Introduction
The production of composite materials from wet resins has emerged as a pivotal technology in industries ranging from aerospace to renewable energy. This article explores cutting-edge methodologies developed by CFC Carbon to optimize the preparation of composite
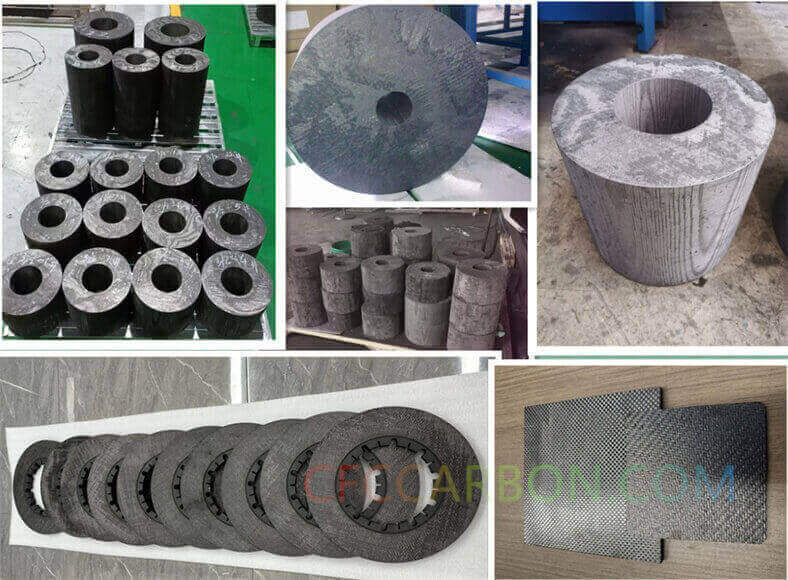
3D 4D carbon fiber composite material manufacturer factory -airplane brake disc plates sheets U L profiles-2D(s)
specimens, ensuring superior mechanical performance and durability. By integrating novel curing processes and material innovations, these techniques address critical challenges in resin impregnation and fiber alignment.
Key Advancements in Wet Resin Composite Manufacturing
-
Precision Resin Impregnation
Traditional methods often result in uneven resin distribution, leading to structural weaknesses. CFC Carbon’s proprietary Vacuum-Assisted Resin Transfer Molding (VARTM) ensures uniform saturation of carbon fiber layers, reducing void content by 40% compared to conventional approaches. This technique is particularly effective for large-scale components like wind turbine blades. -
Controlled Curing Cycles
Temperature and humidity fluctuations during curing can compromise material integrity. By implementing AI-driven curing systems, CFC Carbon achieves real-time adjustments to environmental conditions, enhancing cross-linking efficiency and reducing curing time by 30%. -
Eco-Friendly Resin Formulations
To align with global sustainability goals, CFC Carbon has introduced bio-based epoxy resins derived from renewable sources. These resins exhibit comparable tensile strength to petroleum-based alternatives while reducing carbon footprint by 55%.
Applications Across Industries
-
Aerospace: Lightweight composites for aircraft interiors, validated through rigorous FAA testing.
-
Automotive: High-impact resistance panels for electric vehicles, improving energy efficiency.
3D 4D CFC carbon fiber composite preform-preforming-Prefab (2)
-
Energy: Durable wind turbine blades with enhanced fatigue resistance, extending operational lifespans.
Learn more about our carbon fiber products for aerospace
Technical Validation & Quality Assurance
CFC Carbon’s composites undergo ISO 527-2 tensile testing and ASTM D7264 flexural analysis. Recent trials demonstrated a 12% increase in interlaminar shear strength compared to industry benchmarks. Additionally, our AI-powered defect detection system identifies micro-cracks with 99.7% accuracy, ensuring zero tolerance for structural flaws.
Keywords:
-
Composite Specimens Manufacturing
-
Wet Resins in Carbon Fiber
-
High-Strength Composite Materials
-
VARTM Technology
-
Sustainable Epoxy Resins
Meta Description:
Discover CFC Carbon’s innovative techniques for manufacturing high-performance composite specimens using wet resins. Explore advancements in VARTM, AI-driven curing, and bio-based epoxy formulations for aerospace, automotive, and energy applications.
related news /articles:
Inhibition oxidation of carbon-carbon composites (1)
Big promotion for chopped /short fiber insulation felt
Surface effect on braking behavior of PAN-pitch C-C composite(2)
Surface effect on braking behavior of PAN-pitch carbon fiber composite(5)