In principal, there exist numerous processing routes to infiltrate the matrix system into the fiber preform. Conventional powder processing techniques used for making monolithic ceramics are mostly not suitable and rather unconventional techniques to avoid damage of the fiber preforms are applied. They can be distinguished between the impregnation either by gas phase or by liquid phase
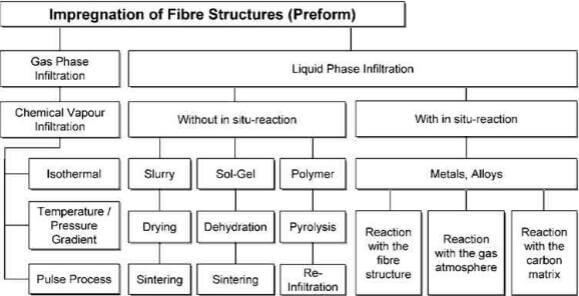
Fig.9-general overview of the manufacturing processes for CMC materials
infiltration (Fig.9). Three different techniques are currently used in an industrial scale for the production of C/SiC and C/C-SiC composites, each of them leading to specific microstructures and properties (Fig.10):
—- Chemical Vapor Infiltration (CVI)
—- Liquid Polymer Infiltration (LPI) or Polymer Infiltration Pyrolysis (PIP)
—- Liquid Silicon Infiltration (LSI)
Historically, the processing routes moved from the isothermal CVI process to more cost-effective technique such as gradient-CVI and liquid polymer or liquid silicon infiltration. These routes are faster and lead to shorter manufacture cycles than isothermal CVI and, especially the two liquid phase processes LPI and LSI, use technologies already developed for polymer matrix composites (PMC).
One important aspect is to realize that processing should be considered as an integral part of the whole process of designing a CMC
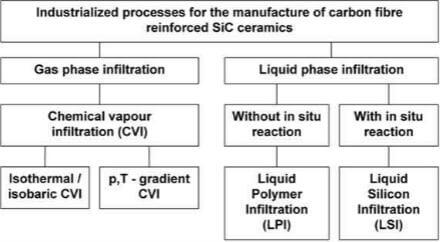
Fig.10-processes for the industrial manufacture of CSiC and CC-SiC composites
component. Fiber orientation, dimensionality of the preform and thermal treatment conditions are important parameters of influence for the preformance of the final CMC product.
Chemical Vapour Infiltration: Chemical vapour infiltration in general allows the deposit of quite a variety of matrices and the processing of any complex shape. The multi-directional fibre preform is fixed in the furnace with a tooling or build-up with a temporary binding agent, which is removed in a first pyrolysis step. The ceramic matrix is obtained by the decomposition of gaseous species within the open porosity of the preform. Usually, methyltrichlorosilane as the process gas and hydrogen as the catalyst are used to form the SiC matrix. Two different phenomena control the matrix rate within the preform’s pores:
– the kinetics of the chemical reaction
– the mass transport of the reaction products into the porosity.
The quality and purity of the deposed silicon carbide is determined by the ratio of mixture between hydrogen and MTS. High portions of H2 lead to Si-rich matrices, whilst increasing amounts of MTS result in SiC matrices with residual carbon. In order to get a good in-depth deposition, low pressures and low temperatures are necessary and must be kept constant over the whole process. This isothermal/siobaric CVI-process leads to very good termalmechanical properties and high fracture toughness. The drawbacks lie in long processing times lasting several weeks or months and inrestricted preform depths which can be infiltrated in one step.
To overcome thoese geometrical restrictions and to increase the deposit rate of SiC, thermal and pressure gradient-CVI processes have been developed and industrialized.
In contrast to the isothermal CVI process a forced mass flow of MTS, driven by gradients of temperature and pressure within the preform, is applied and allows considerable higher process temperatures and pressures. The higher gas density and higher reaction speed result in manufacture times which are more than one order of magnitude faster than the isothermal/isobaric CVI. Typically, 40 to 60 hours are necessary to infiltrate carbon preforms of 5mm thickness to a residual open porosity of 12%. As the forced mass flow of gases necessitate the sealing and cooling of the fiber preform, this variant on CVI is focussed on simple and standardized geometries like profile, tubes and plates.
Besides the good quality of the C/SiC composites processed by chemical vapour infiltration, one of the major advantages of this manufacturing route is that is allows the control of the fibre/matrix interphase. Therefore, C/SiC composites are shortly deposited in a first step with carbon to bovern the fiber/matrix bonding forces. In summary, the manufacture of C/SiC components via the gradient-CVI process comprises the following steps:
1. Fiber preform build-up with a polymer binding agent.
2. Pyrolysis of the polymer (leads to a self-supporting fibre preform)
3. Deposition of carbon for fibre coating (interphase formation)
4. Deposition of SiC for matrix infiltration.
5. Final machining of the near-net shaped C/SiC component.
To continue…
Related news /knowledge:
- Carbon fiber reinforced silicon carbide composites (C/SiC, C/C-SiC)-(1)
- Carbon fiber reinforced silicon carbide composites (C/SiC, C/C-SiC)-(4)-application
- Carbon fiber reinforced silicon carbide composites (C/SiC, C/C-SiC)-(5)-application
- Carbon fiber reinforced silicon carbide composites (C/SiC, C/C-SiC)-(7)-processing