Unlocking the Potential of Multidirectional Carbon-Carbon Composites: Manufacturing, Applications, and Advanced Modeling
*By [Potter Li/CFCCARBON CO., LTD], May 15, 2025*
1. What Are Carbon-Carbon Composites?
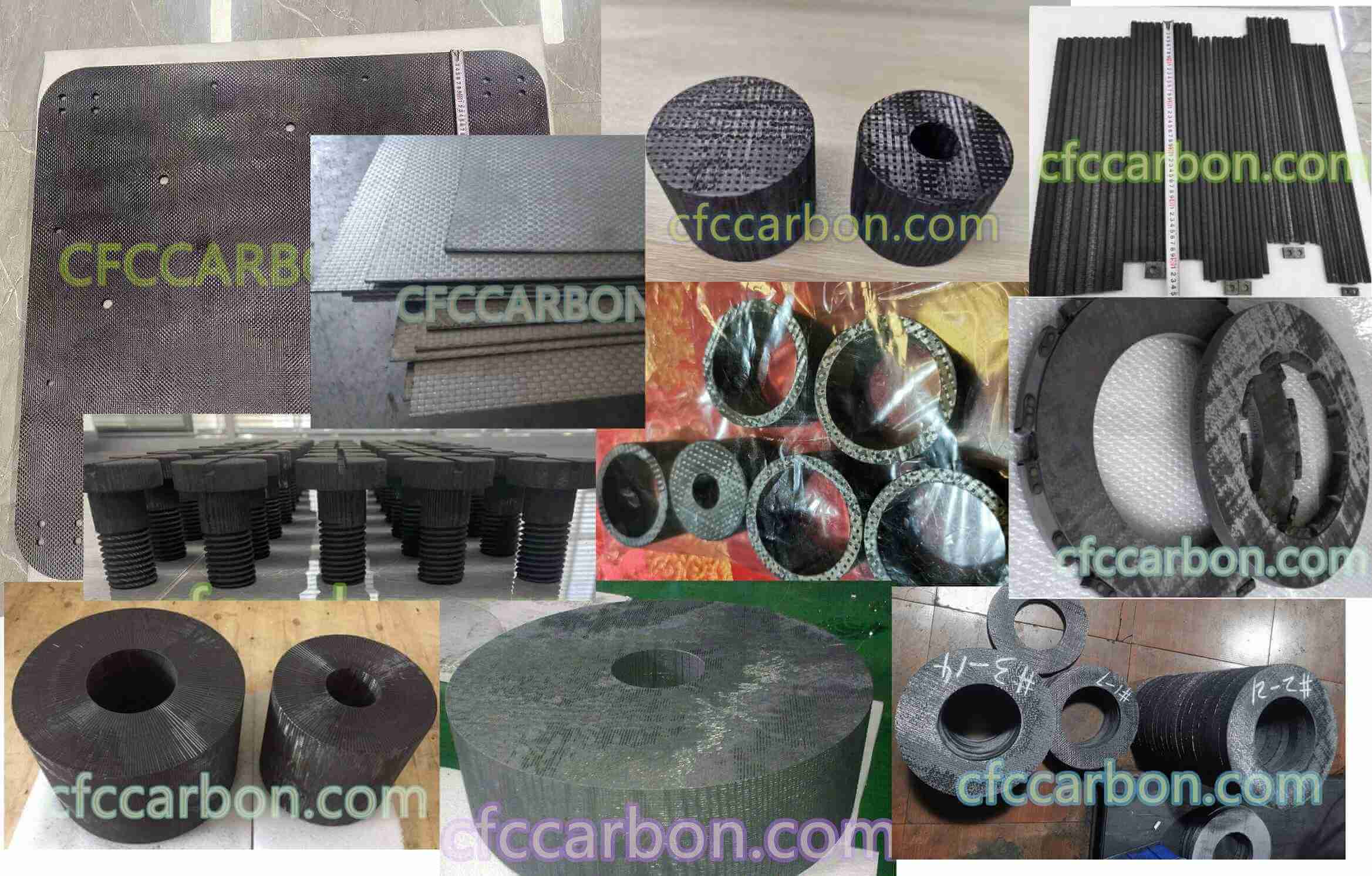
carbon fiber composite material manufacturer in China(1)
Carbon-carbon composites (C/C composites) are high-performance materials composed of carbon fibers embedded in a carbonaceous matrix. These all-carbon materials are renowned for their exceptional thermal stability, mechanical strength, and lightweight properties, making them indispensable in aerospace, defense, and high-temperature industrial applications215. Unlike traditional composites, C/C composites retain structural integrity at temperatures exceeding 2,000°C, a feature critical for rocket nozzles, aircraft brakes, and thermal protection systems in reusable launch vehicles28.
For deeper insights, explore CFRP applications at CFC Carbon.
2. Production and Classification of Multidirectional Carbon-Carbon Composites
Manufacturing Techniques
C/C composites are produced via two primary methods:
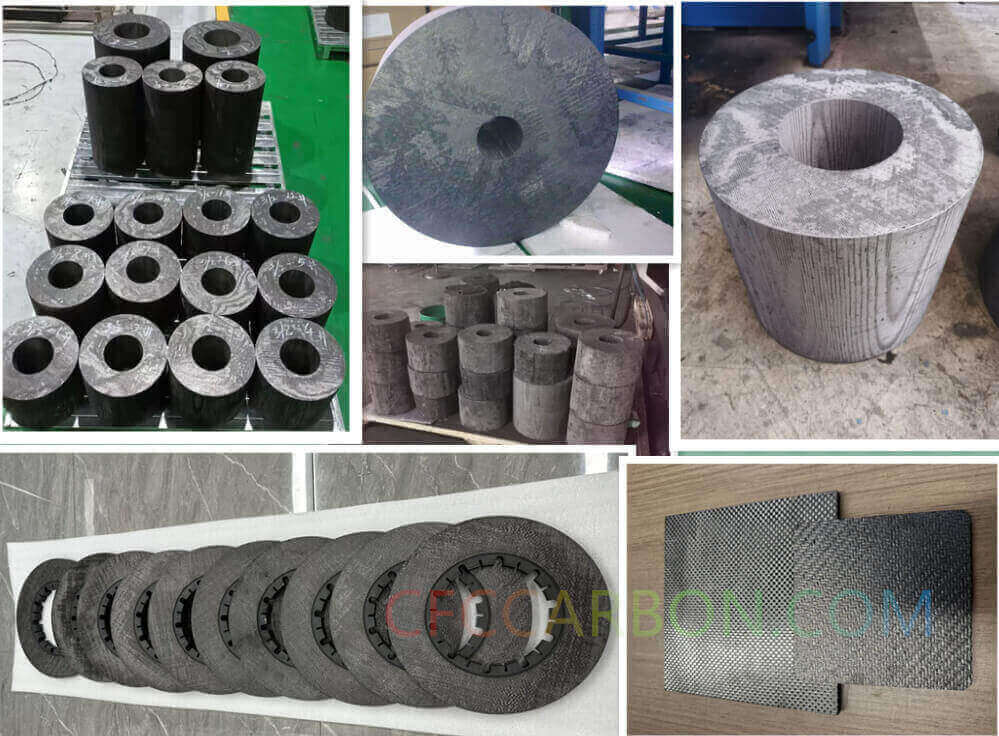
2D 3D 4D 5D carbon fiber composite material manufacturer factory -airplane brake disc plates sheets U L profiles-2D(6)
-
Liquid Impregnation Pyrolysis (LIP): Thermoplastic or thermosetting resins (e.g., phenolic, pitch) are infiltrated into carbon fiber preforms and carbonized at high temperatures.
-
Chemical Vapor Infiltration (CVI): Hydrocarbon gases decompose to deposit pyrolytic carbon onto fibers, creating a dense matrix with superior thermal conductivity2.
Advanced methods like high-pressure processing (HIP) reduce porosity and enhance density, while hybrid techniques combining LIP and CVI optimize cost and performance.
Multidirectional CC Composite Models
The multidirectional model involves layered fiber architectures (2D, 3D, or MD weaves) to achieve balanced mechanical and thermal properties. Key classifications include:
-
Unidirectional (UD): Fibers aligned in a single direction for high axial strength.
-
2D/3D Woven: Cross-ply or orthogonal weaves for enhanced fracture resistance.
-
Needle-Punched: Z-direction reinforcement via stitching for improved interlaminar strength.
Unit Cell Modeling
The composite cylinder assemblage (CCA) model simplifies multidirectional analysis by treating the material as a unit cell with subcells representing fiber bundles and matrix regions. This approach accounts for voids and anisotropies:
-
Void Effects: Spherical or cylindrical voids reduce matrix stiffness, modeled using composite sphere/cylinder assemblages[citation:Original Text].
-
Fiber-Matrix Interactions: Transverse isotropy arises from cylindrical voids, while analytical CCA models predict thermoelastic properties with high accuracy.
Finite-element analyses confirm that hexagonal arrays and CCA models yield nearly identical results, validating their use for predicting elastic, thermal, and viscoelastic behaviors.
3. Performance Advantages and Applications
Key Properties
-
Thermal Stability: Withstands extreme temperatures (up to 3,000°C) without degradation.
-
High Strength-to-Weight Ratio: 5x stronger than steel at 1/4 the weight, ideal for aerospace.
-
Low Thermal Expansion: Maintains dimensional stability under thermal stress.
Industry Applications
-
Aerospace: Rocket nozzles, re-entry vehicle heat shields, and aircraft brake systems.
-
Automotive: Lightweight brake discs and high-temperature engine components.
-
Energy: Solar thermal systems and nuclear reactor components.
4. Innovations in Multidirectional Modeling
Recent advancements focus on integrating nanomaterials like carbon nanotubes (CNTs) and graphene to enhance interfacial bonding and fracture toughness215. For instance:
-
CNT-Grown Fibers: Improve stress transfer between fibers and matrix, reducing delamination risks.
-
Hybrid Composites: Combine pitch-based fibers (high conductivity) with PAN-based fibers (high strength) for tailored performance2.
Computational tools like NDPROP and DCAP enable flexible unit cell configurations, allowing engineers to simulate diverse fiber orientations and void distributions efficiently.
5. Overcoming Oxidation Challenges
C/C composites require oxidation-resistant coatings (e.g., silicon carbide or zirconium carbide) for prolonged use in oxidative environments. Multilayer coatings and matrix inhibitors (boron, silicon) further enhance durability.
6. Future Trends and Sustainability
The carbon composites market is projected to grow exponentially, driven by demand in electric vehicles, wind energy, and space exploration. Sustainable production methods, including bio-based resins and recyclable thermoplastic matrices, are gaining traction.
Conclusion
Carbon-carbon composites represent the pinnacle of material science, combining unmatched thermal and mechanical properties with design flexibility. As modeling techniques evolve and manufacturing costs decline, their adoption will expand into new sectors, revolutionizing industries reliant on high-performance materials.
For cutting-edge C/C composite solutions, visit CFC Carbon.
related news /articles:
Mechanics of multidirectional carbon-carbon composite materials (1)-abstract
4D C/C composite material manufacturer in China
Carbon fiber Composites: Innovations and Applications in Aerospace and Beyond
CVI CVD Carbon Carbon Composite Material, Manufacturer in China