The use of de-icing chemicals at airport ranways has been shown to produce oxides and carbonates of sodium, potassium and calcium which catalyse the oxidation of carbon-carbon composite aircraft brakes leading to an increase of the oxidation rate by an order of magnitude. This review reports on studies that have characterized the catalytic oxidation and discusses the mechanism of the catalytic reaction based on investigations that were carried out with both C-C composites and carbon as a fossil fuel.
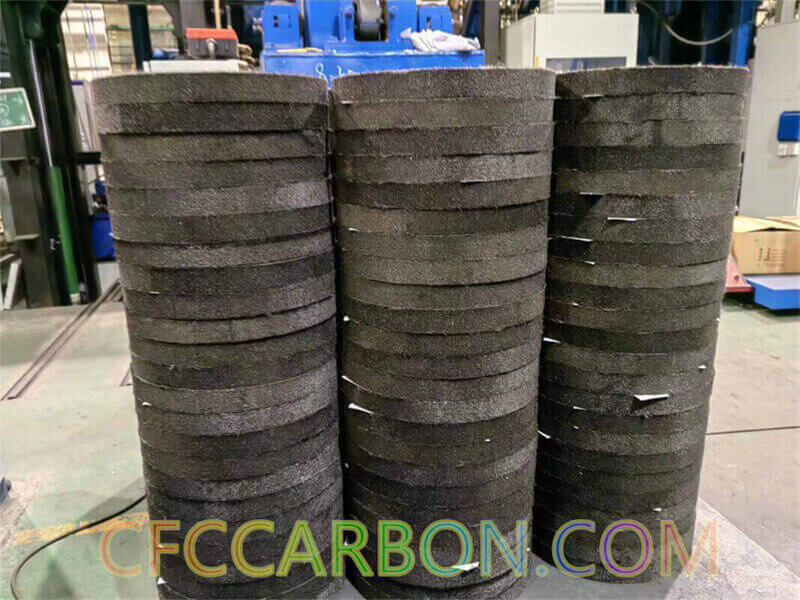
2.5D needle punch CFC airplane Brake disc-carbon fiber composite preform-preforming-Prefab T700 12K (3)
The alkali metal oxides/carbonates are more active catalysts and in their case, the redox reaction between the monoxides and the peroxides has been identified as the most likely catalysis mechanism. In order to reduce or eliminate the problem of catalysis, doping with boron or phosphorus compounds has been investigated by a number of researchers. The effect of these along with the use of protective coatings is also reviewed.
Carbon-carbon composites have found use as friction materials in the aerospace industry and in motorsport and are candidate materials for structural applications at temperatures in excess of 2000C. A typical C-C composite application where friction properties are important is the use of these materials as friction brakes in aircraft. Following their introduction to aircraft in the 1970s, the function of C-C brakes has been to decelerate and stop aircraft after landing by transforming kinetic energy into heat via friction and to dissipate away the resulting heat. In addition, aircraft brakes must be able to efficiently stop an aircraft during an aborted take-off.
The reasons that have led to the use of C-C composites for aircraft braking applications in place of steel brakes include the ability of the former to maintain a stable coefficient of friction and to dissipate heat while maintaining dimensional stability at high temperatures. Other factors including the avsence of fatigue problems and the low density of carbon are also important. By combining the lower density advantage with the higher specific heat capacity of carbon over steel, a 60% weight saving is achieved for a similar brake temperature-operating range.
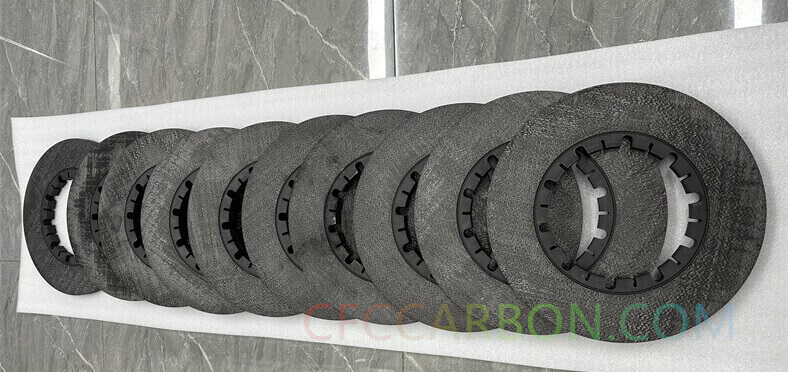
airplane brake disc-aircraft carbon fiber composite material manufacturer- (2)
Compared to steel, C-C discs are more cost-effective and can deliver an average of about 3000 landings, a figure which is about twice as high as that achieved with steel brakes.
In commercial aircraft, the high braking demand requires the sliding interface areas to dissipate approximately 450 kj mm-2 of kinetic energy per unit area to heat in about 30 s. This can lead to high levels of heat generation which has been reported to result in temperature around 1000C and up to 1400C particularly during an aborted take-off. At such high temperatures, the C-C brakes can suffer oxidation and therefore, the lifetime of aircraft brakes is dependent on the rate of oxidation. Thanks for the fast dissipation of heat by the C-C composites and the effective anti-oxidation measures taken by aircraft-brake manufacturers, initially there was little cause for concern. However, the introduction of alkali-based runway de-icing chemicals in the 1990c in place of the traditional urea- and glycol-based de-icers resulted in a drastic increase in the rate of oxidation of carbon-carbon brakes through catalysis of the oxidation reaction.
The aim of this paper is to review the research work that has been conducted to date on the catalytic oxidation of C-C composites in the presence of acetates and/or alkali and alkaline earth metal oxides/carbonates. I addressing the mechanism of catalysis, some relevant studies that were conducted using solely carbon powder for gasification are also reviewed. Finally some of the proposed mechanisms to reduce or eliminate the catalytic –effect are reviewed.
related news /articles:
Catalytic & oxidation of carbon fiber composite aircraft brakes (2)
C/C composite aircraft brakes | brake disc manufacturer in China
Catalytic oxidation of carbon-carbon composite aircraft brakes (5)
Protection Mechanisms Against Catalytic Oxidation in c/c Composites (2)