1. What is Carbon-Carbon Composite?
Carbon-carbon (C/C) composites are advanced materials composed of carbon fiber reinforcements embedded in a carbon or graphite matrix. Developed initially for aerospace applications, these composites combine exceptional thermal stability (up to 2,000°C in non-oxidizing environments), high strength-to-weight ratios, and resistance to thermal shock. Unlike traditional ceramics, C/C composites retain structural integrity under extreme temperatures, making them ideal for reentry vehicles, rocket nozzles, and high-performance braking systems. Learn more about their properties at CFCCarbon.com.
2. Production and Manufacturing Processes
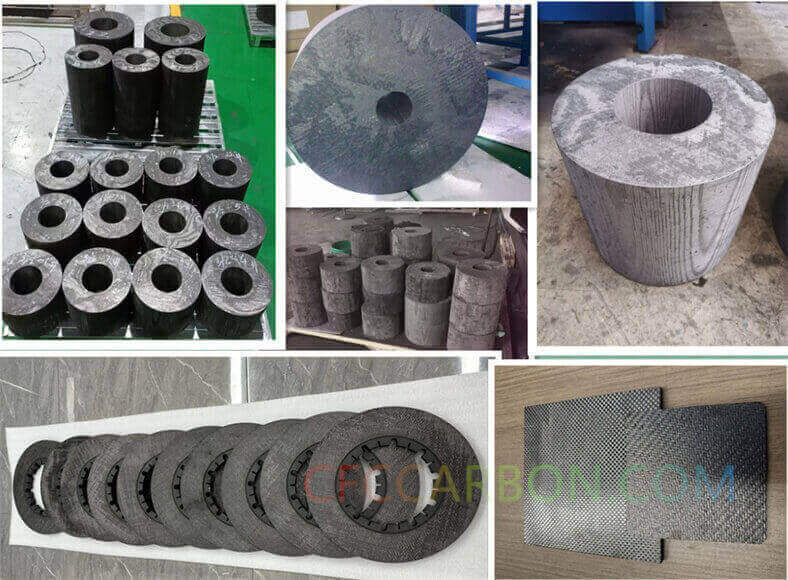
3D 4D carbon fiber composite material manufacturer factory -airplane brake disc plates sheets U L profiles-2D(s)
The fabrication of C/C composites involves three critical stages:
-
Preform Creation: Carbon fibers are woven into a preform structure (unidirectional, bidirectional, or 3D-weave) to meet design load requirements.
-
Densification: The preform is infused with a carbon matrix via Chemical Vapor Infiltration (CVI) or Liquid Polymer Impregnation (LPI). CVI uses hydrocarbon gases to deposit pyrolytic carbon, while LPI employs resins or pitches that are carbonized post-impregnation.
-
Graphitization: High-temperature treatment (up to 2,500°C) enhances crystallinity and mechanical properties.
Advanced techniques like 3D printing of molds (using SLA resins) are now streamlining preform production for complex geometries.
3. Classification and Applications
C/C composites are categorized based on their reinforcement structure and matrix type:
-
Aerospace: Space shuttle leading edges, rocket nozzles, and missile components.
-
Automotive: Formula One brake discs and high-end sports car components.
-
Industrial: Furnace fixtures, thermal shields, and wind turbine blades.
-
Defense: Heat-resistant armor and hypersonic vehicle parts.
4. Performance Characteristics and Oxidation Behavior
Key Properties:
-
High Thermal Resistance: Retains strength above 2,000°C with protective coatings.
SiC coating carbon fiber composite material-CC-CFC (2)
-
Low Thermal Expansion: Minimizes deformation under rapid temperature changes.
-
Lightweight: Density ranges from 1.6–1.98 g/cm³, enabling fuel efficiency in aerospace.
Oxidation Mechanisms:
Uninhibited C/C composites oxidize preferentially at the fiber-matrix interface due to debonding, exposing fibers to accelerated degradation. Inhibited composites, treated with boron (B) or boron carbide (B₄C), form a protective boron oxide (B₂O₃) layer during oxidation. This coating reduces fiber erosion and maintains dimensional stability, even at 625°C.
Microstructural Analysis:
-
Uninhibited Composites: Exhibit pitted morphologies from catalytic impurities (e.g., residual precursors) accelerating localized oxidation.
-
Inhibited Composites: Show smoother surfaces with B₂O₃-coated fiber bundles, reducing open porosity and weight loss.
5. Innovations and Future Trends
-
Hybrid Matrices: Silicon carbide (C/SiC) coatings enhance oxidation resistance and abrasion tolerance11.
-
Additive Manufacturing: 3D-printed carbon fiber molds reduce production costs and enable rapid prototyping.
-
Nanotechnology: Graphene-enhanced matrices aim to improve thermal conductivity and mechanical strength.
6. Microstructural Study of Oxidized C/C Composites
Recent studies reveal distinct oxidation patterns in inhibited vs. uninhibited C/C composites. Non-inhibited samples display loose, exposed fibers after oxidation, while inhibited variants retain structural coherence due to B₂O₃ coatings. Pitting observed in both types stems from catalytic impurities (e.g., residual metals) rather than porosity or spalling, as impurity-driven reactions dominate at 625°C.
Key Findings:
-
Inhibitors reduce fiber-matrix debonding by 70%, extending component lifespan.
-
Boron oxide layers mitigate CO-induced pore formation, enhancing dimensional stability.
-
Pole figure analysis confirms fiber preservation in inhibited composites after 96% weight loss.
7. Conclusion
Carbon-carbon composites represent a pinnacle of material science, merging lightweight design with unparalleled thermal resilience. From aerospace breakthroughs to cutting-edge automotive solutions, their evolution continues to drive innovation. For tailored C/C products, explore CFCCarbon.com, offering custom fabrications from threaded rods to 3D-woven structures.
Future Directions
Researchers are integrating silicon carbide matrices and graphene additives to enhance oxidative stability and conductivity. Meanwhile, 3D printing promises democratized access to custom C/C solutions.
Call to Action
Discover tailored C/C composites at CFCCarbon.com, your partner in high-performance material solutions.
related news /articles:
Oxidation of inhibited carbon-carbon composite (2)
Mechanisms of protection of C-C composites against catalytic oxidation
Carbon fiber reinforced silicon carbide composites (C/SiC, C/C-SiC)-(1)
Understanding Oxidation Mechanisms in Carbon-Carbon Composites