The intermediate temperature range, 1400<T<1700C, still requires that the coating be based on SiO2 growth. The growth rates of Cr2O3 and Al2O3 are too rapid at these temperatures to be considered. The coating system in the intermediate range is sensitive to reduction of oxides by carbon. Carbon reduction of oxides causes large pressures of CO to form. Large pressures of CO can cause the coating to crack or even
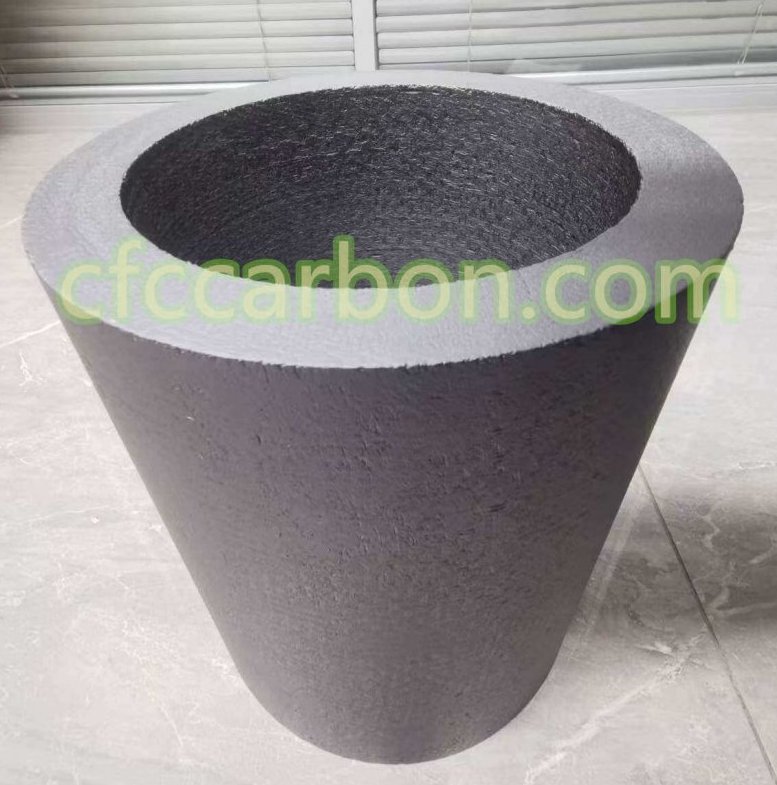
SiC coating carbon fiber composite material-CC-CFC (2)
blow it off. Unalloyed borate glasses are susceptible to carbon reduction at temperature around 1500C. Borate glasses used in this range should, therefore, avoid contact with regions of high carbon activity like the CC composite substrate. At temperatures above 1700C SiO2 is reduced by SiC and Si3N4. This temperature is the upper limit for the use of Si-based coatings as the primary oxygen barrier. Thermal cycling problems still exist in the intermediate range even though the coating and scale should exhibit more plasticity. Only vitreous SiO2 has similar thermal expansion characteristics with the CC composite at these temperatures. Unfortunately the SiO2 devitrifies rapidly at these high temperatures. No simple solution to the thermal cycling problem is currently available. The other problems of oxide scale fluxing and viscosity changes will also be aggravated in this temperature range.
The high temperature regime of T>1800C will require a coating based on something different from SiC or Si3N4. Nonoxide ceramics like HfB2 oxidize in a parabolic fashion. But at rates much too high for practical use. Coatings with these phases would have to be very thick, thus detracting from the attractive properties of the CC composite substrate.
Graphite composites have been made with ZrC, ZrN, and HfB2 additions to achieve oxidation resistance. Oxides have to be considered the primary candidates for oxygen barriers. Of the many oxides available, only HfO2, ThO2, ZrO2, Y2O3, and Al2O3 could be used at T>1800C. Many of these oxides allow oxygen to diffuse through them too rapidly to be considered. These oxides would also have to be in contact with refractory carbides with ac much less than 1.0. Contact with the CC composite substrate would cause reduction of the oxide by carbon. Volatility, chemical compatibility, thermal expansion mismatch, and oxygen permeability are all issues that would have to be solved to obtain a reliable coating.
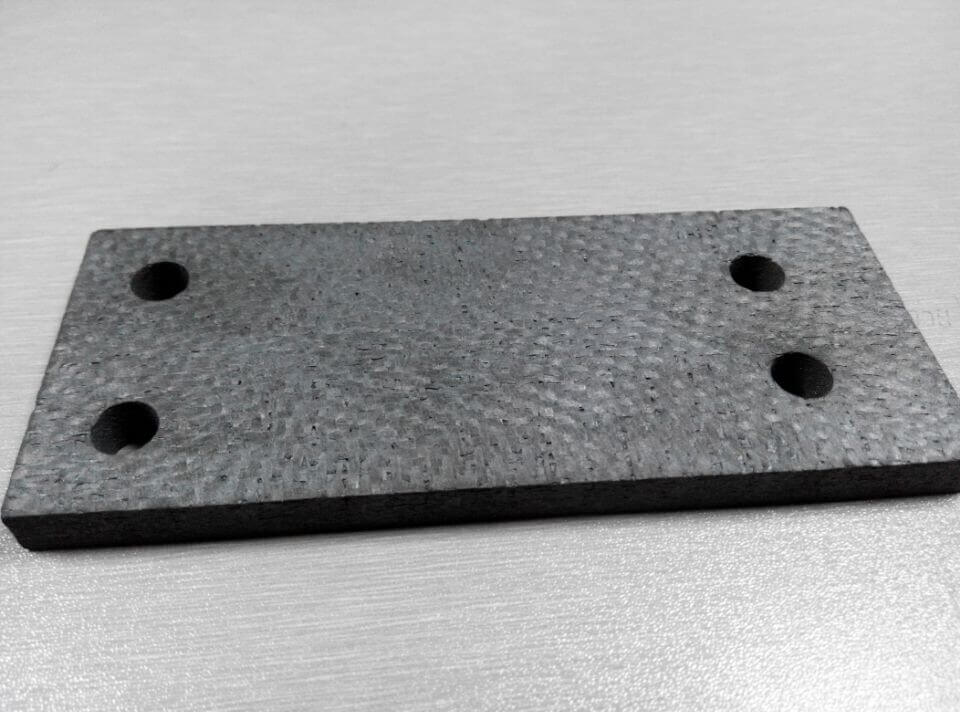
C-SIC
One successful coating in the high temperature range has been discovered. Iridium is essentially impervious to oxygen and does not react with graphite until the eutectic temperature of 2110C. Iridium forms volatile oxides much like Pt. The Ir oxides cause a recession rate of 1 to 10 mil per hour in high velocity gas streams at 2000C.
NASA has done mission simulation testing on some current state-of-the-art coatings. These coatings were SiC-based with various intermediate layers. These workers found that 10 to 20 hour protection could be expected in environments where temperature and humidity were changed to simulate a service mission. Coating adhesion and delamination of CVD layers was the major problem in achieving oxidation resistance.
In summary, the approaches to protect CC composite using coatings have usually involved the formation of SiO2 reaction product barriers with sealants to attempt to overcome the problems arising from cracks in the coatings. The success of such approaches requires more detailed examination than has been performed to date.
related news /articles:
Carbon fiber reinforced silicon carbide composites (C/SiC, C/C-SiC)-(1)
Coatings for carbon-carbon composites (1)-SiC oxidation
Coating systems for carbon fiber carbon composites material (1)
Introduction of high-temperature coatings on CC composite material