Thick-wall multidirectional CC composite structures include nose tips for atmospheric reentry vehicles and components of solid propellant rocket engines. Weave architectures for the former are, for the most part, orthogonal 3D constructions with fine yarn spacings. A typical 3D construction is illustrated in figure 6. In addition
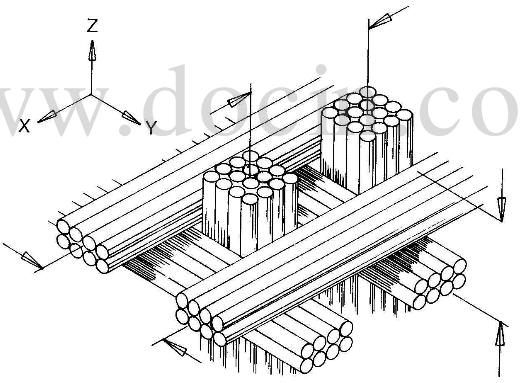
typical 3D CC composite structure
to the high-temperature mechanical property retention afforded by CC composites, reentry vehicle nose tips are required to exhibit unparalleled resistance to thermal shock, predictable thermochemical ablation performance, and the capacity to survive erosive conditions presented to high-velocity vehicles by ice, snow, rain, and dust. Atmospheric reentry environments and their impacts on CC design have been studied extensively over the years. For optimum mechanical properties, higher fiber volume fraction is desired. Small center-to-center fiber spacings are preferred for smooth erosion/ablation performance. Low matrix porosity is also desired for resistance to both thermochemical ablation and particle erosion.
Carbon-carbon reentry applications other than nose tips may have other performance requirements. Control
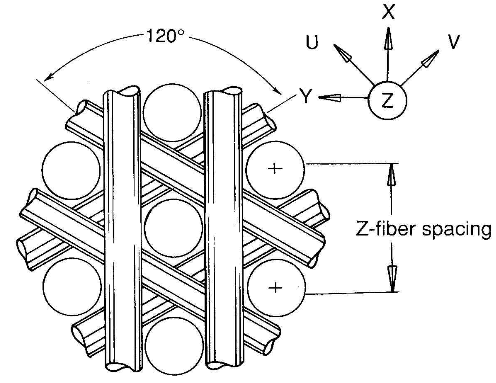
schematic of 4D CC composite structure
surface components requiring higher in-plane shear moduli may require a 4D architecture, such as shown in figure 8, or a 5D architecture, as shown in figure 9. In both
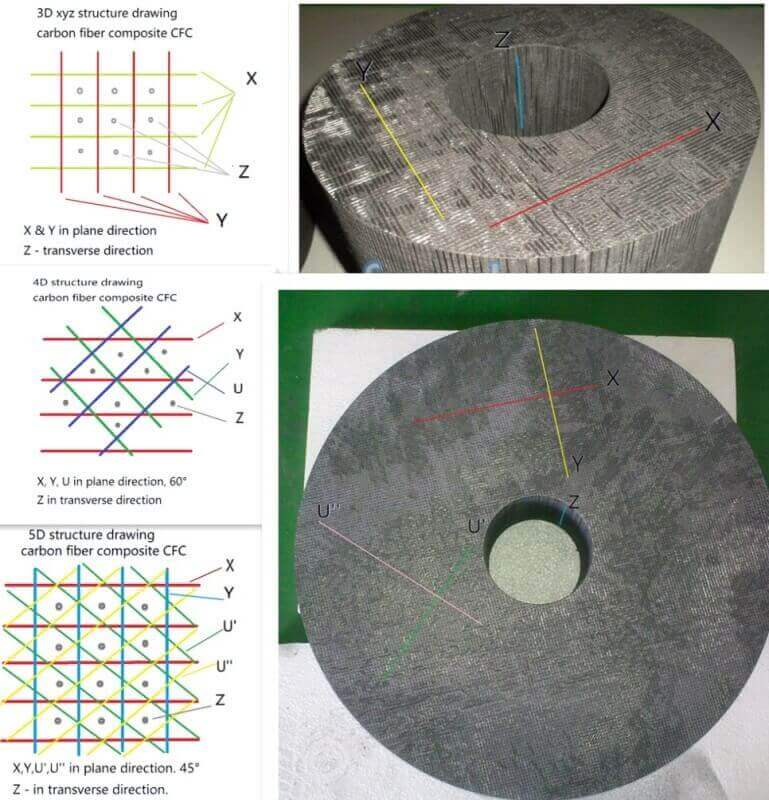
3D 4D 5D carbon fiber composite CFC structural diagram drawing material (1)
cases the additional in-plane fibers impart higher X-Y shear moduli and overall greater isotropy than can be realized from an orthogonal 3D architecture. The result of these fiber architectures is a lower fiber volume fraction in each in-plane direction of reinforcement with a resultant loss of tensile and compressive properties in those directions.
Where off-axis properties are of primary importance and on-axis property requirements can be sacrificed, a 4D architecture of the type shown in figure 8 may be appropriate. A seven-directional CC composite has been manufactured, and 11D CC constructions are feasible. In general, an increase in the number of directions of reinforcement serves to enhance off-axis properties at the expense of on-axis properties, rendering the CC
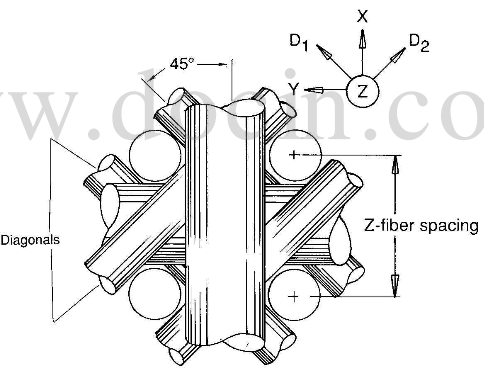
schematic of 5D CC composite structure
composite more isotropic in its properties and lowering the maximum possible fiber volume fraction, hence, the preceding conditions influence the directional properties in any one direction.
For thick-walled constructions that are cylindrical or conical in shape, a polar 3D architecture, shown in figure 11, is appropriate. A fully densified cylindrical ring having this fiber architecture is shown in figure 12. The Z-direction fibers of a polar preform provide axial tensile and axial compressive strength; the circumferential fibers provide hoop tensile strength; the redial fibers impart radial compressive strength and torsional shear strength to the construction.
While weaving of dry carbon yarns is one method of constructing 3D cylindrical preforms, it is not the only method that has been used. An alternative approach uses prefabricated rods that form the radial array and automatic winding of the axial and hoop directions using dry carbon yarn. The cylindrical preform is then processed to yield a CC structure.
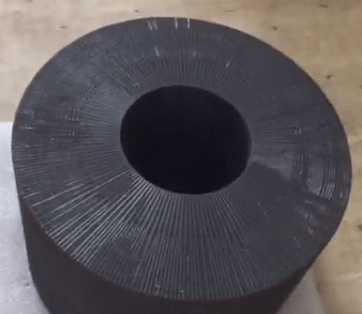
3D cylindrical CC composite round
Orthogonal 3D constructions may also be fabricated by a method other than weaving continuous yarns through the length, width, and height of the preform. This method stacks layers of woven fabric according to a desired 2D orientation sequence and pierces the layers of fabric by locating graphite yarns that provide the Z-direction reinforcement. This technique permits higher in-plane fiber volume fractions than can be realized with 3D orthogonal weaving. A drawback of this technique is that in-plane fibers are broken during the placement of the Z-yarn bundles. The 3D CC composite whose properties was constructed by this method.
Contact Us
related news /articles:
Different structures of 3D carbon carbon composite | C/C composite
4D Carbon fiber composite | CFC material manufacturer in China
2D stucture C/C Composite plates manufacturer in China
3D 4D 5D carbon fiber composites structure and material manufacturer