Carbon-carbon composite laminates find extensive use in the aerospace industry with applications including brake assemblies and structural panels. Various fabrics woven of graphite yarn typically comprise the reinforcement, but uniaxial tape may be preferred in certain cases. The
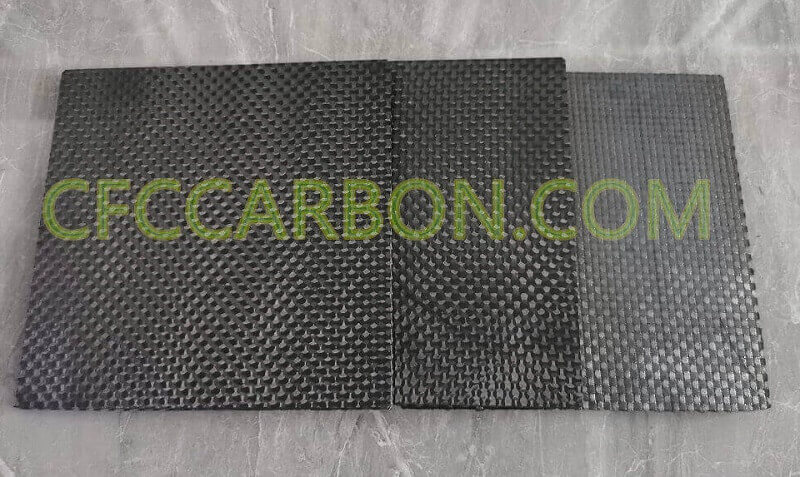
2D carbon fiber composite plate sheet-s
fiber architecture of the laminate is determinded by the weave pattern in the fabric and by the relative orientation of the fabric layers in the stacking sequence.
Fabrics are available in a variety of styles. Fabric styles vary according to basic weave pattern, the type of yarn, yarn spacing, yarn packing efficiency, and the percent of yarn in each direction. The two weave patterns most widely used in CC laminates are plain weave and satin weave.
Uniaxial tape obviously provides the most highly directional properties in a layer, while a balanced plain weave results in the most evenly matched orthotropic distribution of properties within a layer. Satin weaves, which produce smooth fabrics having good drape, are preferred for application in which the layers must conform to topological features such as depressions and bends in the macroscopic shape of the end product.
Laminate structures afford the designer the ability to tailor in-plane properties within the limits of the in situ reinforcement properties.
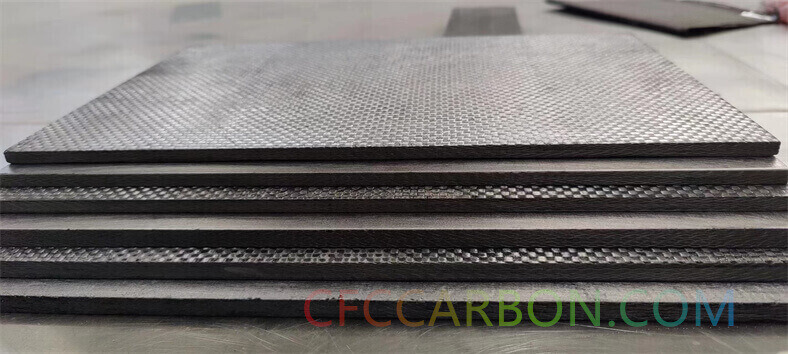
carbon fiber composite plates sheets U L profiles-2D material manufactuer china (5)
Strength in a given direction is determined by the yarn strength and the volume fraction of yarn oriented in that direction. In general, off-axis properties are difficult to predict. The assumption underlying such an approach is one of efficient load transfer between yarns of different orientations. In CC composites, load transfer between fibers is poor, depending on shear modulus. In some instances, depending upon the processing approach used, the designer will assume no load transfer at all. Not surprisingly, CC laminates exhibit low out-of-plane tensile strength and low interlaminar shear strength. Out-of-plane thermal conductivity is lower than in-plane conductivities, since the carbon fibers comprise the high conductivity “heat pipes” in a CC composite. Anisotropy in thermal expansion can be as high as 15:1 depending on the selection of reinforcing fibers.
Laminate structures generally are termed 2D CC even though rotation of fabric plies could be termed multidirectional. For example, the adjacent layers of a certain laminate may be oriented so that the fibers in one layer are directed at 45° to those in the next layer. Thus, a 2D CC structure can have fibers oriented in more than two directions. cfccarbon.com
A 2D CC is suitable for most applications in which interlaminar shear strength and out-of-plane tensile strength are not critical; 2D CC also typically less costly than multidirectionally reinforced CC composite, discussed subsequently. The cost differential originates in weaving-related express, since fabrics typically used to reinforce 2D CC are mass produced to give economies not normally achievable with weaving of individual fiber reinforcements used for 3D preforms. The higher cost of 3D CC composite has inspired alternative fabrication schemes to permit the use of 2D CC composite material in situations in which 3D would otherwise be necessary.
related news /articles:
carbon fiber reinforcement and architecture-woven 3D fabrics
Structural Geometry of CC composite 2D fabrics (1)—Woven fabrics
Rigid carbon/graphite felt board PROMOTION!-20230615(Opens in a new browser tab)