CC composite oxidize at high temperatures at catastrophic rates. The rates are such that untreated CC composite can’t be used for long or short term applications. Inhibition of CC composite does not slow the rate of oxidation enough to use the composites at high temperature. The use of CC composite at high temperatures thus requires the use of a suitable coating. Coatings exposed to oxidizing environments at high temperatures selectively oxidize elemental constituents to form a protective oxide scale. The protective scale acts as a transport barrier
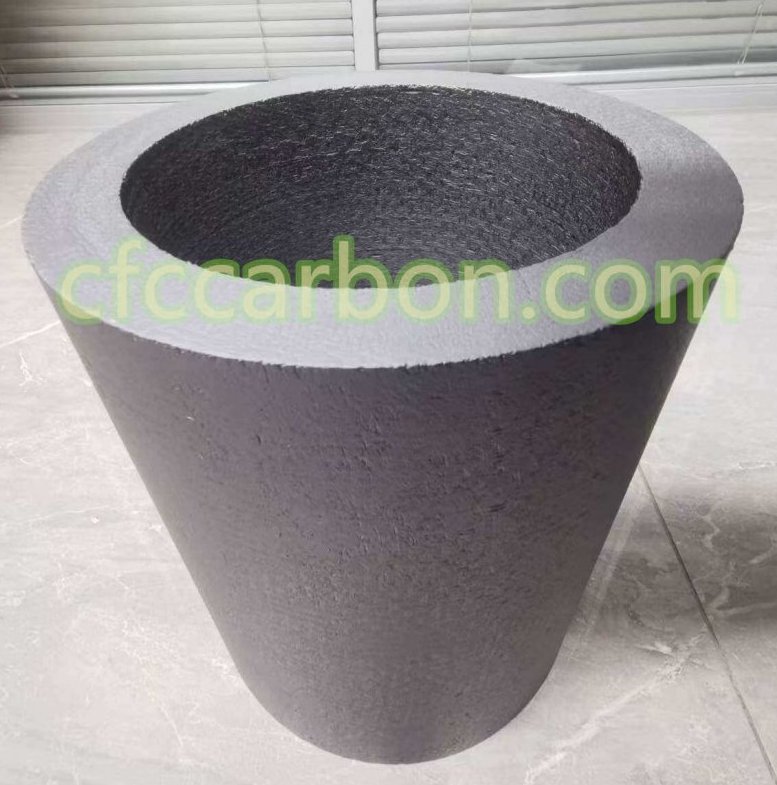
SiC coating carbon fiber composite material-CC-CFC (2)
between the aggressive environment and the substrate. The scale is usually based on the slowly growing scales of Al2O3, SiO2, and Cr2O3.
The current coatings used on CCC are usually based on Si. Silicon reacts with the carbon in low Po2 environments to form silicon carbide, SiC. SiC is a polymorphic line compound that can have a wide range of Si and C thermodynamic activities.
Coatings of SiC on CC composite are applied by vapor deposition processes. In a deposition process where Si is in excess that SiC has a Si activity of nearly 1.0. The other extreme is where carbon is in excess and the SiC has a carbon activity of nearly 1.0. SiC oxidizes very slowly as a result of the formation of SiO2. Many studies of the oxidation behavior of SiC have been published. A brief review of some of this work is useful to better understand of behavior of SiC coated CC composite.
The oxidation mechanisms of a nonoxide ceramic are more complicated than that for a pure metal because the oxidation of both components of such ceramics must be considered. In the case of SiC oxidation, Si reacts to form SiO2, while the C and form CO or CO2 of various pressures. The oxidation kinetics of SiC are often parabolic with time indicating a diffusion controlled reaction. The rate controlling step is controversial and depends on the characteristics of the SiO2 that is formed. Some workers have found that the diffusion of oxygen is molecular form to the SiC/SiO2 interface is the rate controlling step. Other workers indicate that desorption of CO from the SiC/SiO2 interface controls the oxidation rate especially at higher temperatures.
Spear and Tressler have studied the oxidation of green colored single crystal SiC. They found paralolic kinetics at 1200<T<1500C in Po2>0.001 atm. The activation energy for oxidation of Si faces of the SiC was between 53.3 and 71.2 Kcal/mol. The energy for the C faces was 26.7 Kcal/mol at 1200<T<1350C and 62.1 Kcal/mol at T>1350C. The experimental activation energies were in good agreement with the following kinetic equation:
Joxidants(in)=mNB / 2 X0
Where J is the flux of oxidizing species diffusing via interstitials or vacancies; m is a stoichiometric constant that depends on the
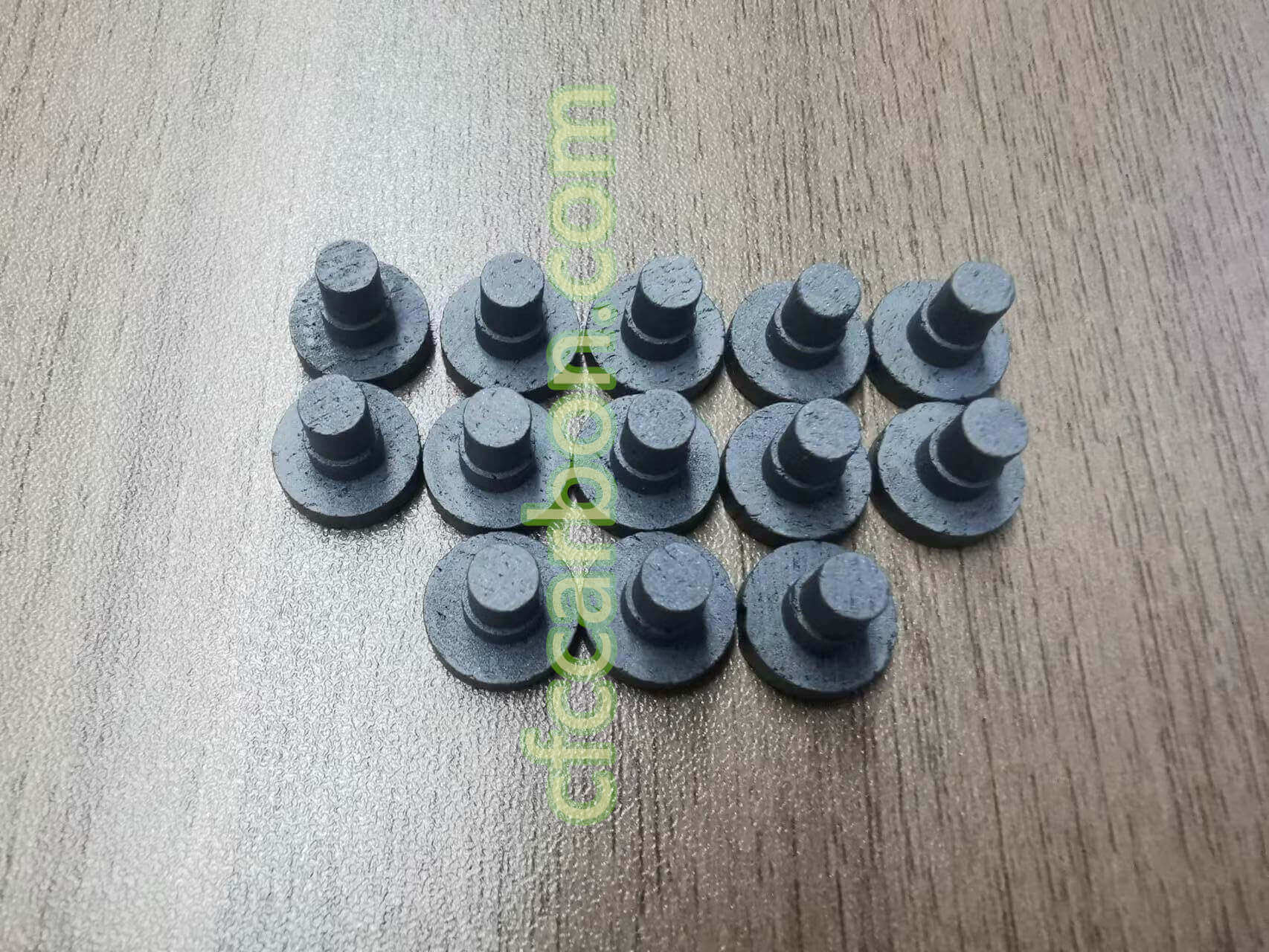
SiC coating carbon fiber composite material-CC-CFC (3)
predominating product species (m=1 for C, m=3/2 for CO, m=2 for CO2); N is the number of oxide molecules in unit volume of SiO2; B is the parabolic rate constant; and Xo is the SiO2 scale thickness. Oxygen diffusion by an interstitial mechanism was believed to be the predominant diffusing species at low temperature. Ionic diffusion of oxygen via vacancies was believed to be the rate controlling step at low PO2.
The oxidation of SiC exhibits an active to passive transition. The transition occurs when SiC is exposed to environments with low PO2. The SiC upon oxidation may form gaseous species like SiO(g), instead of the passivating SiO2. Oxidation under these former conditions is considered to be in the active regime. The passive regime refers to oxidizing conditions where SiO2 forms on the surface of the sample.
Silicon nitride is another Si-based coating that can be used to protect CC composite. Si3N4 usually undergoes parabolic oxidation indicating a reaction controlled by diffusion. Silicon nitride can have different oxidation properties when compared with SiO since the SiO2 that forms can be quite different. Similar to SiC, porosity is often found in the SiO2 scales formed on Si3N4. The porosity is thought to be caused by oxidation products. Silicon nitride reportedly oxidizes faster than SiC at T>1450C. The difference in oxidation rate may be related to impurities. Silicon nitride also erodes faster than SiC and has a higher vapor pressure. A major factor favoring the use of silicon nitride coatings on CC composite is a smaller thermal expansion mismatch than SiC.
related news /articles:
Coating systems for carbon carbon composite material (2)
Friction performance of C/SiC brakes in different environment (10)
Initial characterization of coated carbon-carbon composites
Understanding Oxidation Mechanisms in Carbon-Carbon Composites