1. What Are Carbon-Carbon Composites (CCCs) and Coated CCCs?
Carbon-carbon composites (CCCs) are advanced materials composed of carbon fibers embedded in a carbon matrix, combining the high strength and thermal stability of carbon with the fracture resistance of composites. They excel in extreme environments, such as aerospace re-entry systems and rocket nozzles, due to their low thermal expansion, high thermal conductivity, and ability to retain strength above 2000°C in inert atmospheres.
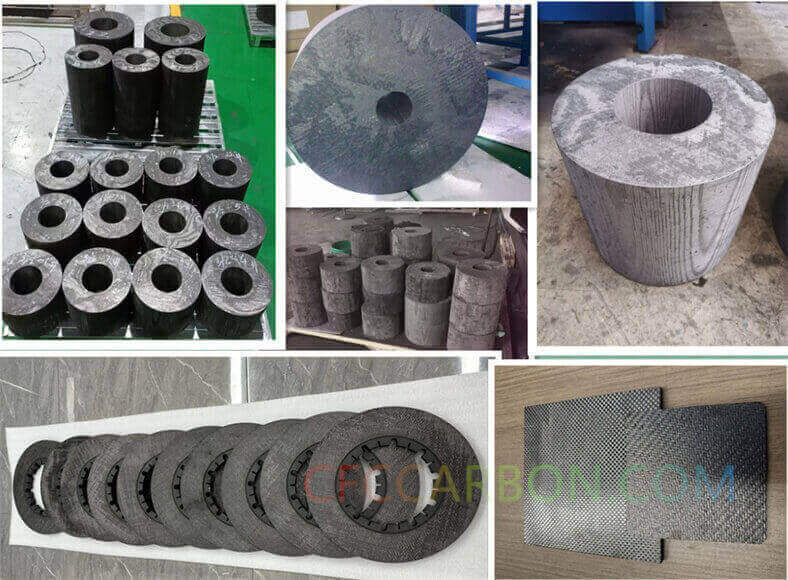
3D 4D carbon fiber composite material manufacturer factory -airplane brake disc plates sheets U L profiles-2D(s)
Coated carbon-carbon composites are CCCs enhanced with protective coatings (e.g., silicon carbide [SiC] or boron carbide [B4C]) to mitigate oxidation at high temperatures. Uncoated CCCs oxidize rapidly above 500°C in air, leading to structural degradation. Coatings form protective oxide layers (e.g., SiO₂ or B₂O₃) that slow oxygen diffusion and extend material lifespan.
2. Article Theme: Production, Classification, Applications, and Performance
Production
CCC manufacturing involves three stages:
-
Layup: Carbon fibers (PAN or pitch-based) are woven into preforms (1D, 2D, or 3D).
-
Pyrolysis: The preform is heated to convert binders (e.g., resins or pitch) into a carbon matrix, leaving voids.
-
Densification: Chemical vapor infiltration (CVI) fills voids with carbon or ceramic matrices, enhancing density and strength.
Classification
-
Fiber Arrangement: Unidirectional, 2D woven, or 3D braided structures.
SiC coating carbon fiber composite material-CC-CFC (3)
-
Coatings: SiC, B4C, or ZrB₂-SiC for oxidation resistance.
Applications
-
Aerospace: Rocket nozzles, re-entry shields (e.g., Space Shuttle leading edges).
-
Industrial: Furnace fixtures, heating elements, and brake systems.
-
Energy: Nuclear reactors and wind turbine components.
Performance Characteristics
-
High-Temperature Stability: Retains strength up to 2400°C in inert environments.
-
Oxidation Vulnerability: Requires coatings for use above 500°C in oxygen-rich conditions.
-
Lightweight: One-tenth the density of metals like tungsten.
Experimental Methods
Samples underwent isothermal oxidation tests at 1100–1400°C. Weight changes were monitored, and microstructural analysis identified coating defects.
Key Findings
-
Coating Performance:
-
SiC coatings exhibited rapid initial weight loss at 1100°C due to crack formation from thermal stress (>35 k.s.i.), allowing oxidant diffusion1.
-
At 1200°C, B4C particles oxidized into B₂O₃, forming a protective layer that reduced weight loss.
-
-
Failure Mechanisms:
-
Crack Propagation: Pre-existing or stress-induced cracks bypassed protective SiO₂ scales, accelerating substrate oxidation1.
-
Boron Oxide Interaction: B₂O₃ altered SiO₂ viscosity, increasing oxygen diffusion rates and destabilizing the protective layer.
-
-
Comparative Analysis:
-
Coated CCCs outperformed uncoated variants, with 50% longer lifespan at 1300°C due to partial SiO₂ scale formation.
-
Future Directions
Researchers emphasize the need for defect-free coating processes and hybrid systems (e.g., ZrB₂-SiC-Cf composites) to achieve parabolic oxidation kinetics, a hallmark of long-term stability.
Conclusion
This study underscores the potential of coated CCCs to revolutionize high-temperature engineering. For more details on CCC solutions, visit CFCCARBON.
related news /articles:
Advanced SiC-Coated Carbon fiber Carbon Composites
Experimental Investigation of Isothermal Oxidation Kinetics in Carbon-Carbon Composites
High-Performance Coatings for Carbon fiber Carbon Composites
Oxidation kinetics and mechanisms of a 2D C/C composite (1)