The microstructure of a typical C-C brake is presented in Fig..1 which shows the presence of carbon fibers embedded within a carbon matrix. The manufacture of carbon fibers has been reported extensively in the past articles; carbon fibers can be made from different precursors including pitch, rayon and pan. In the case of C-C brakes, PAN fibers are needled together in three directions or 2.5D to form a cloth which then undergoes
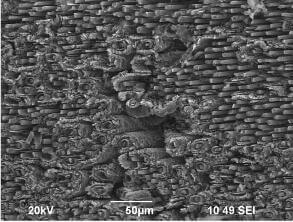
SEM micrograph of partially oxidised C-C composite showing carbon fibers in a matrix of carbon
carbonization in an inert atmosphere. The carbonized cloth is then cut to a specific mould and several layers are laid on top of each other to form a carbon pre-form disc with a specified weight for production for a specific type aircraft. Several discs are compressed onto a jig and loaded into a predetermined position in a furnace which is heated inductively to about 1000C. Natural gas is then introduced which infiltrates the disc preforms and deposits carbon in the gaps between the carbon fibers.
The discs go through multiple infiltration cycles until the target density which generally ranges between 1.75-1.85g/cm3 is achieved. These values correspond to porosity levels between 10 and 15%, though manufacturers ten to specify density rather than porosity values. The discs are finally machined to the desired size using computer-controlled equipment. Disc dimensions tend to vary, but are typically of diameter of 400mm and 25mm thickness
The use of de-icing chemicals has become essential in order to maintain safe-operating conditions both in-flight and at airport runways. The formation of ice on the aerodynamic surface of an aeroplane can affect in-flight
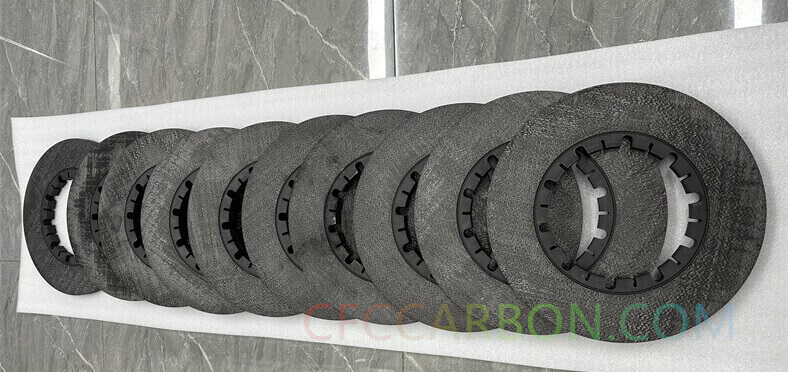
airplane brake disc-aircraft carbon fiber composite material manufacturer- (2)
handling, while icy runways are hazardous to aircraft as ice reduces the friction coefficient significantly and the aircraft tyres cannot grip the runway surface. Anti-icing fluids are therefore sprayed directly onto aircraft to prevent ice formation, while de-icing chemicals are used to remove ice from runways.
Traditionally these products were made from glycol and urea; while glycol products are still being used for aircraft de-icing, the runway de-icing fluids were substituted by alkali metal formats and acetates during the 1990s owing to the high aquatic toxicity and high values of both biochemical oxygen demand and chemical oxygen demand of urea. The COD value for urea de-icer has been reported to be 2.1kg O2/kg compared to 0.7 and 0.3 kg O2/kg of de-icer for sodium and potassium acetates respectively. While the introduction of the new de-icers led to improvements to the operational and environmental quality of winter maintenance activities at airports, several reports began to emerge highlighting some unexpected detrimental effects that included the catalytic oxidation of C-C brakes, cadmium coating corrosion, corrosion of airfield electrical and ground support equipment as well as degradation of asphalt and concrete.
Concerns arising from such observations led to the establishment of the Airport Cooperative Research Programme (ACRP) which collected and reviewed data on the damage caused by the new de-icers. According to the findings of the programme as summarized by Friedman et al., analysis of C-C brakes that were returned for service in the winter months indicated that brakes from aircraft operating in northern Europe has suffered more oxidation compared to those used in aircraft around the Mediterranean area. In addition, the brakes that came from aircraft operating in northern Europe displayed greater contamination from potassium as a result of the more extensive use of de-icing chemicals. Effectively, the catalytic oxidation of C-C brakes was the culprit.
It was also reported that even cooler parts of the brakes were suffering from catalytic oxidation. At the temperature level that develop as a result of friction, the sodium, potassium and calcium acetates and formats from the de-icers decompose to the equivalent carbonates or oxides which are well-known for their catalytic effects on carbon-based reactions.
related news /articles:
C/C composite aircraft brakes | brake disc manufacturer in China
Catalytic & oxidation of carbon fiber composite aircraft brakes (2)
Catalytic oxidation of carbon-carbon composite aircraft brakes (5)
Protection Mechanisms Against Catalytic Oxidation in c/c Composites (2)