Exploring the Fundamentals and Innovations in Uncoated Carbon-Carbon Composites
By CFC Carbon Co., Ltd | Updated: May 18, 2025
1. What Are Carbon-Carbon Composites?
Carbon-carbon (C/C) composites are advanced materials composed of carbon fiber reinforcements embedded in a carbon matrix. These
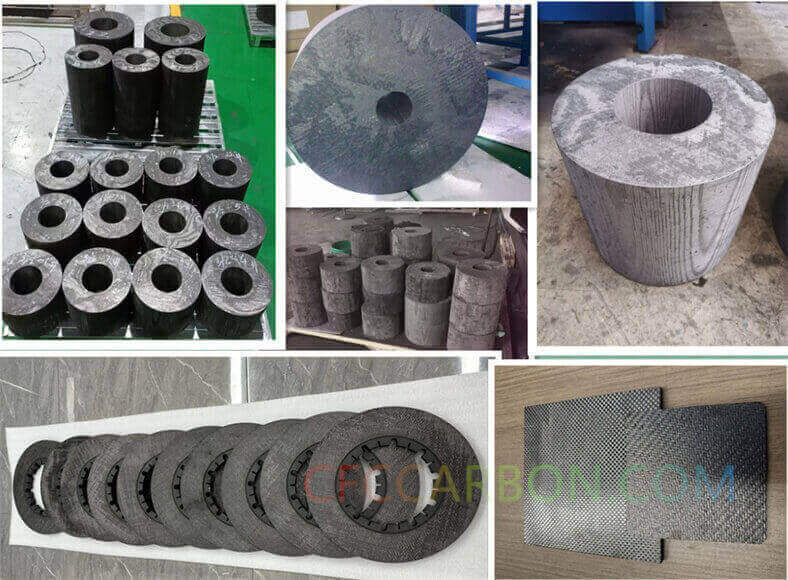
3D 4D carbon fiber composite material manufacturer factory -airplane brake disc plates sheets U L profiles-2D(s)
composites exhibit exceptional thermal stability, high strength-to-weight ratios, and resistance to extreme environments, making them indispensable in aerospace, defense, and biomedical applications. According to CFC Carbon’s research, uncoated C/C composites are particularly valued for their purity and adaptability in high-temperature processes, such as chemical vapor deposition (CVD).
2. Production, Classification, and Performance
Manufacturing Techniques
C/C composites are primarily fabricated through two methods:
-
Chemical Vapor Infiltration (CVI): Methane gas is decomposed at high temperatures to deposit pyrolytic carbon, filling pores and densifying the structure. This process creates columnar carbon nodules (up to 20 μm thick) and addresses porosity issues.
-
Liquid Impregnation Pyrolysis (LIP): Thermosetting resins or pitches are repeatedly impregnated and carbonized to enhance density.
Recent advancements include 3D printing with multiphase direct ink writing (MDIW), which enables scalable production of multilayered architectures with tailored thermal and mechanical properties.
Material Classification
-
2D/2.5D Composites: Feature layered fiber fabrics with limited out-of-plane reinforcement. These structures often develop 25 μm pores at fiber intersections and fissure cracks (5–50 μm) due to thermal expansion mismatches.
-
3D Braided Composites: Utilize multidirectional fiber preforms to minimize cracking. For example, 3D-C/C composites for chest wall reconstruction show 51% open porosity (>100 μm) for tissue adhesion and 167 MPa tensile strength, outperforming traditional titanium alloys.
Key Applications
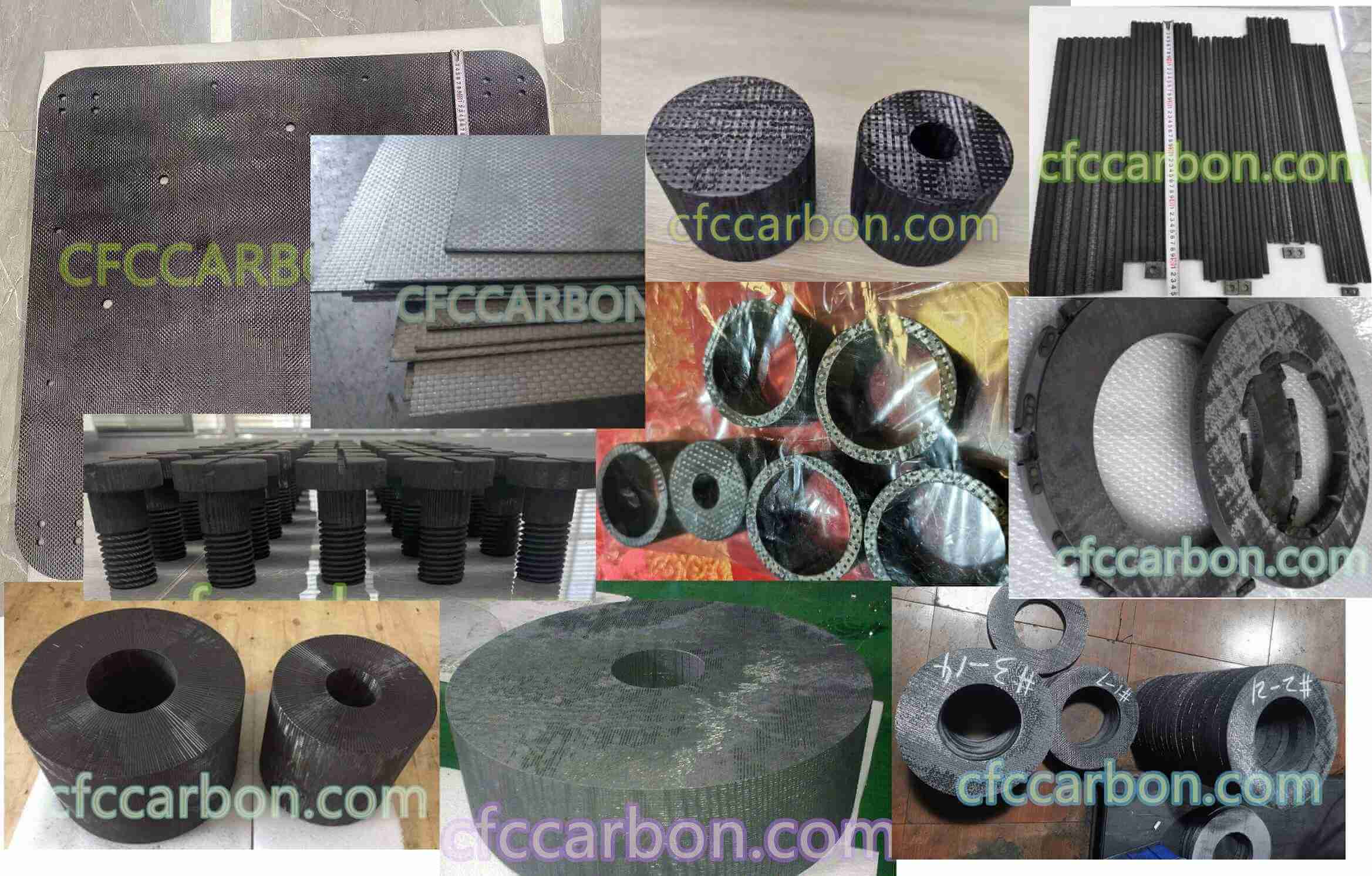
carbon fiber composite material manufacturer in China(1)
-
Aerospace: Rocket nozzles, heat shields, and brake systems.
-
Biomedical: Artificial ribs and bone scaffolds due to biocompatibility and modulus (5 GPa) matching human bone.
-
Energy: High-conductivity components for solar thermal systems.
Performance Characteristics
-
Thermal Stability: Low coefficient of thermal expansion (CTE) and tolerance to >2000°C environments.
-
Mechanical Integrity: Tensile strength up to 167 MPa with fatigue resistance over 1 million cycles.
-
Microstructural Challenges: Inherent cracks (50–100 μm in CVD layers) and anisotropic thermal behavior arise from heterogeneous carbon phases (e.g., pyrolytic carbon vs. fiber carbon).
3. Microstructural Analysis of Uncoated C/C Composites
Recent studies by CFC Carbon reveal critical microstructural features in uncoated C/C composites:
-
Crack Networks: Surface CVD layers exhibit 50–100 μm cracks, while planar sections show finer fissures (5–50 μm). These result from CTE mismatches among four carbon types: fiber carbon, resin-derived carbon, pitch carbon, and CVD carbon.
-
Porosity Distribution: A 25 μm pore concentration occurs at fiber intersections, with finer porosity networks in fiber-matrix interstices. CVD carbon effectively fills pores within 100 μm depths.
-
Inhibitor Effects: Boron carbide (B4C) inhibitors improve oxidation resistance with uniform particle distribution, whereas elemental boron forms uneven aggregates.
4. Innovations and Future Directions
To address manufacturing limitations, researchers are integrating functional additives like silicon carbide (SiC) and graphite nanopowder (Gnp) into resin matrices. 3D-printed C/C composites now demonstrate dual-phase patterning for enhanced thermo-electrical properties. Additionally, oxidation-resistant coatings (e.g., multilayer SiC/ZrO2) are being developed to expand applications in corrosive environments.
5. Conclusion
Uncoated carbon-carbon composites remain a cornerstone of high-performance engineering. By optimizing fabrication techniques and microstructure design, these materials are poised to revolutionize industries from aerospace to regenerative medicine. For detailed product specifications, visit CFC Carbon’s official website.
About CFC Carbon Co., Ltd
As a leader in carbon material innovation, CFC Carbon specializes in customized C/C solutions for extreme environments. Our R&D team leverages advanced characterization tools, including SEM and micro-CT, to ensure material reliability. Contact us at potter@cfccarbon.com for collaboration opportunities.
related news /articles:
Friction performance of C/SiC brakes in different environment (9)
Structural Geometry of CC composite 2D fabrics (2)—Knitted fabrics and Braided fabrics
Initial characterization of coated carbon-carbon composites
Oxidation kinetics and mechanisms of a 2D C/C composite (1)