Densification of 2D CC reinforced laminates starts with prepregging of fabric or aligned yarns. Prepregging of woven fabric is readily accomplished on a large-scale basis and is typically automated. For graphite fabric destined for CC composite, the resin impregnant is
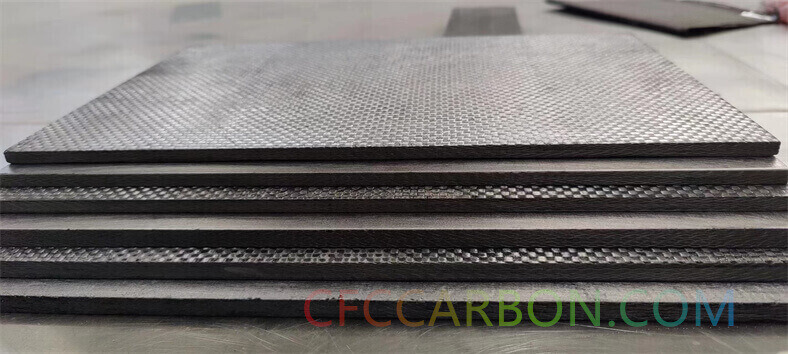
carbon fiber composite plates sheets U L profiles-2D material manufactuer china (5)
commonly a high char (carbon) yielding phenolic, although other resin systems may be used. The process consists essentially of passing the fabric through a controlled resin bath and depositing the desired amount of resin pickup, followed by curing or staging prepregged fabric through thermal treatment.
The process of making laminates from prepreg consists of cutting the prepreg material to the desired size, stacking the layers in a predetermined sequence of orientation, and molding. During molding, pressure is applied to the stack while heat is applied to cure the resin. The time-temperature-pressure requirements for molding depend upon the characteristics of the prepreg. For phenolic resins, molding may be conducted at 160C to 180C under a pressure of 200psi to 300psi for 30 min to 60 min. Molding is followed by a lengthy 24 hr to 100 hr postcure to temperatures higher than those of the molding temperature but well bellow those of the resin decomposition
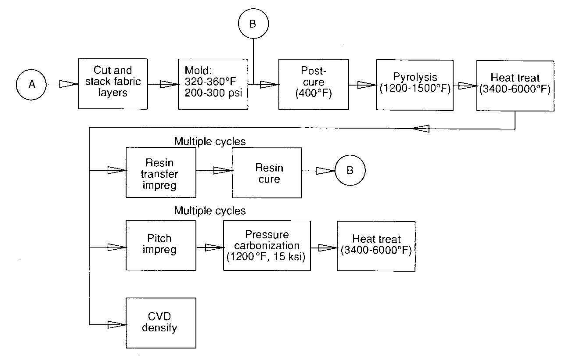
typical 2D CC composite process schematic
temperature. A postcure temperature of 200C is typical for a phenolic resin. Following postcure, the temperature is raised to the 650C to 800C range to pyrolyze the resin, leaving a carbon matrix. Postcuring and pyrolysis are carried out under an inert atmosphere to prevent oxidation. After the resin has been pyrolyzed, the laminate is a CC composite. A stabilization or graphitization heat treatment follows to a temperature that will match or exceed the maximum temperature that the composite will experience in subsequent processing or in use.
The purpose of any subsequent processing would be to reduce porosity and improve mechanical properties. Repeated resin impregnation, pyrolysis, and graphitization; several cycles of pitch impregnation, pyrolysis, and graphitization; CVD densification; or a combination of these, may be done. Pitch-based processing will be described in the context of processing 3D CC composite. Subsequent resin impregnation of 2D CC composite panels typically is done by a resin transfer or submerged impregnation technique whereby the part, by itself or with others, is placed in chamber that is then evacuated to remove gases from the pores of the CC composite. Following this, resin is admitted to the chamber, filling it. A pressure of 50 psi to 100 psi nitrogen is then applied to assist the penetration of the resin into the panel. The excess resin is then drained off, or the panel is removed from the resin bath and a low pressure resin cure is done. Because the fiber volume fraction has been fixed by the initial molding process, higher pressures are not required for this cycle. Postcure, pyrolysis, and graphitization follow the cure cycle. The sequence of impregnation and thermal processing may be repeated a number of times until the target density of the laminate is achieved. Figure 13 illustrates the manufacture of 2D CC composite from prepregged fabric or unidirectional tape.
An alternative densification process, or a final one following a series of resin transfer and stabilization cycles, is chemical vapor deposition or CVD. In this process a carbon-carrying gas such as methane is diffused into the CC substrate and thermally decomposed to deposit carbon onto te interior and exterior surfaces of the CC composite. The process can be economically accomplished by processing a large number of parts in a single cycle. For example, CC brakes are CVD densified. The CVD-densified thin-walled CC tubes have exhibited improved strength and stiffness over otherwise identical tubes densified by resin transfer method. The improvement has been attributed to small pore filling and a degree of interfilament bonding in the CVD-densified tubes.
related news /articles:
Laminates of carbon carbon composite material
Fabric preforms of carbon-carbon composite structures
Structure and properties of textile-reinforced carbon-carbon composite