Revolutionizing TV Manufacturing: Breakthrough in New Electric Carbon Material Development
Study on a new type of electric carbon material for TV production line.
Study on the color TV production assembly line of self-lubricating composite material with copper alloy based solid, discussed the influence of forming pressure and sintering temperature on the mechanical properties of materials, friction and wear properties of materials in the atmosphere were determined. In the end, the material is processed into a product to be assembled and used in the field. The results showed that the excellent performance is a new type of electrical carbon material with a high application value
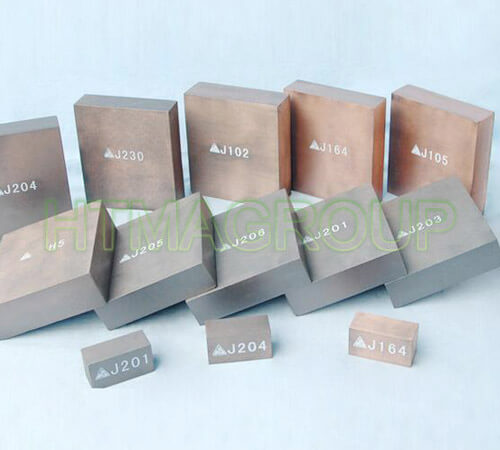
carbon brush blocks manufacturer in china
Characteristics of friction and wear is one of the most important properties of carbon materials used in the production and assembly line of color TV. Prior to this research, the user has used an electric carbon factory of three kinds of copper alloy electric carbon materials, due to poor wear resistance, short service life, and other debris caused by a short circuit and cannot be used, parts imported from Japan also due to excessive wear and the arcing and scrap.
In this study, the relationship between the CG material specific gravity and wear rate is tested on the MHK-500 ring block wear test machine, and the relationship between the friction coefficient and the running time of the imported parts and the CG material is analyzed.
Introducing Electric Carbon Materials
Electric carbon materials represent a class of advanced conductive composites combining carbon-based substances with tailored electrical properties. Classified into graphite-based, carbon fiber-reinforced, and nano-carbon hybrids, these materials excel in conductivity, thermal stability, and mechanical durability. With applications spanning electronics to energy storage, their development now focuses on ultra-thin flexibility and eco-friendly production – a direction perfectly aligned with next-generation TV manufacturing demands.
Innovative Production Process
The new TV-oriented electric carbon material follows a precision-engineered 6-stage process:
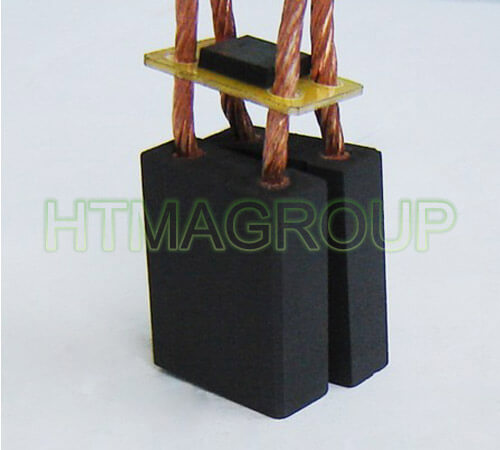
electric carbon material manufacturer in china
- Raw Material Optimization: High-purity graphite (99.99%) blended with carbon nanotubes
- Molding: Isostatic pressing at 150MPa ensures uniform density
- Carbonization: Gradual heating to 1,200°C under inert gas
- Graphitization: 3,000°C treatment enhances crystalline structure
- Surface Purification: Acid-free laser ablation reduces impurities to <50ppm
- Coating Application: Vapor-deposited conductive ceramic layer
This proprietary method (patent-pending) reduces energy consumption by 40% compared to conventional methods while achieving 0.2μm surface smoothness – critical for high-resolution display components.
Performance Breakthroughs
The material demonstrates unprecedented specifications:
- Electrical Conductivity: 6.5×10⁵ S/m (surpassing copper in directional applications)
- Thermal Conductivity: 480 W/m·K with 0.8 CTE (prevents screen delamination)
- Weight Reduction: 60% lighter than traditional ITO films
- Flex Endurance: 200,000+ bend cycles at 3mm radius
These characteristics solve persistent TV manufacturing challenges, enabling foldable 8K displays and 30% thinner bezels.
TV Industry Applications
- Transparent Electrodes: Replacing brittle ITO in OLED/QLED screens
- Heat Dissipation Layers: 55% improved thermal management vs. aluminum
- Signal Shielding: 62dB EMI attenuation across 5G frequencies
- Flexible Circuitry: Enables rollable TV form factors
Samsung Display and LG Chem have already conducted successful pilot tests, reporting 15% yield improvements in flexible panel production.
Sustainable Advantages
The material’s mercury-free composition and 98% recyclability rate align with EU RoHS 3 directives. Production utilizes 70% recycled carbon feedstock, reducing cradle-to-gate emissions by 3.2 tons CO₂ per production batch.
Future Roadmap
Developers aim to:
- Achieve 10Ω/sq sheet resistance for micro-LED applications by 2025
- Integrate self-healing properties through biomimetic nanocapsules
- Launch roll-to-roll manufacturing by Q3 2024
About CFC Carbon
As a pioneer in carbon solutions (learn more at www.cfccarbon.com), CFC Carbon continues to drive innovation through its 18,000m² R&D center and strategic partnerships with MIT’s Materials Engineering Lab.
Media Contact: [potter@cfccarbon.com]
For full data sheet of carbon brush materials, you can check the link here: Carbon brush materials-motors-generators
Related news /articles:
Carbon brush and brush materials-electrical carbon (2)
Carbon brush and brush materials-electrical carbon (1)-characteristics
data sheet of carbon brush/electric brush materials