Natural graphite:
Graphite is found in various parts of the world including Brazil, Canada, China, Korea, United States and occurs in three forms- flake, crystalline and amorphous- with quite divergent compositions and properties (table 2.2). The products are milled to a controlled particle size and find application in various forms of lubricants, electrical brushes, batteries and carbon additives, and can be baked with clay for lead pencils.
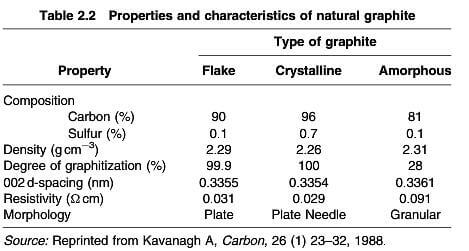
properties and characteristics of natural graphite
Kish graphite:
Kish graphite crystallizes out as flakes in the manufacturing process of cast iron, is a relatively pure form of graphite and is almost identical to natural graphite.
Synthetic graphite:
The manufacture of synthetic graphite basically involves the transition of an organic precursor through a carbonization and graphitization process to yield a char, which may be graphitized with difficulty, or a coke that is a graphitizable carbon (table 2.3)
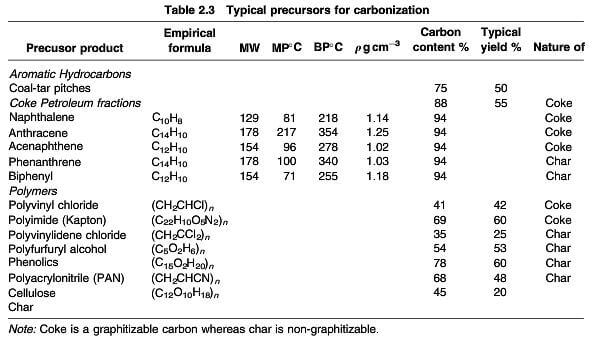
typical precursors for carbonization
Molded graphite is a form of synthetic graphite, manufactured by carbonizing and graphitizing a mixture of carbon filler with an organic binder and is an exceedingly proprietary process with the working details varying from company to company. It is normally based on the Acheson process and a typical industrial process is shown in figure 2.11. A carbon filler such as petroleum coke, which is the almost solid residue left in the process of petroleum refining, is processed further by a series of distillation and cracking stages to yield a heavy residue, which is heated for several days to 400-500C to produce a raw coke. The selection of this raw coke precursor is very important to obtain a good product and needle shaped particles, for example, will enhance the thermal shock resistance. The addition of a “puffing inhibitor” such as iron facilitates the removal of sulfur and is acceptable in a product destined for electrodes. The coke is further purified by heating to about 1200C to remove residual hydrogen and to develop the crystal structure. The product is then ground to particle size dependent on the end use and for a fine graphite, a flour with a particle size<8.4μm is produced and is subsequently mixed with a carefully selected grade of coal tar pitch, which has a low softening point and high carbon content and acts as a binder. Mixing is carried out at 165-170C to lower the viscosity of the coal tar pitch to aid penetration. The mixture is then normally cooled to 125C and extruded through a die to impart a preferred orientation. Alternatively, the mixture can be compression molded in a tungsten carbide die, or to obtain a highly uniform product, albeit an expensive route, it can be isostatically pressed. Sufficient porosity must be retained to permit evolution of volatiles and after shrinkage, the product will have a final porosity of about 25%, which is reduced further by successive pressure impregnations of a binder using a somewhat lower viscosity version of a coal tar pitch to aid penetration into the pores, or alternatively, to use a phenolic resin. Graphitization is then carried out in a resistance, or an induction heated furnace at 2600-3000C. Most of the remaining hydrogen is evolved by 1500C and subsequent heating develops the crystal structure. Cooling is a slow process and takes about two weeks, yielding a product with many faults in the layer planes and some cross linkages. The ash content is about 0.04-0.8% and to obtain a purer product, it is heat treated at 2500C in a halogen atmosphere to remove the impurities as volatile halides, reducing the ash content to about 20ppm.
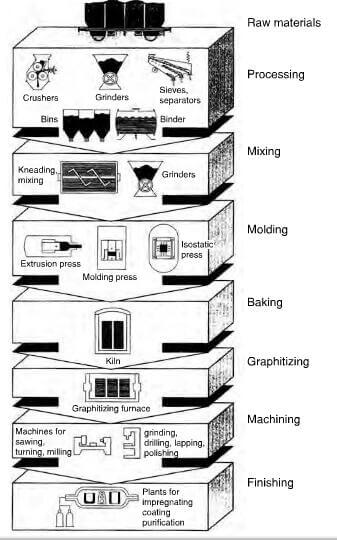
typical manufacturing process for molded graphite.
To consider what structural changes occur in the formation of graphite, a simplistic overview can be taken by following the course of the graphitization of pure hydrocarbon in the absence of an oxidizing atmosphere. On heating to 400C, the hydrocarbon initially darkens, possibly turning black, a process referred to as charring or coking. Condensed ring structures increase in size and progressive dehydrogenation occurs up to 1600C forming a large network of hexagon rings containing macro-aromatic molecules stacked on above another, but with no crystallographic order perpendicular to these networks. From 1600C to 2800C, a graphitizable carbon undergoes progressive graphitization with an increasing three-dimensional order. A non-graphitizing carbon with an interlayer spacing of 0.37 nm is, however, not converted fully to graphite even after heating for many hours at 2000C. The molecular structure of the precursor material affects the type of carbon produced. Graphitizing-carbons, on the other hand, with an initial interlayer spacing of 0.344 nm become quite well aligned at 2200C and at lower temperatures, give a mixture of a graphitic structure with an interlayer spacing of 0.355nm and a turbostratic structure with a spacing of 0.344 nm, normally specifying the mean layer spacing in these instances.
related news /articles:
Introduction of high-temperature coatings on CC composite material
Introduction of carbon-carbon (CC) material–CFCCARBON LTD
Size list and price list of molded graphite | moulded graphite material