Introduction to Carbon-Carbon Composite Coatings
Carbon-carbon composite coatings (C/C coatings) are advanced materials combining carbon fibers embedded in a carbon matrix, offering exceptional thermal stability, mechanical strength, and resistance to extreme environments. These coatings are critical for applications requiring lightweight durability, such as aerospace components, high-performance automotive systems, and medical implants. Unlike
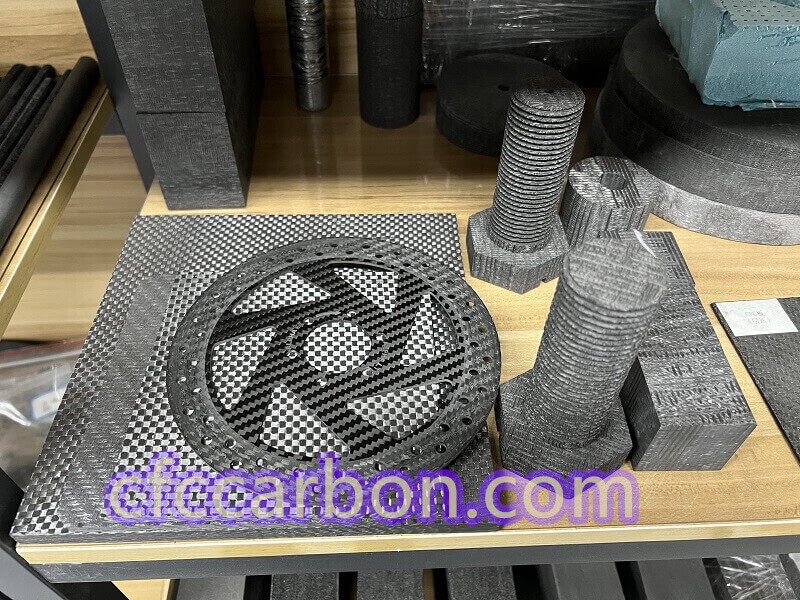
carbon fiber composite CFC parts
traditional materials, C/C coatings maintain structural integrity at temperatures exceeding 2000°C, making them indispensable for re-entry vehicles, rocket nozzles, and braking systems.
Manufacturing and Classification
-
Production Techniques
-
Chemical Vapor Infiltration (CVI): A dominant method for creating dense, high-purity coatings by depositing carbon from hydrocarbon gases onto preforms.
-
Liquid Impregnation Pyrolysis (LIP): Involves repeated cycles of resin/pitch infiltration and carbonization to enhance density and reduce porosity.
-
Thermal Spraying: Cost-effective for large components, though limited to materials with congruent melting points.
-
-
Classification by Structure
-
2D/2.5D Coatings: Layered fiber architectures ideal for moderate-stress applications like aircraft brakes.
carbon fiber composite material manufacturer in China(1)
-
3D Braided Coatings: Enhanced impact resistance and open porosity for biomedical uses, such as chest wall reconstruction implants.
-
Performance Characteristics
-
High-Temperature Stability: Retains strength above 2000°C, with thermal conductivity tailored for heat shields and nozzles.
-
Low Thermal Expansion (CTE): CTE values as low as 1.8×10⁻⁶°C⁻¹ minimize thermal stress in aerospace structures.
-
Tribological Resistance: Superior wear properties under friction, critical for automotive braking systems.
-
Biocompatibility: 3D-C/C composites show promise in medical implants due to bone-like stiffness (5 GPa) and minimal immune response.
Applications Across Industries
-
Aerospace & Defense
-
Reinforced Carbon-Carbon (RCC): Used in Space Shuttle leading edges and rocket nozzles for thermal protection.
-
Self-Healing Coatings: Boron-modified SiC layers seal cracks during re-entry, extending component lifespan.
-
-
Automotive
-
Brake Discs: Carbon-carbon brakes reduce weight by 40% compared to steel, improving fuel efficiency in Formula 1 and luxury vehicles.
-
-
Medical
-
Artificial Ribs: 3D-C/C composites with 51% open porosity promote tissue adhesion, outperforming titanium alloys in biocompatibility.
-
-
Energy & Electronics
-
Thermal Management: High conductivity enables heat dissipation in satellites and nuclear reactors.
-
Innovations in Coating Technology
-
Multilayer Protective Systems
-
Outer CVD Layers: SiC and Si₃N₄ coatings act as primary oxygen barriers, resistant to erosion up to 1700°C.
-
Inner Glass-Forming Layers: Boron compounds oxidize to seal cracks, enhancing durability in cyclic thermal environments.
-
-
Nanotechnology Integration
-
Carbon Nanotube (CNT) Coatings: Improve corrosion resistance and bioactivity in medical implants while reducing toxicity through functionalization.
-
-
Functional Grading
-
FGMs (Functionally Graded Materials): Combine ceramics and metals to optimize thermal and mechanical performance in hypersonic vehicles.
-
Challenges and Future Directions
-
Oxidation Below 760°C: Moisture-induced volatility in borate glasses remains a hurdle, necessitating advanced sealing techniques.
-
Cost Reduction: Scaling production of high-performance PAN-based fibers and optimizing CVI processes could lower costs for broader adoption.
-
Impact Resistance: Developing hybrid composites with carbon nanotubes or graphene may address brittleness in thin coatings.
Conclusion
Carbon-carbon composite coatings represent a fusion of material science and engineering innovation, driving advancements from space exploration to regenerative medicine. With ongoing research into self-healing mechanisms and nanotechnology, these coatings are poised to revolutionize industries demanding extreme performance. For detailed technical specifications and product solutions, visit CFCCarbon.
References
-
Frontiers in Materials: Carbon-Carbon Composites Overview
-
ScienceDirect: C/C Composite Production
-
Nature: 3D-C/C Composites in Medical Implants
-
Springer: CNT Coatings for Biomedical Use
related news /articles:
Introduction of high-temperature coatings on CC composite material
Advanced Protective Coatings for Carbon-Carbon Composites
Advanced Coatings for Carbon fiber Carbon Composites
High-Performance Coatings for Carbon fiber Carbon Composites