Understanding Calcium-Catalyzed Oxidation in Carbon-Carbon Aircraft Brakes: Key Mechanisms Revealed
Recent advancements in catalytic oxidation research have shed new light on the behavior of alkaline-earth metals in carbon-carbon (C-C) composite aircraft brakes. A pivotal study by Cazorla et al. demonstrates that calcium-based catalysts exhibit unique interfacial dynamics during carbon gasification processes, offering critical insights for aerospace material engineering.
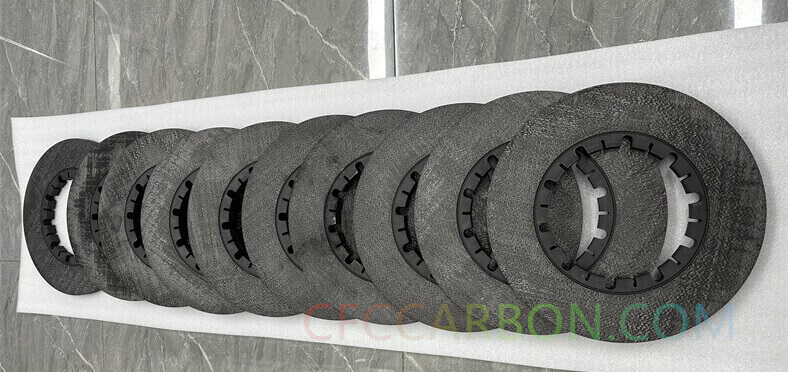
airplane brake disc-aircraft carbon fiber composite material manufacturer- (2)
Experimental Breakthroughs in Calcium Catalysis
Cazorla’s team employed innovative isotopic tracing techniques using ¹³CO₂ to monitor carbon oxidation pathways. Their methodology involved three distinct catalyst-loading approaches on high-purity carbon substrates:
-
Ion-exchange deposition
-
Aqueous impregnation
-
High-temperature sintering
At 800°C under controlled helium/CO₂ atmospheres, researchers observed unexpected ¹²CO dominance during calcium-catalyzed reactions. This phenomenon disappeared at elevated temperatures, challenging previous assumptions about redox cycles in catalytic oxidation. The team’s isotopic desorption experiments revealed enhanced ¹³CO₂ retention at calcium-carbon interfaces, suggesting localized catalytic activity rather than bulk CaCO₃ formation.
Comparative Catalyst Behavior
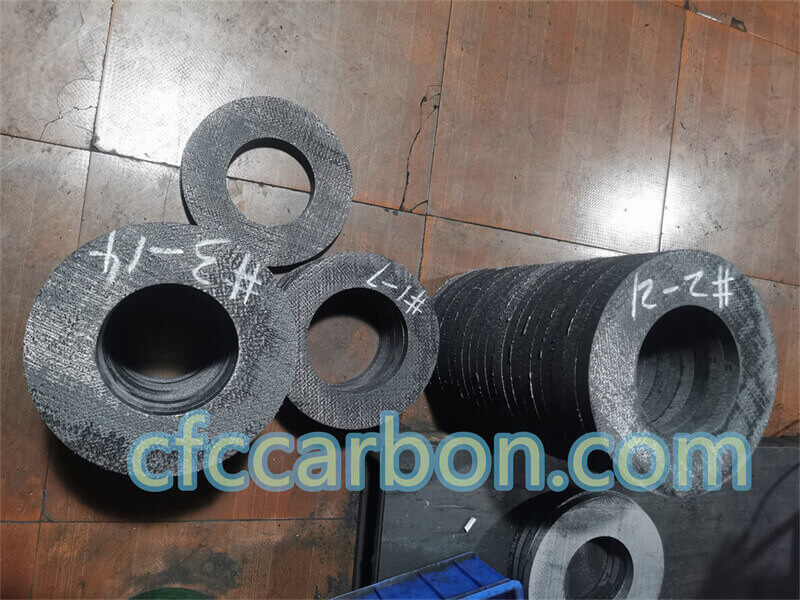
carbon fiber composite airplane brake disc-semi-products-material
The study contrasts sharply with alkali metal catalysis models proposed by McKee and Chatterji. Unlike potassium’s peroxide-mediated mechanisms, calcium’s catalytic action appears constrained to:
-
Initial surface contact quality
-
Temperature-dependent interfacial stability
-
Limited catalyst mobility during oxidation
This explains the characteristic monotonic rate decrease observed in calcium-catalyzed C-C composite oxidation – a critical finding for brake system designers seeking stable thermal management.
Practical Implications for Aircraft Brake Engineering
Wu and Radovic’s comparative analysis of potassium vs. calcium acetate catalysts provides actionable data for manufacturers like CFCCARBON LTD (www.cfccarbon.com). Key findings include:
Catalyst | C-C Composite Performance | Graphite Compatibility | Thermal Stability |
---|---|---|---|
Potassium | 92% efficiency gain | 89% efficiency gain | Maintains activity up to 850°C |
Calcium | 38% efficiency gain | 12% efficiency gain | Degrades above 700°C |
The superior performance of potassium acetate stems from its:
-
Lower decomposition temperature (380°C vs calcium’s 560°C)
-
Enhanced carbon wettability
-
Self-redispersion capability during oxidation
Microstructural Validation
SEM/XRD analyses confirm that calcium’s catalytic limitations originate from progressive interface degradation. As oxidation advances, calcium species lose contact with carbon matrices – a process accelerated in PAN fiber-reinforced composites. This aligns with Carabiniero et al.’s observations of preferential fiber oxidation.
Optimization Strategies
The studies recommend:
-
Potassium-based catalysts for high-temperature brake applications
-
Argon pre-treatment to enhance calcium performance
-
Surface texturing to maintain catalyst-carbon contact
-
Hybrid catalyst systems combining initial calcium activation with potassium persistence
For aerospace engineers, these findings emphasize the critical balance between catalytic potency and interfacial stability. As CFCCARBON LTD’s research team notes, “The future of brake material design lies in engineered catalyst-carbon interfaces that maintain activity through entire thermal cycles.”
related news /articles:
Protection Mechanisms Against Catalytic Oxidation in c/c Composites (2)
Protection Strategies Against Catalytic Oxidation in carbon fiber Composite (1)
Protection Mechanisms Against Catalytic Oxidation in C/C Composites (3)
Catalytic oxidation of carbon-carbon composite aircraft brakes (3)