Revolutionizing Extreme Environments: Ultrahigh-Temperature Coatings for Carbon-Carbon Composites
By CFC Carbon Co., Ltd | May 17, 2025
1. What Are Carbon-Carbon Composites?
Carbon-carbon (C/C) composites are advanced materials composed of carbon fibers embedded in a carbon matrix. Renowned for their
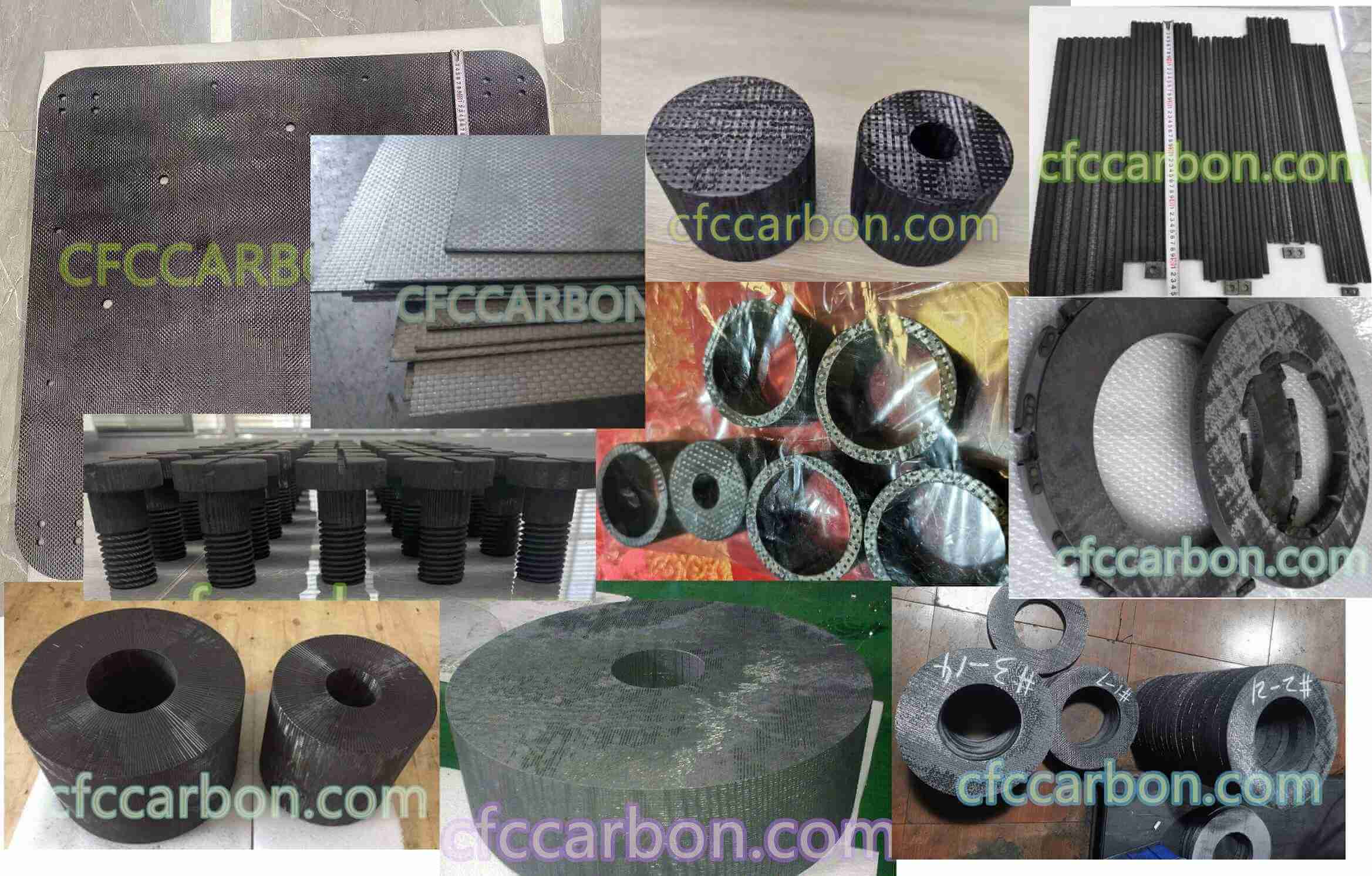
carbon fiber composite material manufacturer in China(1)
exceptional properties, they exhibit ultra-low density (1.3–1.95 g/cm³), high thermal stability (retaining strength up to 2500°C), and outstanding resistance to thermal shock and corrosion812. These composites are indispensable in aerospace (e.g., rocket nozzles, hypersonic vehicle leading edges), automotive braking systems, and nuclear reactors.
2. The Critical Role of Ultrahigh-Temperature Coatings
While C/C composites excel in inert environments, their Achilles’ heel lies in oxidative degradation above 500°C. Ultrahigh-temperature coatings (UHTCs) address this by forming protective barriers against oxygen and erosive gases at extreme temperatures (1600–2400°C).
Key Challenges in Coating Design
-
Oxygen Permeability: Effective coatings must achieve oxygen permeability below 10⁻¹⁰ g/cm·s to ensure long-term protection.
-
Thermal Expansion Mismatch: Coatings like ZrO₂ or HfO₂ suffer from high oxygen permeability and coefficient of thermal expansion (CTE) mismatch with C/C substrates, leading to delamination.
-
Material Stability: At ultrahigh temperatures, oxides react with carbon to form carbides, undermining coating integrity.
SiC coating carbon fiber composite material-CC-CFC (2)
3. Cutting-Edge Coating Technologies
Iridium-Based Coatings
Iridium has long been explored for its unmatched properties: a melting point of 2400°C, negligible oxygen permeability, and chemical inertness with carbon. Techniques like chemical vapor deposition (CVD) and plasma spraying have been used to apply iridium layers, demonstrating short-term protection up to 2100°C. However, challenges like high material costs, volatile oxide formation, and CTE mismatch limit its widespread adoption10.
Silica (SiO₂) Glass Sealants
SiO₂ coatings offer unique advantages: low CTE, self-healing via viscous flow at 1800°C, and compatibility with C/C substrates. However, SiO₂ reacts with carbon at high temperatures, necessitating intermediate layers (e.g., ZrB₂ or HfTiO₄) to prevent degradation. Recent advances include multilayer designs combining SiO₂ with refractory oxides to enhance erosion resistance.
Multiphase Ceramic Coatings
To overcome single-phase limitations, composite coatings like ZrB₂-ZrC-SiC are gaining traction. Laser cladding and precursor infiltration pyrolysis (PIP) enable precise deposition of these materials, which form stable oxides (e.g., ZrO₂, SiO₂) during ablation. For instance, ZrB₂-SiC coatings reduce mass ablation rates by 75% compared to uncoated C/C composites.
4. Manufacturing Innovations
Laser Cladding
Laser cladding has emerged as a game-changer for depositing millimeter-thick UHTC layers. By fusing Zr, B₄C, and Si powders onto C/C substrates, this technique creates dense, crack-free coatings with metallurgical bonding. For example, ZrB₂-ZrC-SiC coatings withstand 1600°C oxidation for 80 minutes with minimal weight loss.
Chemical Vapor Infiltration (CVI)
CVI densifies C/C preforms with ceramic matrices like SiC or HfC, enhancing both mechanical strength and oxidation resistance. High-density C/C composites (up to 1.95 g/cm³) produced via CVI are now commercially available, offering tensile strengths exceeding 165 MPa.
5. Applications Across Industries
-
Aerospace: Leading edges of space shuttles and hypersonic vehicles rely on reinforced carbon-carbon (RCC) panels with SiC or HfC coatings89.
-
Automotive: Formula 1 and luxury cars (e.g., Bugatti Veyron) use C/C-SiC brake discs for unmatched thermal stability.
-
Energy: Nuclear reactors employ C/C-UHTC components for plasma-facing applications.
6. CFC Carbon’s Technological Leadership
At CFC Carbon Co., Ltd, we pioneer high-density C/C composites (1.95 g/cm³) and advanced coatings tailored for extreme environments. Our 4D woven composites deliver:
-
Thermal Conductivity: 49 W/m·K (in-plane) at 900°C
-
Mechanical Strength: Compressive strength up to 273 MPa
-
Custom Solutions: Laser-clad ZrB₂-ZrC-SiC coatings for ablation resistance.
Explore our full product portfolio at www.cfccarbon.com.
7. Future Directions
Research is pivoting toward high-entropy UHTCs (e.g., (Hf,Zr,Ta)C) and nanoscale fiber coatings to further enhance durability. With innovations in additive manufacturing and AI-driven material design, the next generation of C/C composites will push the boundaries of extreme-environment engineering.
Contact Us
CFC Carbon Co., Ltd
Yizhuang Economic Development Zone, Beijing 100176, China
Email: potter@cfccarbon.com | Tel: +86-18910941489
Website: www.cfccarbon.com
related news /articles:
Advanced Protective Coatings for Carbon-Carbon Composites
Introduction of high-temperature coatings on CC composite material
Innovations in Carbon-Carbon Composite Internal Coatings
Advanced Coatings for Carbon fiber Carbon Composites