Definition of pyrolytic graphite:
Pyrolytic graphite is a new type of carbon material. It is a pyrolytic carbon with higher crystal orientation that is deposited on a graphite matrix of 1800℃~2000℃ by chemical vapor deposition of high-purity hydrocarbon gas under a certain furnace pressure. It has high density. (2.20g/cm), high purity (impurity content (0.0002%) and anisotropy of thermal, electrical, magnetic and mechanical properties. It can still maintain a vacuum of 10mmHg at around 1800°C.
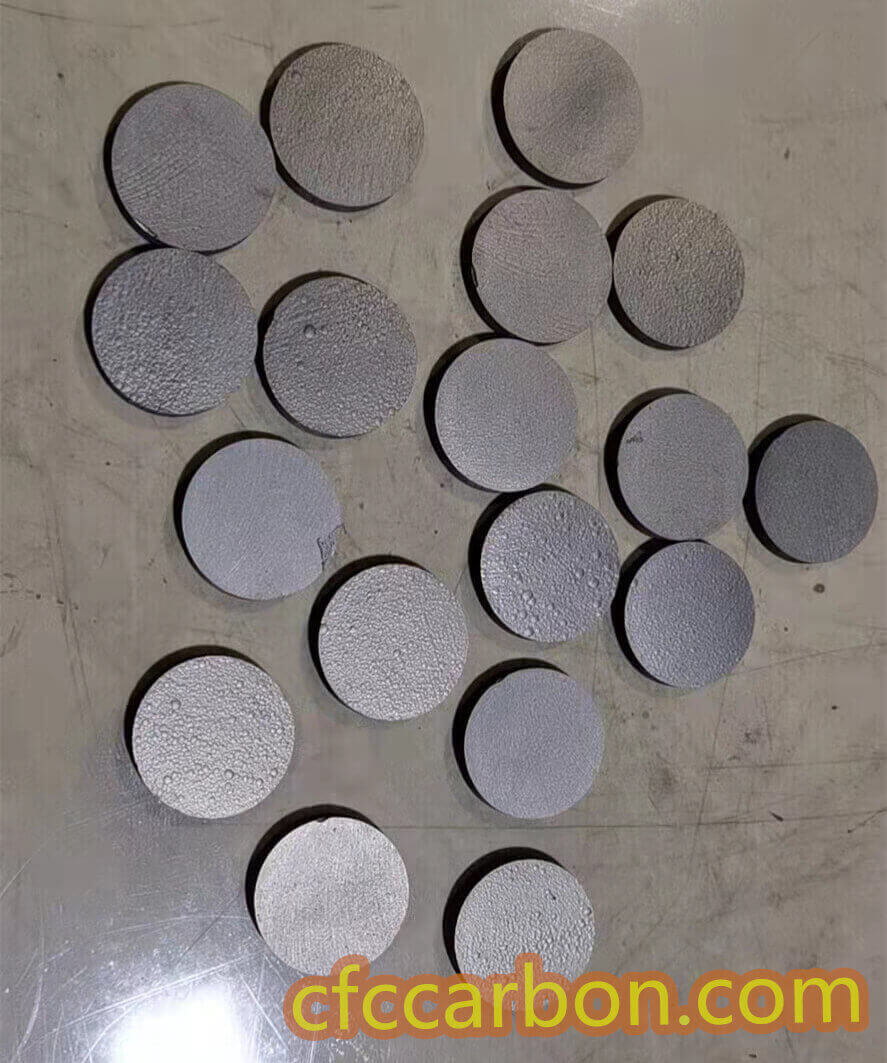
PG sheet-pyrolytic graphite plate disc crucible pipe tube (10)
Production process, production method:
Pyrolytic graphite is a product of high-temperature vapor deposition. At present, intermediate frequency induction heating (or choke-type graphite heater heating) vacuum furnace is the main equipment for its preparation. The induction heating deposition furnace is shown in Figure 3-9. The graphite heating element and the substrate deposited in the graphite sleeve are set in the induction coil, and they are all heated by induction.
When starting, the air in the furnace is first exhausted, and the vacuum degree is below 133.3~266. 6Pa, and then the power is sent to increase the temperature. When the substrate reaches the specified deposition temperature, a mixture of nitrogen and hydrocarbon gas mixed in a certain proportion is sent , Pyrolysis. In this process, the vacuum pump continuously extracts the exhaust gas, and the mixture is input quantitatively. After a certain period of deposition, a pyrolytic carbon layer with a specified thickness is obtained. The whole device is divided into four systems: air supply, heating, exhaust, and monitoring.
The raw material for pyrolysis can be natural gas, liquefied petroleum
gas, coal gas or benzene and toluene vapor, etc. The dilution carrier can be nitrogen, sensitizer, hydrogen, etc. to control the deposition rate and density. The matrix can be refractory metals such as pan, copper, molybdenum, or massive
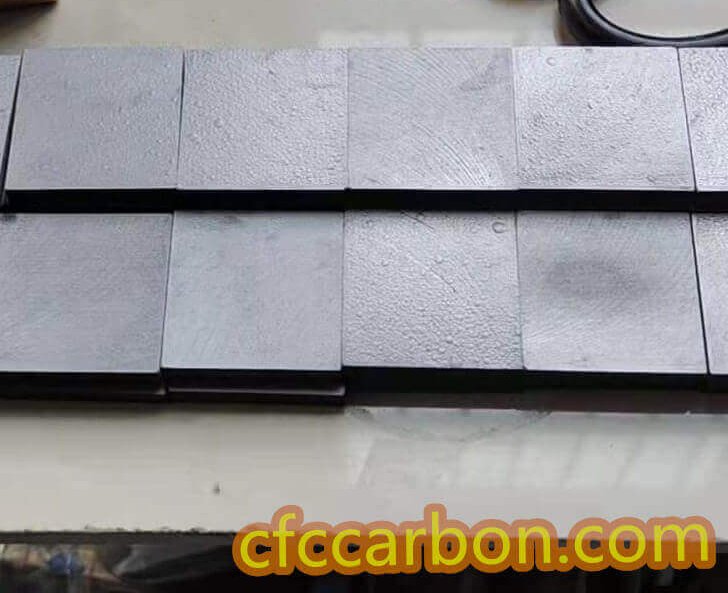
PG sheet-pyrolytic graphite plate disc crucible pipe tube (2)
graphite. For pyrolytic carbon products used in semiconductors and electronic technology, high-purity graphite should be used as the matrix. The matrix must be finely processed and polished to facilitate demoulding. The corners should be rounded as far as possible to reduce the internal stress of pyrolytic charcoal.
During the deposition process, the three main parameters of temperature, pressure, and gas flow must be stabilized. The deposition time is determined by the thickness of the required pyrolysis layer. The best choice of these parameters depends on the use and properties of the pyrolytic graphite. Certainly.
Properties of pyrolytic graphite:
Grade: Pyrolytic Graphite |
Properties: |
Density: 2.18-2.2 g/cm3 |
Compressive strength: 83.6 Mpa AB direction |
Tensile strength: 75 Mpa AB direction |
Ash content: 0.02-0.005% |
Thermal conductivity: 300-400W/m.k AB direction |
3.5-5 W/m.k C direction |
C.T.E: 3.2×(10-6/℃) AB direction |
17-26×(10-6/℃) C direction |
Specific resistance: 2×10-4 Ω.cm AB direction |
0.6Ω.cm C direction |
Distance between Carbon atom layer(002): </= 3.42 A |
Air impermeability: He transmissivity<10-10cm2 |
Sizes max: |
Dia 90×5mm; |
90×90×5mm |
90×200×5mm |
Max width:180mm, length: 800mm, thickness: 10 mm |
Others to be confirm. |
Features of pyrolytic graphite:
The surface is dense, without pores, and easy to machine.
High purity, total impurity content <20ppm, good air tightness.
High temperature resistance, the strength increases with the increase in the use temperature, and the strength reaches the highest value of 3600°C at 2750°C.
The modulus of elasticity is low, the thermal conductivity is high, the coefficient of thermal expansion is small, and the product has excellent thermal shock resistance.
Good chemical stability, resistance to acid, alkali, salt and organic reagents. It has no effect on molten metal, slag and other corrosive media. The oxidation is not obvious below 400 ℃ in the atmosphere, and the oxidation rate increases significantly at 800 ℃.
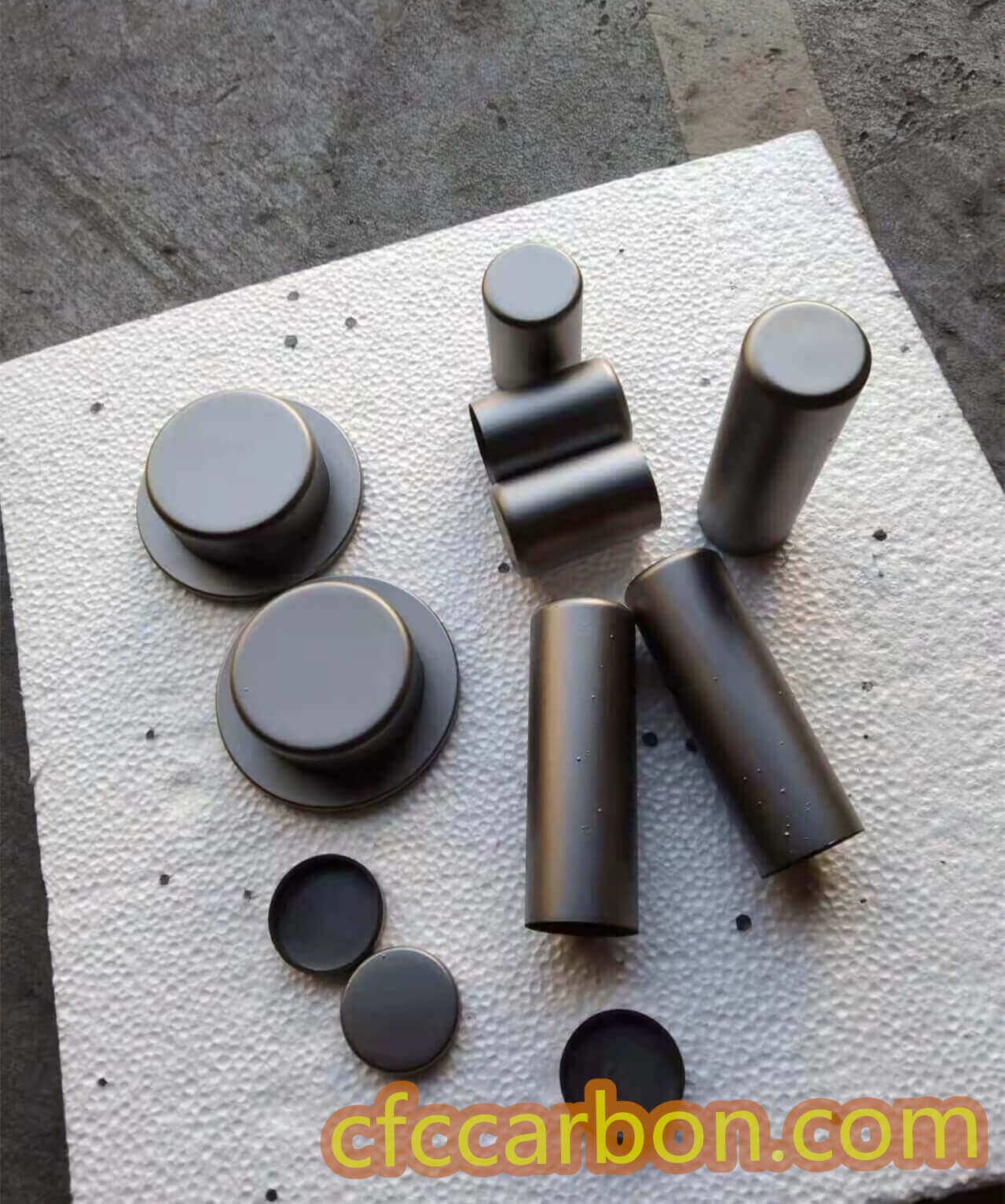
PG sheet-pyrolytic graphite plate disc crucible pipe tube (4)
No gas is released under high temperature, and the vacuum of 10-7mmhg can be maintained at about 1800℃.
Application areas of pyrolytic graphite:
Graphite heater
Diversion bucket
PBN/PG composite heater
Atomic absorption tube
The development history and future trends of pyrolytic graphite:
Pyrolytic graphite refers to the decomposition and polymerization of carbon-containing compounds on the surface of the hot solid substrate at a temperature of about 2100. 2500C) recombined carbon that is consistent with the graphite structure.
As early as 1880, Sawyer et al. used hydrocarbon gas to obtain pyrolytic graphite on the filament; in the late 1940s and early 1950s, Brown et al. limited their interest in the laboratory and obtained small pieces of heat by direct energization. Degraphite; In 1959, the American Muncean Company began mass production of pyrolytic graphite for the purpose of nuclear fuel coatings, fire front cones, etc., and was able to produce larger and special-shaped parts around 1960. In the field of aerospace; in 1963, British scholars first produced highly oriented pyrolytic graphite by pressure heat treatment; in 1962, China also carried out the research and development of pyrolytic graphite at the Institute of Metal Research of the Chinese Academy of Sciences and the Shanxi Institute of Coal Chemistry. Lanzhou and other places established production bases, and successfully used pyrolytic stone springs in the throat lining of missiles, electron tube grids and rocket nozzles in the 1970s; in 1975, Fitxer and others published polyimide (PI). , A research report on the formation of high-crystallinity stone products after pyrolysis carbonization and high-temperature graphitization; after entering the 1980s, the scientific research team headed by Murakami Mutsuki started from POD and counterpoint polymerization. High polymers such as phenylene (PPP), polynaphthalene (PN) and polyanthracene (PA) have been heat-treated to over 3000C to obtain pyrolytic graphite with high crystallinity and a highly preferential orientation of the surface graphite layer; In 1988, the use of mold carbonization to obtain highly oriented pyrolytic stone disk film was carried out: in the 1990s, scholars such as Nyslen B, Shinohara Hiroharu and other scholars prepared mesophase pyrolytic graphite. The research and development of scientists has been greatly enriched. People’s understanding of the connotation of pyrolytic graphite, and a wave of research and application of it has been set off in countries all over the world.
In order to obtain specific energy of pyrolytic graphite, scientists have devised a development method to transform the extremely directional deposition of carbon crystallites on the substrate and the cross-linking between the two-dimensional structure of the carbon crystallites into an extremely developed three-dimensional. Its pyrolysis The specific preparation methods of graphite include: (1) Chemical vapor deposition method using gas or liquid carbide as carbon source (including ① direct heating method using matrix material as heating element. This method is mostly used in the laboratory, and the matrix is directly energized. The high temperature is only suitable for parts with thin deposits, simple shapes and smaller volumes. The disadvantage of this method is that the pyrolytic graphite of the deposits is not homogeneous in the thickness direction, and the pyrolytic graphite gradually grows , The resistance of the heating element will gradually decrease. ②The indirect heating method in which the culture body is placed inside or outside the heating element and heated to a high temperature by the radiation of the heating element. This method is especially suitable for induction heating to produce larger sizes and thicknesses. Large (because there is no pyrolytic stone house deposited on the outside of the heating tube, so the resistance change is small, and the thickness sample can be made) and the parts with complex shapes (such as plate-shaped, tubular, flat-end and boat-shaped products)]; (2) Conventional or transformational solid-phase pyrolysis carbonization using polymers as raw materials to obtain pyrolytic graphite through high temperature treatment; (3) Liquid phase carbonization to prepare mesophase carbon, and then high-temperature heat treatment to obtain pyrolytic graphite Law.
The formation mechanism and structure of pyrolytic graphite: From the reaction research accumulated in the literature and the analysis of experimental data, the carbon-containing compound as the carbon source is pyrolyzed and broken, the low-molecular component is removed, and the pyrolytic polymerization reaction process, the carbon atom Between SP2 and SP3 two hybrid modes, solid carbon crystals containing huge molecules with different pore configurations and irregular arrangements are generated, and then after high-temperature crystal rearrangement, it becomes a pyrolysis consistent with the graphite structure. graphite. As for its exact generation mechanism, it needs to be further supplemented and verified using modern and future innovative testing methods and analysis methods combined with the process. The structure of pyrolytic graphite is a two-dimensional ordered structure consisting of a hexagonal network of carbon atoms with interlaced layers. After high temperature treatment (above 3000 degrees), it will become a three-dimensional ordered crystal, which is close to graphite single crystal. In addition, its crystals have high orientation and anisotropy, which leads to the anisotropy of bulk pyrolytic graphite, and it is easy to deform and crack inside. In addition, due to the unevenness of the substrate surface or the formation process of pyrolytic graphite The surface of the pyrolytic stone room is in a unique round convex and concave state mixed with a nucleus similar to granular soot, but after the sea treatment above 3000C, it is almost as smooth and shiny as a mirror-like silver-gray metallic light ocean. It It does not contain any macroscopic pores, but contains a large number of vacant atoms, edge activated carbon atoms, dislocations, grain boundaries, stacking faults and other defects.
The performance of pyrolytic graphite is in addition to many characteristics of ordinary graphite such as high temperature resistance, corrosion resistance, self-lubricating, thermal and electrical conductivity, heat resistance, impact resistance, and good mechanical plus T performance, as well as high purity And impurity content is very small (ash content is only 0.001-0.004wt*%), good oxidation resistance (under 700c, its oxidation resistance is more than 10 times higher than ordinary artificial graphite), compact material (its density is 1.80 -2·22g/cm’, which is roughly equal to the theoretical density of Ishiguro) and very small air permeability (approximately 7 seconds in cm (He-chamber)], a certain degree of flexibility, and an extremely prominent anisotropy (At room temperature, the ratio of the thermal conductivity in the a-direction 4 c-direction exceeds 100, and the thermal expansion value in the a-direction is negative. The direction is positive, and the electrical resistivity in the a-direction and c-direction differs by nearly 1000 times) , Also found that it has a good diamagnetic and high sound transmission rate function.
In addition to the application of pyrolytic graphite in the field of space technology, it can be used as nozzles, throat linings, nose cones, leading edges, antimagnetic balls for satellite attitude control, etc., in nuclear reactors to prevent the leakage of nuclear fission products. Granular nuclear fuel or nuclear fuel shell coating material; it can be made into electron tube grids, semiconductor P-type or N-type materials, epitaxial wafers for semiconductor production, electrical shielding materials, brushes for voltage regulators, and X Ray monochromator and neutron wave device, etc.; can also be used as a sealing material, sealing gasket and high temperature furnace insulation material under island temperature conditions; also can be used as an electrode for metallurgical equalization and boat and electrochemical analysis ; It has also been practically applied in the field of clinical medicine and acoustic materials.
It should be noted that the research and development of pyrolytic graphite has not yet ended. Although it has a history of more than one hundred years of development, its special and excellent nature has made an indelible contribution to mankind’s conquest of nature and the promotion of social modernization. However, there are still many doubts and suspenses in the discipline, and many new reactions, new processes, new applications, reduction of production costs, and potential impacts on humans and nature that have yet to be discovered. Questions to be solved.
See the video of PG pyrolytic graphite sheet plate block disc pipe tube crucible at:
The price of pyrolytic graphite: Its cheap, not expensive. but due to different sizes and quantity, the price varies a little. Please send email for more enquiries.
You can see the product video of pyrolytic graphite on this link: https://youtu.be/yfd3LQrs3uI
Related news /knowledges:
Pyrolytic carbon material, pyrolytic graphite material
Pyrolytic graphite sheets
The carbonization/pyrolysis process –principle
Pyrolytic graphite plates
pyrolytic graphite crucible plates sheets