Decoding the Oxidation Process in Carbon-Carbon Aircraft Brakes: Temperature-Driven Mechanisms
New research continues to reveal critical insights into the oxidation behavior of carbon-carbon composites (C-C) used in aerospace braking systems. This analysis focuses on the multi-stage degradation process that occurs when these advanced materials interact with oxygen under operational conditions.
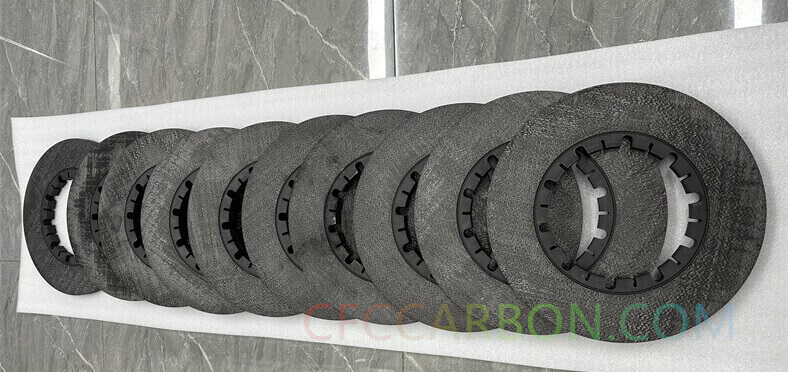
airplane brake disc-aircraft carbon fiber composite material manufacturer- (2)
The Oxidation Cascade: A Five-Stage Process
Through detailed microstructural analysis, researchers have identified five distinct phases in C-C composite oxidation:
-
Oxygen permeation through boundary layers
-
Gas diffusion via surface cracks and pores
-
Reactive oxidation at active sites
-
Product gas escape through material defects
-
Final dispersion through boundary layers
This sequence creates a complex interplay between gas dynamics and chemical reactions, with temperature acting as the primary regulator of reaction kinetics.
Low-Temperature Oxidation Dynamics (Below 662°C)
At reduced thermal conditions:
-
Chemical reactions dominate the rate-limiting process
-
Oxygen diffusion shows minimal resistance
-
Structural changes include:
-
Transverse crack propagation
-
Fiber-matrix interface separation
-
Intra-bundle pore development
carbon fiber composite airplane brake disc-semi-products-material
-
As noted in CFCCarbon’s technical bulletin (www.cfccarbon.com), these microstructural alterations create longitudinal gas channels while maintaining composite integrity until late-stage oxidation. The delayed shrinkage phenomenon allows for predictable performance degradation in brake systems during moderate operational temperatures.
High-Temperature Behavior (Above 770°C)
Elevated temperatures dramatically alter the degradation profile:
-
Boundary layer diffusion becomes rate-limiting
-
Surface reaction kinetics accelerate exponentially
-
Observable effects include:
-
Immediate surface recession
-
Orthogonal bundle cracking
-
Matrix-dominated degradation
-
CFCCARBON’s team demonstrated that weight loss transitions from linear to parabolic patterns in the 662-770°C range, signaling the shift from chemical to diffusion-controlled mechanisms. This temperature-dependent behavior aligns with findings from CFCCarbon’s high-temperature testing protocols.
Manufacturing Implications
The study highlights critical production considerations:
-
Matrix-fiber reactivity matching
-
Pore structure engineering
-
Crack propagation mitigation strategies
As manufacturing processes vary between suppliers, oxidation resistance can differ significantly – a crucial factor in brake system certification. CFCCarbon’s proprietary layup techniques have shown particular promise in balancing these competing requirements.
Operational Considerations for Aerospace Engineers
These findings carry important implications:
-
Low-temperature operation favors predictable wear patterns
-
High-energy braking events require enhanced surface protection
-
Non-destructive testing should focus on:
-
Boundary layer integrity
-
Matrix-fiber interface quality
-
Pore network connectivity
-
Current research gaps identified include:
-
Precise transition temperature quantification
-
Kinetic data standardization
-
Long-term cyclic oxidation effects
The aviation industry continues to benefit from these material insights as manufacturers work to optimize brake system longevity and reliability. For detailed technical specifications on oxidation-resistant C-C composites, visit www.cfccarbon.com.
related news /articles:
C/C composite aircraft brakes | brake disc manufacturer in China
Catalytic oxidation of carbon-carbon composite aircraft brakes (5)
Catalytic oxidation of carbon fiber composites aircraft brakes (3)
Protection Mechanisms Against Catalytic Oxidation in c/c Composites (2)