Title: Advanced Protection Mechanisms Against Catalytic Oxidation in Carbon-Carbon Composites
Subtitle: Innovations in Coating Technologies and Dopants for Enhanced Thermal Stability
Introduction
Carbon-carbon (C-C) composites are critical materials for high-temperature applications, including aircraft brakes and hypersonic flight systems. However, their susceptibility to catalytic oxidation—accelerated by alkali metal residues from de-icing agents or environmental
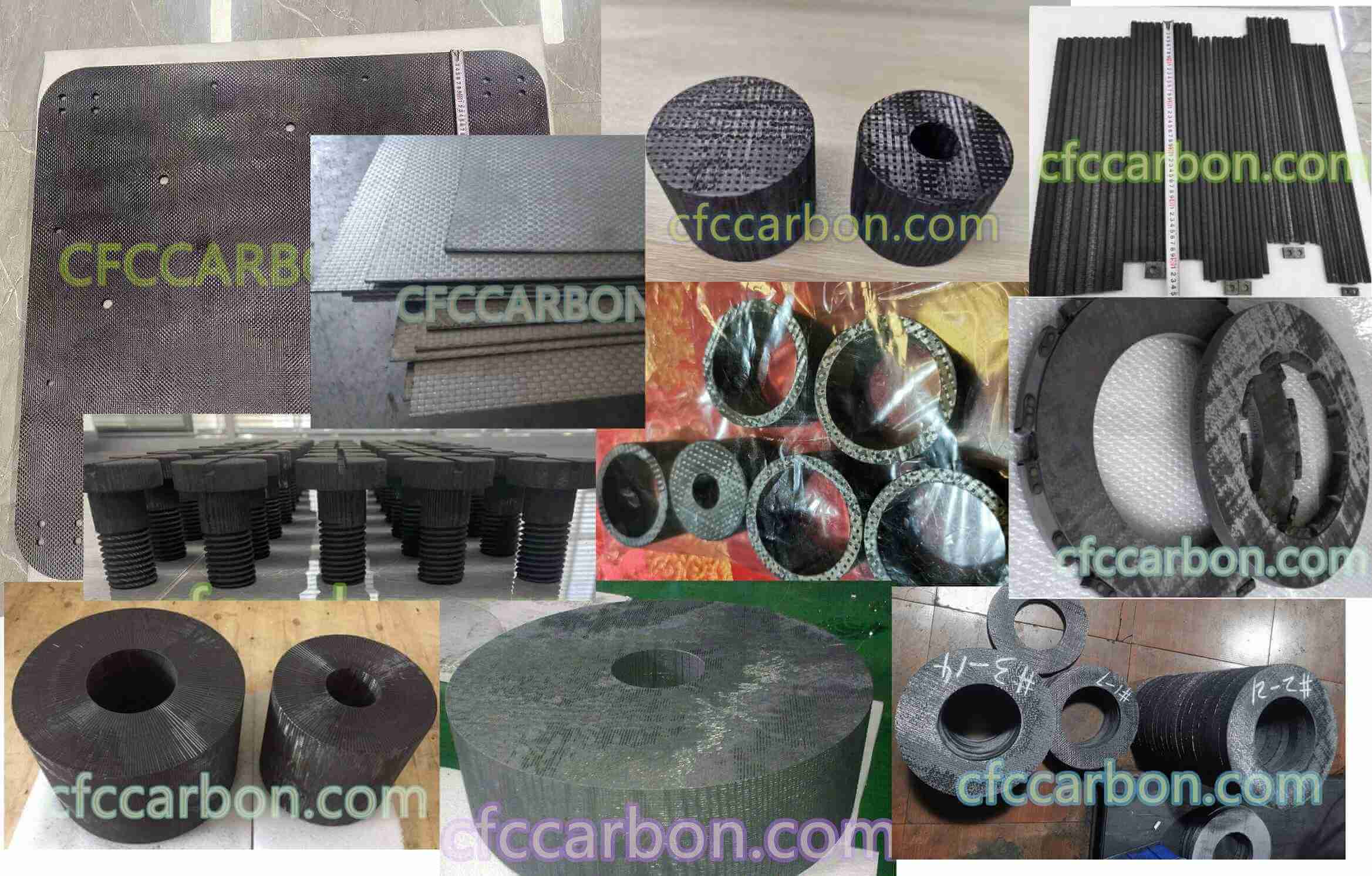
carbon fiber composite material manufacturer in China(1)
contaminants—poses significant challenges. This article explores cutting-edge strategies to mitigate catalytic degradation, focusing on coating technologies, surface treatments, and dopants that enhance oxidation resistance while addressing thermal expansion mismatches.
1. The Challenge of Thermal Expansion Mismatch in Protective Coatings
Protective coatings like silicon carbide (SiC) and silicon nitride (Si₃N₄) are widely used due to their thermal expansion coefficients (CTE) closely matching carbon substrates (~3–5 × 10⁻⁶/K vs. ~1 × 10⁻⁶/K for C-C composites)36. However, even minor CTE discrepancies can induce coating cracks during thermal cycling, allowing oxygen diffusion and accelerating oxidation. Recent advances, such as graded multilayer coatings and carbon fabric reinforcement within silicide layers, have reduced crack density by over 80%. For instance, mechanically treated surfaces combined with carbon fiber integration create a transitional layer that smoothens CTE gradients, significantly enhancing durability.
2. Surface Treatments and Phosphorus-Based Inhibition
Phosphoric acid treatments have emerged as a cost-effective solution to neutralize catalytic impurities. Labruquere et al. demonstrated that phosphoric acid reacts with alkali metals (e.g., K, Na) to form inert orthophosphates, reducing carbon loss from 12% to 2% at 650°C. At higher temperatures (>600°C), phosphorus species bind to active carbon sites, blocking oxygen access. However, this protection diminishes above 900°C due to phosphorus layer delamination12. Innovations like hybrid coatings combining SiC with ZrB₂ or HfC—materials with self-healing oxide layers (e.g., SiO₂-ZrO₂)—show promise in extending operational limits to 1950°C.
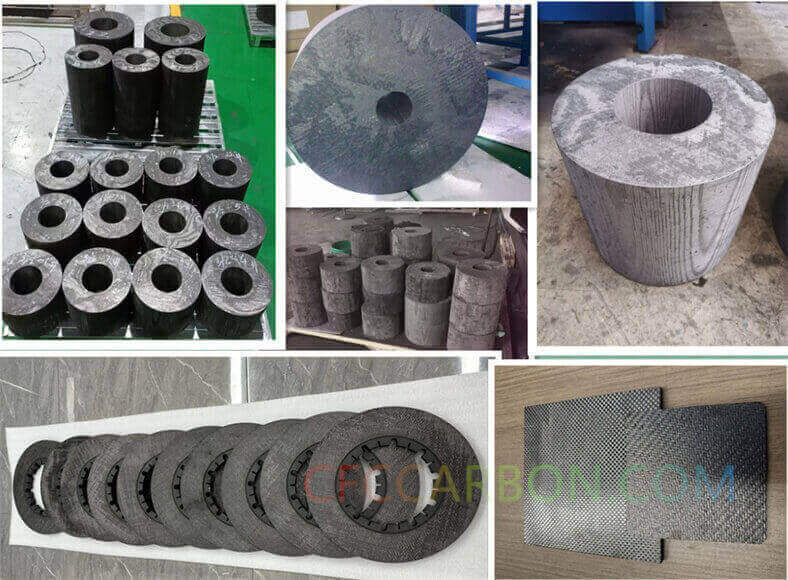
3D 4D carbon fiber composite material manufacturer factory -airplane brake disc plates sheets U L profiles-2D(s)
3. Boron and Phosphorus Dopants: Dual Roles and Controversies
Doping C-C composites with boron or phosphorus introduces complex effects. Boron enhances graphitization and forms protective B₂O₃ glass at high temperatures, but low concentrations (≤2 wt.%) paradoxically catalyze oxidation, while higher doses (5 wt.%) inhibit it. Phosphorus, via C-O-PO₃ bonds, effectively passivates calcium-based catalysts but struggles against alkali metals. Recent studies suggest combining dopants with reactive melt infiltration (RMI) to uniformly distribute protective phases, such as SiC-BN matrices, which reduce porosity and improve oxidation resistance by 30%.
4. Emerging Coating Technologies: Beyond Traditional Ceramics
Ultra-high-temperature ceramics (UHTCs) like ZrB₂-SiC and HfB₂-SiC are revolutionizing oxidation protection. These coatings form refractory oxide layers (ZrO₂, HfO₂) that resist ablation and reduce oxygen permeability. For example, in-situ ZrB₂-SiC coatings synthesized via pack cementation exhibit 40% lower mass loss than pure SiC at 1500°C due to synergistic SiO₂-B₂O³ glass formation. Additionally, nanostructured dopants (e.g., SiC nanowires) enhance fracture toughness by deflecting cracks and reducing CTE mismatches.
5. Industrial Applications and Future Directions
C-C composites are pivotal in reusable launch vehicles and hypersonic systems, where oxidation protection is mission-critical. Companies like CFC Carbon (www.cfccarbon.com) are pioneering multilayer coatings integrating SiC, UHTCs, and nanoscale additives for aerospace brakes. Future research aims to develop dynamic coatings that adapt to thermal stresses, such as MoSi₂-based systems with high-temperature plasticity. Computational modeling of ablation mechanisms and flame interactions will further optimize these systems.
Conclusion
The catalytic oxidation of C-C composites remains a formidable challenge, but advancements in coating engineering, dopant chemistry, and nanostructuring are closing the gap. By addressing thermal expansion mismatches and leveraging reactive surface treatments, the next generation of C-C materials will achieve unprecedented durability in extreme environments. Collaborative efforts between academia and industry, such as those highlighted by CFC Carbon, are essential to translate lab-scale innovations into real-world solutions.
related news /articles
Oxidation kinetics and mechanisms of a 2D C/C composite (1)
Oxidation kinetics and mechanisms of a 2D C/C composite (3)
Performance Challenges in Carbon-Carbon Composite Coatings
Understanding Oxidation Mechanisms in Carbon-Carbon Composites