Carbon-carbon composites with either pitch+CVI matrix or resin-derived matrix were joined to copper-clad molybdenum using two active braze alloys, Cusil-ABA and Ticusil. The brazed joints revealed good interfacial bonding, preferential precipitation of Ti at the composite/braze interface, and a tendency toward de-lamination in resin-derived C-C composite due to its low inter-laminar shear strength. Extensive braze penetration of the inter-fiber channels in the pitch+CVI C-C composites was observed. The relatively low brazing
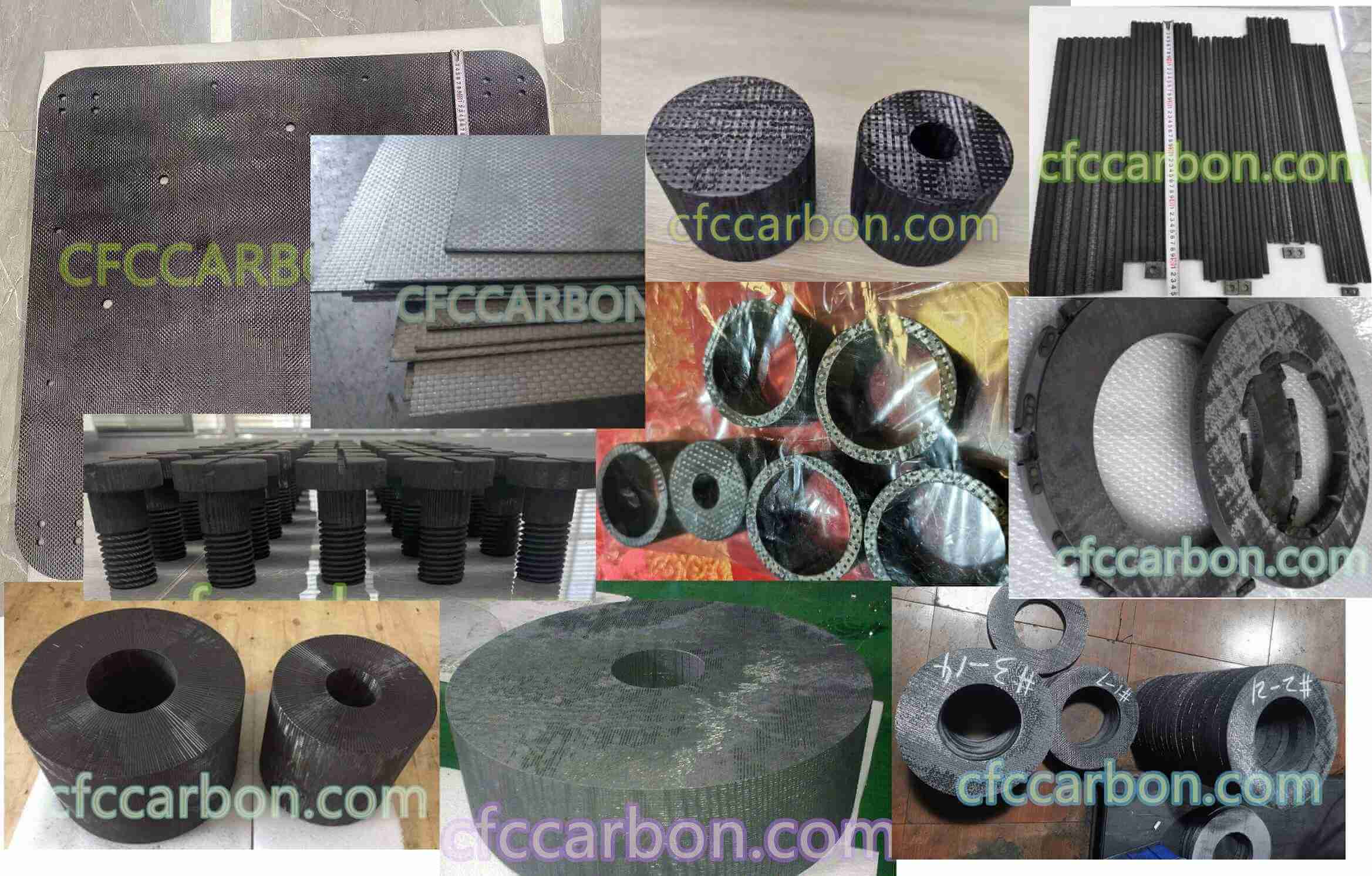
carbon fiber composite material manufacturer in China(1)
temperatures precluded melting of the clad layer and restricted the redistribution of alloying elements but led to metallurgically sound composite joints. The Knoop microhardness distribution across the joint interfaces revealed sharp gradients at the Cu-clad-Mo/braze interface and higher hardness in Ticusil than in Cusil-ABA. These C-C/Cu-clad-Mo joints with relatively low thermal resistance may be promising for thermal management applications.
A number of thermal management applications utilize copper-clad-Mo and copper-clad-invar because of their tailorable thermal conductivity and low thermal expansion properties. However, the high density of these material has limited their use in lightweight heat rejection systems. In order to reduce the weight without sacrificing the thermal conductivity and thermal expansion benefits, copper-clad-Mo has been jointed to graphite and more recently, to C-C composites. Carbon-carbon composite containing high-conductivity carbon fibers provide excellent heat dissipation and low expansion properties at considerably reduced weight. For example, the axial thermal conductivity of high-modulus and ultra-high modulus carbon fibers are about 120-300 W/m.K and 500-1100 W/m.K, respectively. The thermal conductivity of Cu-clad Mo varies with the clad layer thickness and is in the range 138-235 W/m.K for 0 to 30% Cu layer thickness per side of Mo substrate; the condutivity at 30% clad layer thickness is comparable to the conductivity of lightweight aluminum, a good thermal conductor, but slightly inferior to the thermal conductivity of heavier copper with a density of 8940 kg/m3. Acting in combination at a joint, Cu-clad Mo and C-C composite can provide excellent heat dissipation capability at reduced weight compared to the heavier Cu-clad Mo acting in isolation. The coefficient of thermal expansion of Cu-clad Mo varies from 5.6*10-6/K to 11.6*10-6/K for 0 to 30% clad layer thickness whereas the CTE of C-C composites is 2.0-4.0*10-6/K over the temperature range 20-2500°C. Thus, the CTE mismatch between C-C and Cu-clad Mo can be designed to minimize residual stresses during joining and service while still maintaining good thermal conductivity for use in heat rejection systems.
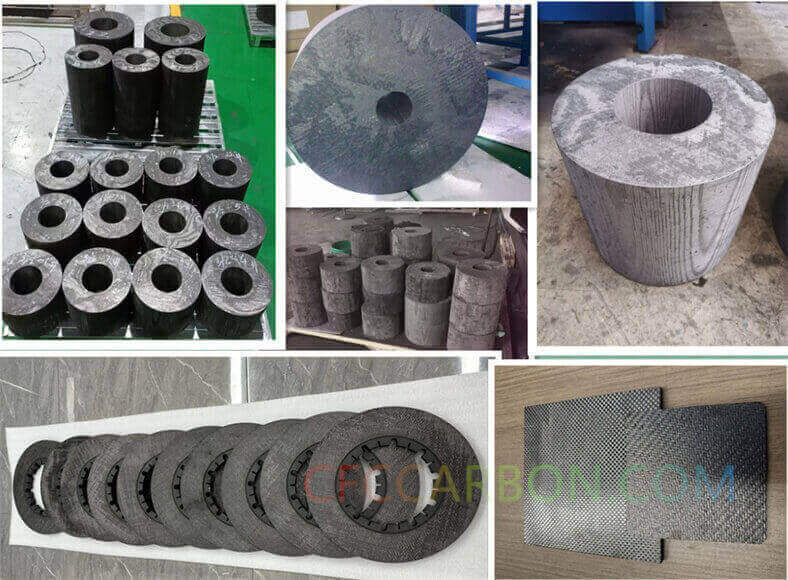
3D 4D carbon fiber composite material manufacturer factory -airplane brake disc plates sheets U L profiles-2D(s)
In a recent study, we had brazed resin-derived C-C composites containing T300 C fibers to Cu-clad-Mo using four active brazes: Cu-ABA, Ticuni, TIcusil and Cusin-1 ABA. In the present work, we report the brazing and joint characterization of 3D C-C composites having pitch+CVI carbon matrices to Cu-clad-Mo for heat rejection applications using two Ti-containing Ag-Cu active braze alloys. The alloys Ticusil and Cusil-ABA have thermal conuctivity either higher than or comparable to the conductivity of braze alloys used in our earlier study. The thermal conductivity of Cusil-ABA is better than that of Cu-ABA and Cusin-1 ABA used in our earlier work. In addition, the ductility of Cusil-ABA is better than the ductility of Cusin-1 ABA and comparable to Cu-ABA. Both Cusil-ABA and Ticusil are Ti-containing active braze alloys that are expected to wet the carbon. In recent publications, we had reported on the use of these and similar brazes to join C-C, monolithic ceramics, and ceramic-matrix composites to various other substrates.
Some comments are in oerder to justify the use of 3D C-C composite with CVD carbon matrices in place of resin-derived matrices used in our earlier work. First, 3D fiber structure overcomes the problems of poor mechanical properties perpendicular to 1D and 2D laminate planes. Second, complex 3D constructions are possible, including those with
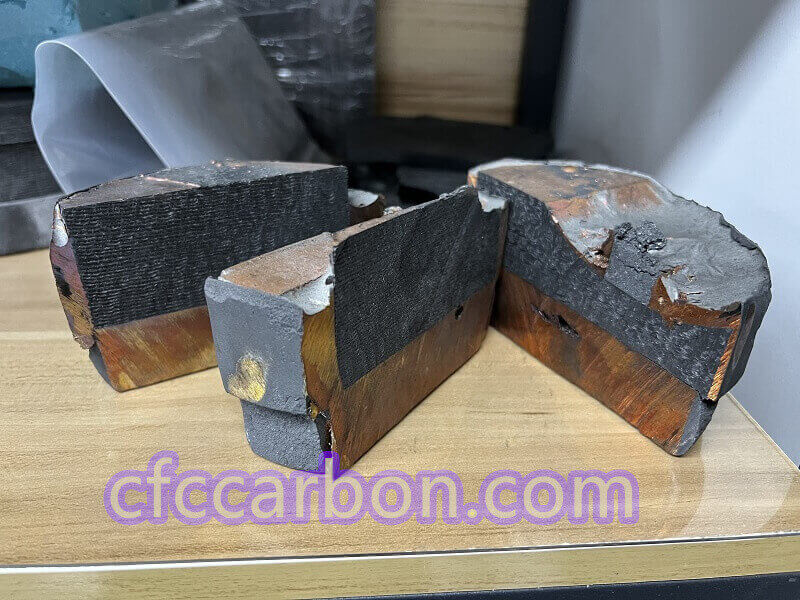
CFC and copper weld parts
yarns oriented on polar coordinates in the radial, axial and circumferential directions. Third, the use of CVI to deposit the matrix carbon offers some distinct advantages. In CVI, carbon is directly deposited onto the fiber surface whereas with liquid resin precursors, the carbon is produced in the void between the fibers after a thermal treatment. The resulting volumetric changes lead to porosity and shinkage cracks in resin-derived carbon matrix when compared to CVI carbon matrix. In addition, because CVI deposites carbon mainly on the fiber surface, it is better suited than precursor-based methods for the production of thin sections which may be needed in thermal management applications. Finally, the thermal conductivity of CVI C-C composites is either comparable to or better than the thermal conductivity of resin-derived composites making the former more suitabe for thermal management applications. In CVI composites, the conuctivity and expansion are determined by the preferred orientation, and their values can approach single crystal graphite values.
In the present study, we investigated the vacuum brazing of CVI 3D C-C composites to Cu-clad-Mo using two Ag-Cu brazes. The presence of Cu as a cladding on Mo and as an alloying additive in the braze alloys is expected to promote the metallurgical continuity across the joint while providing interfacial ductility to mitigate the CTE mismatch induced stresses. A limited number of runs were made with resin-derived C-C composites to generate comparative base-line data on joining response. The brazed joints were characterized using optical microscopy, field emission scanning electron microscopy, energy dispersive spectrometry, and by microhardness measurements.
related news /articles:
Characterizaton of Brazed joints of C-C composite to Cu-clad-Mo (2)
Characterizaton of Brazed joints of C-C composite to Cu-clad-Mo (3)
Joining of C/C composite to metals demonstrated for thermal management applications
Characterizaton of Brazed joints of C-C composite to Cu-clad-Mo (5)