There are several types of CVI processes which can be used to process carbon-carbon composite:
- Isothermal CVI process:
Typically, a carbon preform is placed within an induction furnace susceptor and heated uniformly to about 1100C, passing the reactant gas over the surface at such a rate as to maintain the surface reaction rate below the diffusion rate. A number of cycles are undertaken, maching away the surface crust prior to the next densification cycle.
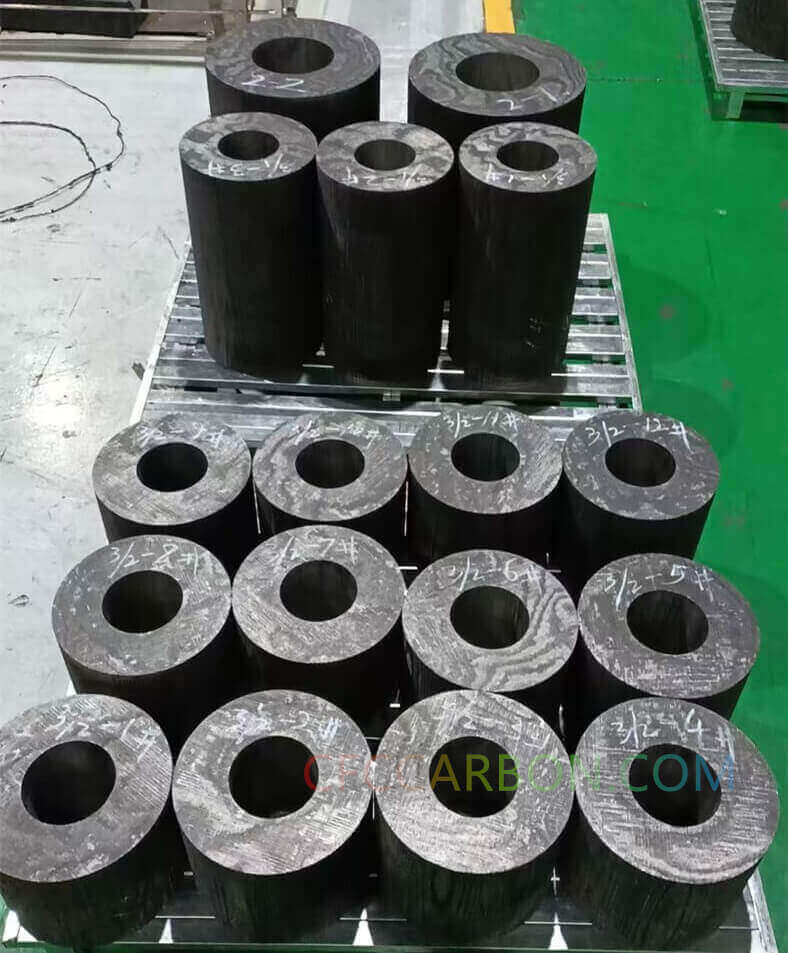
3D carbon fiber composite material manufacturer factory (5)
- Thermal gradient CVI process:
Typically, the carbon preform is positioned in an induction furnace, supported on a mandrel, which acts as a susceptor, and a high gas flow is passed over the preform surface at such a rate that the surface immediately adjacent to the susceptor is about 500C hotter than the exterior surface. The temperature gradient helps prevent surface build-up. To achieve this result, the fiber preform must have a low thermal conductivity and preferably be in a felt form, in order to control the gas flow and ensure sufficient cooling of the external surface of the preform. The technique has been used for rocket motor cones using a filament wound preform applied directly onto a shaped susceptor. Although the deposition rates are faster than the conventional isothermal method and the process is operated at atmospheric pressure, it is unfortunately, a single processing procedure.
- Pressure gradient process:
The fiber preform is sealed in a unit and placed in a heated zone. The sealed design ensures that the gas flow passes through the perform, setting up a pressure gradient and depositing carbon with the evolved H2 being emitted from the outlet end. The deposition rate speeds up with time as the pores become filled and the pressure drops further. The method is not widely used since it is restricted to single item processing and may still require the component to be removed and machined to obtain uniform densification.
- Pulse CVD process:
This technique is a combination of operating the reaction vessel at atmospheric pressure followed by part vacuum to facilitate better penetration of the reactant gases into the pores of the preform. The commercial difficulties of operating this type of process appear to have been overcome by Daewoo Heavy industries to give a lower cost and faster densification procedure.
- Possible new routes:
Continuous efforts are being made to improve the manufacturing process. Some companies investigate an alternative approach for products with improved stiffness, but which would be cheaper. The approach used a pitch matrix and provided added axial stiffness to 345Gpa with reduced production time from months to hours.
Some company have developed a single step impregnation process using a novel resin and a patented process that is reputed to increase the carbon yield and significantly reduce the cost of carbon-carbon composite to about 10-50$/Ib.
In an attempt to make the carbon-carbon production process cheaper, some company have developed a forced flow/thermal gradient process, which is, reputedly, 30% faster and permits a part of 25 mm thickness to be produced in as little as 8h time. The C3H6, C3H8 or CH4 is forced through the preform under pressure at a temperature of 1200C. The ensuing temperature gradient in the material ensures a uniform flow of vapor through the preform. This uniform vapor infiltration enables parts of 10 mm thickness to be produced in 8 h. Parts up to 20mm thickness have been produced using this process.
A Japan company has developed another process wherein a carbon fiber prepreg is coated with graphite precursor powders from coke or pitch. The coating is protected by wrapping with a plastic sleeve during initial weaving or chopping into staple from. The carbon fiber ratio by volume is about 40-60%. The product is then placed in a mold and hot pressed. It is claimed that fewer densification stages are required, but it is not stated what happens to the plastic sleeve, which could remain in situ, with sleeve itself undergoing charring in the subsequent processing. A liquid impregnation increases the densification speed some 50-100 times as compared to the standard process using a gas.
Article keywords /tags: CVI, CVD, carbon-carbon, composite, material, manufacturer, China, processing methods, CFC, C/C,
related links /articles:
Carbon fiber carbon matrix composites manufacturing processes
Carbon fiber reinforced silicon carbide composites (C/SiC, C/C-SiC)-(6)-processing
Modelling of carbon-carbon composite ablation in rocket nozzles (3)