Overcoming Performance Challenges in Carbon-Carbon Composite Coatings: Innovations and Solutions
By CFC Carbon R&D Team | Updated: May 17, 2025
1. What Are Carbon-Carbon (C/C) Composite Coatings?
Carbon-carbon composites (C/C) are advanced materials combining carbon fibers with a carbon matrix, renowned for their exceptional
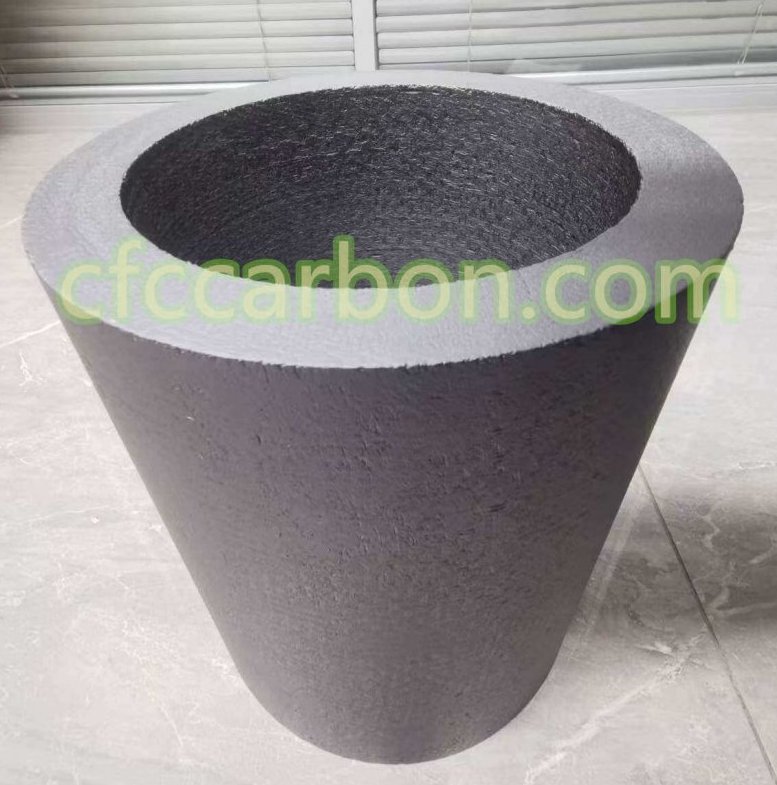
SiC coating carbon fiber composite material-CC-CFC (2)
strength-to-weight ratio and thermal stability above 2,300 K. However, their susceptibility to oxidation above 750 K necessitates protective coatings. C/C composite coatings are multilayer systems designed to shield the substrate from oxygen penetration and thermal degradation. These coatings typically include:
-
Transition layers (e.g., SiC) to mitigate thermal expansion mismatch
-
Ultra-high temperature ceramic (UHTC) outer layers (e.g., ZrB₂-SiC, HfC) for ablation resistance
-
Self-healing glass sealants (e.g., borate or phosphate-based) to repair microcracks
CFC Carbon Co., Ltd., a global leader in C/C manufacturing, emphasizes that coatings must balance oxidation resistance with mechanical compatibility to prevent spallation—a critical failure mode in aerospace applications.
2. Manufacturing, Classification, and Applications
Production Techniques
-
Chemical Vapor Deposition (CVD): Ensures uniform coating penetration for complex geometries (e.g., rocket nozzle liners).
-
Plasma Spray: Cost-effective for large-scale components like brake discs.
SiC coating carbon fiber composite material-CC-CFC (1)
-
Slurry Method: Ideal for doping nanostructures (e.g., carbon nanotubes) to enhance fracture toughness.
Product Categories
Coating Type | Key Materials | Applications |
---|---|---|
Single-phase | SiC, ZrB₂ | Transition layers |
Multiphase | ZrB₂-SiC, HfC-TaC | Hypersonic vehicle leading edges |
Nanostructured | CNT-doped SiC | High-stress turbine components |
Glass-sealed | B₂O₃, CSZP phosphates | Long-duration rocket engines |
Performance Characteristics
-
Thermal Stability: Withstand temperatures up to 2,200 K (e.g., HfC-ZrC coatings).
-
Oxidation Resistance: CSZP-based coatings reduce oxygen permeability by 40% compared to borate glasses.
-
Moisture Resistance: Modified phosphate glasses minimize hydrolysis-induced swelling.
3. Current Challenges and Solutions
Key Performance Issues
-
Coating Spallation
-
Cause: CTE mismatch between coating (e.g., SiC, α=4.5×10⁻⁶/K) and C/C substrate (α=1×10⁻⁶/K).
-
Solution: Gradient carbide transition layers (e.g., SiC/ZrB₂-SiC) distribute strain gradually.
-
-
Borate Glass Corrosion
-
Cause: High oxygen permeability (B₂O₃: ~10⁻⁷ cm²/s) accelerates SiO₂ dissolution in SiC coatings.
-
Innovation: Replace borates with low-permeability Ca₀.5Sr₀.5Zr₄(PO₄)₆ (CSZP) ceramics.
-
-
Moisture Sensitivity
-
Risk: Boric acid formation (H₃BO₃) weakens adhesion.
-
Mitigation: Hydrophobic dopants (e.g., graphene) in sealant layers.
-
-
Coating Thickness Trade-offs
-
Thin coatings (<50 µm) improve adhesion but degrade rapidly.
-
Thick coatings (>200 µm) resist corrosion but promote crack propagation.
-
4. Advancements in Coating Technology
Recent breakthroughs address these limitations:
-
Internal Oxidation Barriers: CFC Carbon’s proprietary SiC-whisker-reinforced C/C preforms slow substrate oxidation even if the outer coating fails.
-
Diamond-like Carbon (DLC) Coatings: Reduce friction coefficients by 60% in machining applications while maintaining high hardness (30–50 GPa).
-
Tantalum (Ta) CVD Coatings: Enhance compressive strength of porous C/C foams by 300% through strut reinforcement.
5. Future Directions
-
Multifunctional Coatings: Combine UHTCs with sensors for real-time health monitoring.
-
AI-Driven Process Optimization: Machine learning to predict CTE gradients and crack propagation.
-
Sustainable Manufacturing: CFC Carbon’s low-cost batch production techniques reduce energy use by 25%.
Conclusion
While current C/C coatings face challenges in spallation and environmental durability, innovations in material design (e.g., CSZP, DLC) and process engineering (e.g., nanostructured doping) are paving the way for next-generation solutions. CFC Carbon continues to lead this evolution, offering tailored coatings for aerospace, defense, and energy sectors.
Explore CFC Carbon’s Coating Solutions: www.cfccarbon.com
related news /articles:
High-Performance Coatings for Carbon fiber Carbon Composites
Advanced Coatings for Carbon fiber Carbon Composites
Introduction of high-temperature coatings on CC composite material
Advanced Protective Coatings for Carbon-Carbon Composites