1. What is Carbon-Carbon Composite?
Carbon-carbon (C/C) composites are advanced materials composed of carbon fiber reinforcement embedded in a carbon matrix. This unique combination leverages the high strength and stiffness of carbon fibers alongside the thermal stability and chemical resistance of the carbon
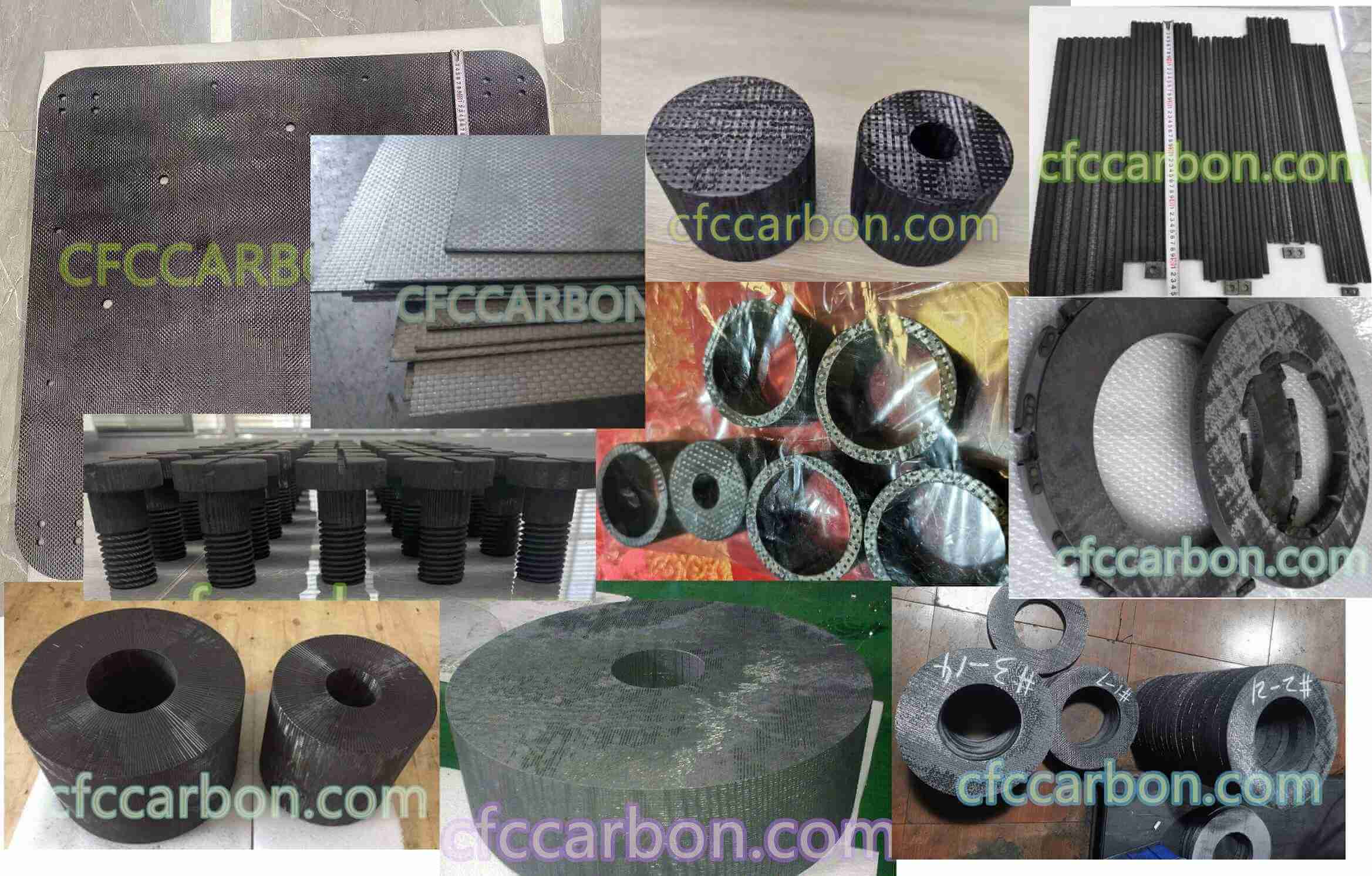
carbon fiber composite material manufacturer in China(1)
matrix18. Unlike traditional metals or polymers, C/C composites retain exceptional mechanical properties even at extreme temperatures (up to 3,315°C), making them indispensable in aerospace, automotive, and medical industries. For example, CFCCARBON LTD, a leading manufacturer in China, produces 2D, 2.5D, 3D, and 4D C/C composites with densities ranging from 1.40 to 1.95 g/cm³ using advanced methods like CVD (Chemical Vapor Deposition) and CVI (Chemical Vapor Infiltration).
2. Method of Analysis for Carbon-Carbon Composites
Production and Manufacturing
C/C composites are fabricated through two primary processes:
-
Chemical Vapor Infiltration (CVI): Hydrocarbon gases (e.g., methane) infiltrate carbon fiber preforms, depositing pyrolytic carbon to densify the matrix. This method ensures uniform porosity and high-temperature stability27.
-
Polymer Impregnation and Pyrolysis (PIP): Thermosetting resins or pitches are impregnated into fiber preforms, followed by carbonization at high temperatures. CFCCARBON LTD employs this technique for cost-effective, high-strength composites9.
Product Classification
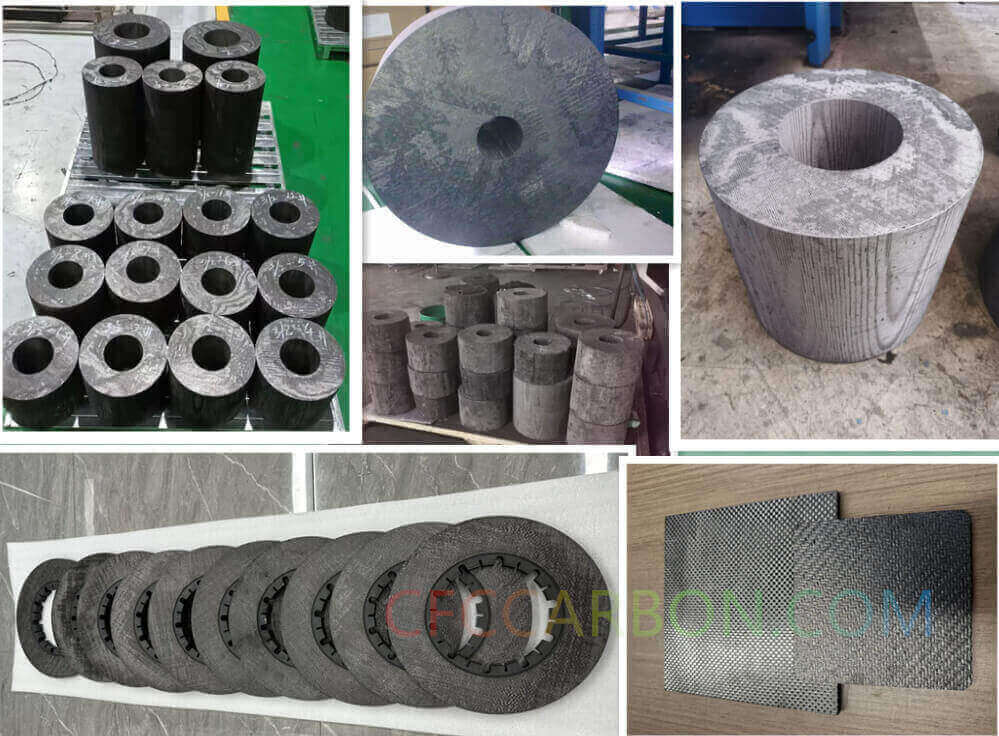
2D 3D 4D 5D carbon fiber composite material manufacturer factory -airplane brake disc plates sheets U L profiles-2D(6)
C/C composites are categorized by fiber architecture:
-
2D/2.5D: Woven fabrics or layered non-woven cloths for moderate mechanical loads (e.g., brake discs).
-
3D/4D: Braided or multidirectional fiber preforms for structural applications requiring isotropic strength (e.g., rocket nozzles)79.
Performance Characteristics
Key properties driving analysis include:
-
Thermal Stability: Retains strength at >2,000°C, ideal for re-entry vehicle heat shields7.
-
Mechanical Strength: Tensile strength up to 167 MPa and fatigue resistance validated through cyclic loading tests9.
-
Biocompatibility: Low CT imaging artifacts and tissue adhesion capabilities enable medical applications (e.g., artificial ribs)9.
Analytical Techniques
-
Microstructural Characterization:
-
SEM/CT Imaging: Evaluates fiber-matrix bonding and void distribution (Fig. 1).
-
Mercury Porosimetry: Measures pore size (>100 µm for tissue ingrowth in biomedical implants).
-
-
Mechanical Testing:
-
Tensile/Flexural Tests: Determines Young’s modulus (~5 GPa for bone-like flexibility).
-
Fatigue Analysis: Validates durability under 1×10⁶ cyclic loads.
-
-
Thermal Analysis:
-
Thermogravimetric Analysis (TGA): Assesses oxidation resistance and ablation performance.
-
3. Advanced Analytical Models for Elastic Constants
The stress-strain relationship in C/C composites is modeled using unit cell homogenization. A stress state is applied to a representative volume element (RVE), and displacements at subcell boundaries are calculated to derive average strains. By transforming coordinates and equating computed stresses to applied stresses, effective elastic constants (e.g., Young’s modulus) are determined. This approach, validated by energy-bound principles, ensures accuracy in predicting anisotropic behaviors.
4. Innovations in C/C Composite Applications
-
Aerospace: Rocket nozzles and thermal protection systems leverage C/C’s low thermal expansion and high conductivity.
-
Medical: 3D-C/C artificial ribs exhibit autogenous bone-like flexibility and biocompatibility, reducing post-surgical complications9.
-
Energy: Wind turbine blades and fusion reactor components benefit from lightweight, fatigue-resistant designs.
5. CFCCARBON LTD’s Expertise
As a top-tier C/C composite manufacturer, CFCCARBON LTD (www.cfccarbon.com) specializes in:
-
Custom Architectures: 2D to 4D preforms tailored for extreme environments.
-
Hybrid Composites: Carbon-ceramic matrices for enhanced wear resistance.
-
Quality Assurance: ISO-certified CVI and CVD processes ensuring density uniformity (±0.05 g/cm³).
6. Future Trends
Research focuses on self-healing coatings to mitigate oxidation and AI-driven finite element analysis (FEA) for rapid prototyping710. These advancements aim to reduce production costs and expand applications in renewable energy and robotics.
Conclusion
Carbon-carbon composites represent the pinnacle of high-performance materials, combining unmatched thermal, mechanical, and chemical properties. Through advanced analytical methods—from microstructure imaging to unit cell modeling—engineers can optimize these composites for next-generation technologies. For cutting-edge C/C solutions, visit CFCCARBON LTD to explore their product portfolio.
related news /articles:
Concluding remarks for CC composite models
CVI CVD Carbon Carbon Composite Material, Manufacturer in China
Microstructure of CVI matrix carbon carbon composite
Microstructure analysis after thermal shock conditions on C/C composites (1)