Liquid Polymer Infiltration: The manufacture of C/SiC components by using polymeric precursors is called liquid polymer infiltration (LPI) process or polymer infiltration and pyrolysis (PIP) process and represents one of the most advanced manufacturing methods for large and complex shaped CMC parts for the aerospace industry. The starting materials to form the silicon carbide matrix are usually polycarbosilane or polysilane polymers which convert from polymer to an amorphous or crystalline ceramic during pyrolysis. The big difference in the densities of the polymeric and the SiC matrix results in a reduction of volume and induces a high amount of pores in the matrix. Inert submicronic SiC particles or reactive fillers can be used to reduce the shrinkage, but usually a number of successive infiltration cycles followed by a respective pyrolysis step are required to obtain a SiC matrix with a sufficient high density. Typically, five to seven impregnations are necessary to obtain a residual porosity of less than 10%.
Fig.11 give an overview of the LPI-process which is used for the manufacture of integral C/SiC components. Prior to their slurry
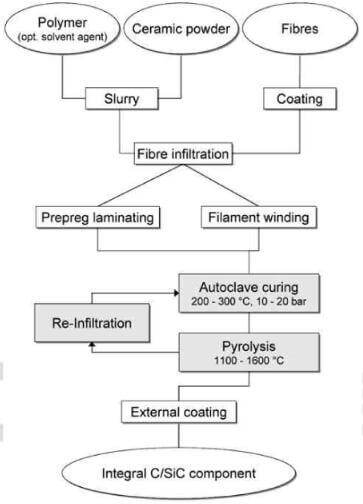
Fig.11-the technique for making CSiC components by liquid polymer infiltration
infiltration the carbon fibres are coated by CVD to reduce the fibre/matrix bonding. In the follwing steps, the processing route follows the classical methods of manufacturing carbon fibre reinforced plastics. The coated fibres are infiltrated with the precursor, for example by filament winding, fabric prepreging or resin transfer moulding. The resulting laminate is subsequently cured in an autoclave at 200-300°C.
During the following high temperature treatment under inert atmosphere or vacuum the polymer is decomposed and the real ceramic matrix is formed within several intermediate steps. The chosen temperature-time-cycle influences heavily the morphology of the resulting SIC matrix. Whilst high heating rates and low final temperatures lead to a high porosity and an amorphous matrix, a crystalline SiC matrix with low and fine distributed pores can be obtained by low heating rates and ultimate temperatures up to 1600°C.
To summarize, this polymer route of making C/SiC composites has the advantage of a good matrix composition control, relatively low densification temperatures and the possibility to join together different parts with the original matrix slurry to highly complex components. The disadvantages are the multiple infiltration/densification/pyrolysis cycles and the large shrinkage during pyrolysis, resulting in a cracking of the matrix.
Liquid Silicon Infiltration: This technique is based on the impregnation of porous carbon/carbon composites by molten silicon and reaction of the metallic melt with the solid matrix carbon to silicon carbide. The melt infiltration process can use almost any reinforced geometry and yields a high-density, low-porous matrix. A fibre preform having a network of pores and cracks is infiltrated by liquid silicon, mostly using capillary pressure. Application of pressure of processing in vacuum can support the infiltration process. The tmperatres involved are at least beyond the melting point of silicon and can lead to deleterious reactions between the fibres and silicon. The melt viscosity, the chemical reactivity, the wetting of the reinforcement and the anomaly of silicon during phase transition are critical processing parameters to be considered. The thermal expansion mismatch between the fibres and the matrix and the rather large temperature interval between the processing temperature and room temperature are problems which have to be taken into account.
First attempts to infirltrate carbon/carbon composites by liquid silicon have been conducted for more than twenty years. After these basic investigations, the carbon fibres have to be coated priors to the infiltration of silicon in order to reduce the degree of fibre degradation. Also, highly graphitized carbon fibers like high modulus fibres are recommended as reinforcement for the fibre preform which are more stable in contact with silicon than only carobnized fibres. Both requirements are in contrast with a cost-efficient processing of CMCs and only poor fracture toughness have been achieved by the infiltration of unadapted carbon/carbon preforms. In the last few years, new processes and novel C/C-composites with adapted microstructures which also allow the use of uncoated and chopped high tenacity carbon fibres were developed.
Related news /knowledge:
- Carbon fiber reinforced silicon carbide composites (C/SiC, C/C-SiC)-(1)
- Carbon fiber reinforced silicon carbide composites (C/SiC, C/C-SiC)-(3)-application
- Carbon fiber reinforced silicon carbide composites (C/SiC, C/C-SiC)-(4)-application
- Carbon fiber reinforced silicon carbide composites (C/SiC, C/C-SiC)-(6)-processing