabricated assemblies, with carpet stacked precast or 305mm wide carpet folded into a preform accordion. Compared to the two, the latter is the same material, energy saving efficiency is higher, but the cost is higher than that of the latter.
Applications Across Industries
- Metallurgy: Used in vacuum furnaces and ladle insulation to reduce energy consumption by 30% (case studies available at CFCCarbon).
- Aerospace: Protects components in rocket engines and re-entry vehicles.
- Energy Storage: Enhances safety in lithium-ion batteries by preventing thermal runaway.
- Semiconductor Manufacturing: Shields equipment during high-temperature processes.
Future Development Trends
- Nanotechnology Integration: Incorporating carbon nanotubes to boost mechanical strength.
- Sustainability: Recycling waste graphite to reduce environmental impact.
- Smart Functionality: Embedding sensors for real-time thermal monitoring.
Conclusion
Graphite insulation felt represents a paradigm shift in high-temperature insulation, merging flexibility with unmatched thermal performance. As industries push the boundaries of efficiency and sustainability, this material is poised to redefine thermal management systems globally. For technical specifications and custom solutions, visit CFCCarbon.
Cfccarbon ltd is a professional manufacturer of graphite felt, committed to research and development, production and sales of insulation materials and industrial furnace, tunnel kiln design and construction of integrated enterprise, specializing in providing high quality aluminum silicate needled blanket. Companies rely on thermal insulation material of the major scientific research institutions strong technical support.
related news articles:
03-Rigid carbon graphite felt board-data sheet
Chopped fiber /short fiber insulation graphite felt
Properties and Applications of Graphite felt–CFCCARBON LTD
Pan based graphite felt and its applications–CFCCARBON LTD