Title: Carbon-Carbon (C/C) vs. Silicon Carbide (C/SiC): A Comprehensive Guide to Ablation Resistance and Material Selection
Understanding Ablation Rates and High-Temperature Material Performance
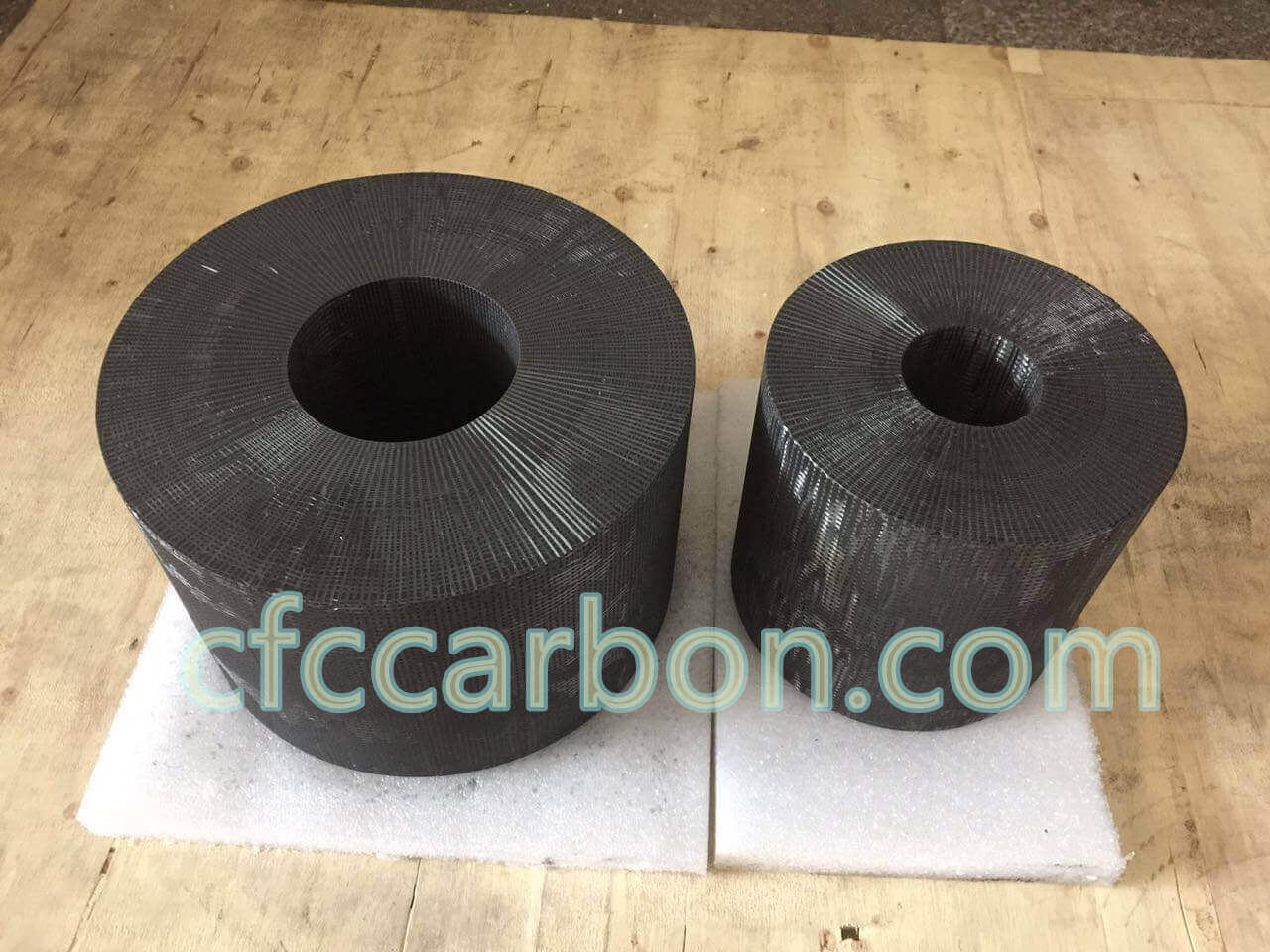
3D 4D 5D Hoops, Loop, weaving, stucture, drawing, carbon fiber, carbon, composite, CFC, CC, manufacturer, China, (1)
In extreme environments such as aerospace, hypersonic vehicles, and re-entry systems, selecting the right ablation-resistant material is critical. Two leading candidates—carbon-carbon (C/C) and carbon-silicon carbide (C/SiC)—offer distinct advantages depending on temperature ranges and operational conditions. Below, we break down their ablation behaviors, structural properties, and optimal use cases.
1. What is Ablation Rate?
Ablation rate measures how quickly a material erodes under extreme heat and chemical reactions (e.g., oxidation). It is quantified by linear ablation rate (mm/s) and weight ablation rate (mg/s), critical metrics for evaluating thermal protection systems (TPS).
2. C/SiC vs. C/C: Key Differences in Ablation Resistance
Low to Moderate Temperatures (≤1600°C)
-
3D-xyz structure-carbon fiber composite material-CC-CFC
C/SiC Composites: Excel due to superior oxidation resistance. At 1600°C, their linear ablation rate (e.g., 0.068 mm/s for PIP-type) is lower than C/C.
-
C/C Materials: Begin oxidizing above 400°C but remain stable up to 1600°C with minimal mass loss.
Ultra-High Temperatures (2000°C+)
-
C/SiC Limitations: Above 2000°C, SiC decomposes into volatile SiO gas, causing severe non-uniform ablation and surface peeling (e.g., 0.012–0.023 mm/s at 2300°C).
-
C/C Superiority: Carbon fibers and matrix erode uniformly without catastrophic failure. Even at 3200°C, C/C maintains structural integrity in inert/vacuum environments.
3. C/SiC Subtypes: PIP vs. LSI Manufacturing
Two primary methods produce C/SiC composites:
-
-
LSI (Liquid Silicon Infiltration):
Reacts silicon with carbon to form SiC.
Lower SiC content (~50–70%), uneven distribution, and fiber damage reduce strength.
-
PIP (Polymer Infiltration and Pyrolysis):
Achieves higher SiC content (80%+) with uniform crystallinity.
-
Superior ablation resistance below 2300°C but underperforms LSI at extreme temperatures.
Ablation Test Data (2300°C):
Type | Density (g/cm³) | Linear Rate (mm/s) | Weight Rate (mg/s) |
---|---|---|---|
PIP | 1.90–1.95 | 0.066–0.068 | 2.48–3.23 |
LSI | 2.10–2.30 | 0.012–0.023 | 0.34–1.68 |
Conclusion: LSI outperforms PIP at ≥2300°C due to denser structure and lower porosity.
4. Temperature Limits in Different Environments
Environment | C/SiC Stability | C/C Stability |
---|---|---|
Air | ≤400°C (no oxidation) | ≤1600°C (gradual oxidation) |
Inert Gas | ≤2700°C (SiC gasifies) | ≤3200°C (intact fibers) |
Vacuum | ≤2700°C (rapid gasification) | ≤3200°C (uniform ablation) |
5. Why C/C is the Ultimate Ablation-Resistant Material
C/C composites dominate in ultra-high-temperature applications (>2000°C) for three reasons:
-
Uniform Structure: Isotropic carbon fiber reinforcement ensures even stress distribution.
-
Predictable Erosion: No delamination or sudden failure—critical for re-entry vehicles.
-
Adaptability: Performs reliably in air, vacuum, and inert atmospheres.
6. CFCCARBON CO., LTD: Pioneering Advanced Ablation Solutions
For industries demanding unmatched thermal protection, CFCCARBON CO., LTD (www.cfccarbon.com) leads the market with cutting-edge C/C and C/SiC composites. Their expertise includes:
-
Tailored C/C Components: Optimized for rocket nozzles, brake systems, and nuclear reactors.
-
High-Precision C/SiC: Engineered via LSI/PIP for turbine blades and hypersonic TPS.
-
R&D Excellence: Custom solutions for temperatures up to 3200°C.
Why Choose CFCCARBON?
-
ISO-certified manufacturing with ultra-low porosity (<5%).
-
Global clientele in aerospace, energy, and defense.
-
Technical support for material selection and lifecycle management.
Visit www.cfccarbon.com to explore case studies and product specifications.
Final Recommendations
-
C/SiC: Ideal for thermal insulation below 2000°C (e.g., engine liners).
-
C/C: The gold standard for ablation-critical applications above 2000°C (e.g., rocket thrust chambers).
You can check the C/C vs C/SiC ablation resistant comparison sheet attached, or download it: https://www.cfccarbon.com/wp-content/uploads/2025/04/CFCvsC-SiCLSI-PIP-ablationmaterial-CFCCARBON-2025.pdf
For material specifications or partnership inquiries, contact CFCCARBON’s engineering team today.
related news /articles:
Carbon fiber reinforced silicon carbide composites (C/SiC, C/C-SiC)-(6)-processing
Carbon Felt and C/SiC Material Manufacturer: Leading the Way in Advanced Composite Solutions
Carbon fiber reinforced silicon carbide composites (C/SiC, C/C-SiC)-(1)