Figures 2 through 6 show the joint microstructure of C-C composite with Cu-clad-Mo. All joints display intimate physical contact at the composite/Cu-clad-Mo interface. The contact region and the braze region are free of common structural imperfections such as interfacial
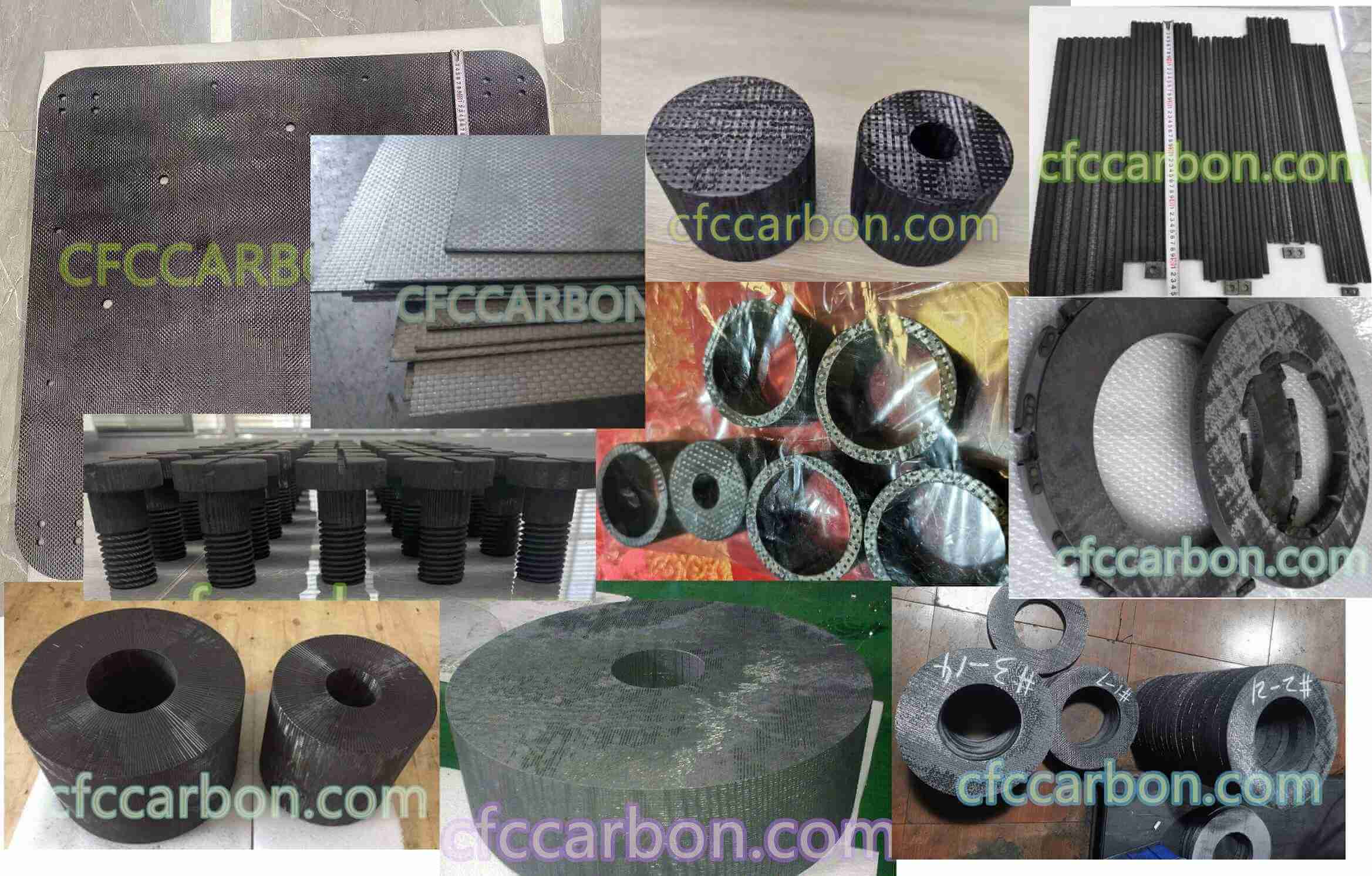
carbon fiber composite material manufacturer in China(1)
microvoids, shrinkage cavities, and micro-cracks. The dissolution of the Cu cladding from the Mo surface has enriched the braze with Cu, and led to the precipitation of a copper-rich phase at the joint- and within the inter-fiber regions. The fiber ply orientation at the joint interface had no influence either on the infiltration distance or the microstructure of the joint.
The EDS elemental compositions at the composite/braze and braze/Cu-clad-Mo interfaces are given in Tables 2 through 9. The distribution of the other major alloying elements across the joint region in different samples is also given in these tables. Only relative atomic percentages among the alloying elements are provided. A higher titanium comcentration is observed at the composite/braze interface than in the nearby regions of the joints. The preferential segregation of Ti at the composite/braze interface is consistent with the high chemical affinity of Ti toward C, which promotes braze spreading and bonding. Improvement in spreading is promoted by the formation of the TiC. The Gibb’s free energy change for TiC formation via Ti+C→TiC at a brazing temperature of 850°C is -171.18kJ, which suggests that TiC formation is possible. The Au-Cu-Ti ternary diagram shows that at the brazing temperatures used, alloys with Ti>5at% yield a Ti-impoverished liquid phase and a Ti-rich liquid phase. It is conceivable that this Ti-rich liquid reacts with the carbon to form the carbides and a metallurgical bond. Besides caride formation, Ti could react with minute amounts of residual oxygen in the furnace atmosphere leading to oxy-carbides and oxides such as the wettability-enhancing, metal-like compound TiO, which is known to form an interfacial layer on carbon.
The interfacial concentrations of Ti are larger in joints made with Cusil-ABA than in joints made using Ticusil. The EDS analyses show that diffusion of Ag, Mo and Ti in the composite matrix in negligible. The braze matrix exhibits a two-phase eutectic structure with Ag-rich light-grey areas and Cu-rich dark areas. In the Ag-Cu-Ti system, intermetallics such as AgTi, Ti2Cu3, and TiCu2 may also form.
The Cusil-ABA/Cu-clad-Mo interface displays evidence of good wetting and somewhat diffuse interface character. The light-grey and dark eutectic micro-constituents are distributed within the braze region. The Cu cladding at the braze/Cu-clad-Mo interface appears to be intact because the joining temperatur is below the melting point of Cu; however, some chemical dissolution has probably occurred at the Cu-cladding/braze interface. Very small quantities of Mo, Ag and Ti have diffused in the Cu cladding and these elements did not lower the liquides temperature sufficiently to cause melting of the cladding; this is evident from a lack of any conceivable sign of solidification microstructure in the clad layer.
Small amounts of Ag and Cu from braze are detected within the C-C composite region but no measurable quantity of Mo is noted. The C-C/Cusil-ABA interface is rich in titanium and the Ti concentration decreases rather systematically with increasing destance from the interface.
In C-C/Cu-clad-Mo joints made using Ticusil, a normal two-phase eutectic structure with a characteristic acicular morphology is observed within the braze region. Some carbon has dissolved in the molten braze, possibly because of the higher brazing temperature of Ticusil which led to C diffusion in the eutectic micro-constituents. In addition, carbon is detected within the Cu-clad-Mo region. Finally, as stated in a preceding paragraph, oxygen could also be playing a role. Upon contact with the molten braze, the scale will dissociate and dissolve, yielding an oxygen-rich braze layer. As a result, besides carbides, oxides such as TiO and TiO2 may also form at the C-C/metal joint because stable oxides of Ti can form at very low oxygen partial pressures.
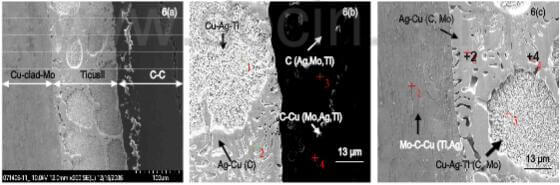
fig.6-C-C composite-Ticusil-Cu-clad-Mo joint showing interfaces
Figure 6 shows joint interfaces between resin-derived C-C composite and Cu-clad-Mo made using Ticusil. Microstructurally sound joint interfaces have formed but there is some cracking within the C-C composites. Ag- and Cu-rich phases have formed in the braze matrix with the Ag-rich phase preferrentially precipitating onto both C-C surface and Cu-clad-Mo surface. A small amount of Cu is detedted within the composite. Both C-C/Ticusil and Ticusil/Cu-Mo interfaces in the joint region appear to be defect-free.
In summary, whereas extensive chemical interactions did not occur and optically visible interfacial reaction layers did not form at the C-C/CuAgTi interfaces in joints, some redistribution of chemical species seems to have occurred. Large titanium concentrations occurred at the C-C/braze interface which indicated that surface modification, presumably a carbide-forming, had promoted the wetting and bonding.