Title: Understanding Input Properties of Carbon Fiber Composite Materials: A Guide to Manufacturing, Classification, and Performance
Carbon fiber composite materials (CFRPs) have revolutionized industries from aerospace to automotive due to their exceptional strength-to-weight ratios and durability. However, predicting their final properties requires a deep understanding of input properties—the intrinsic
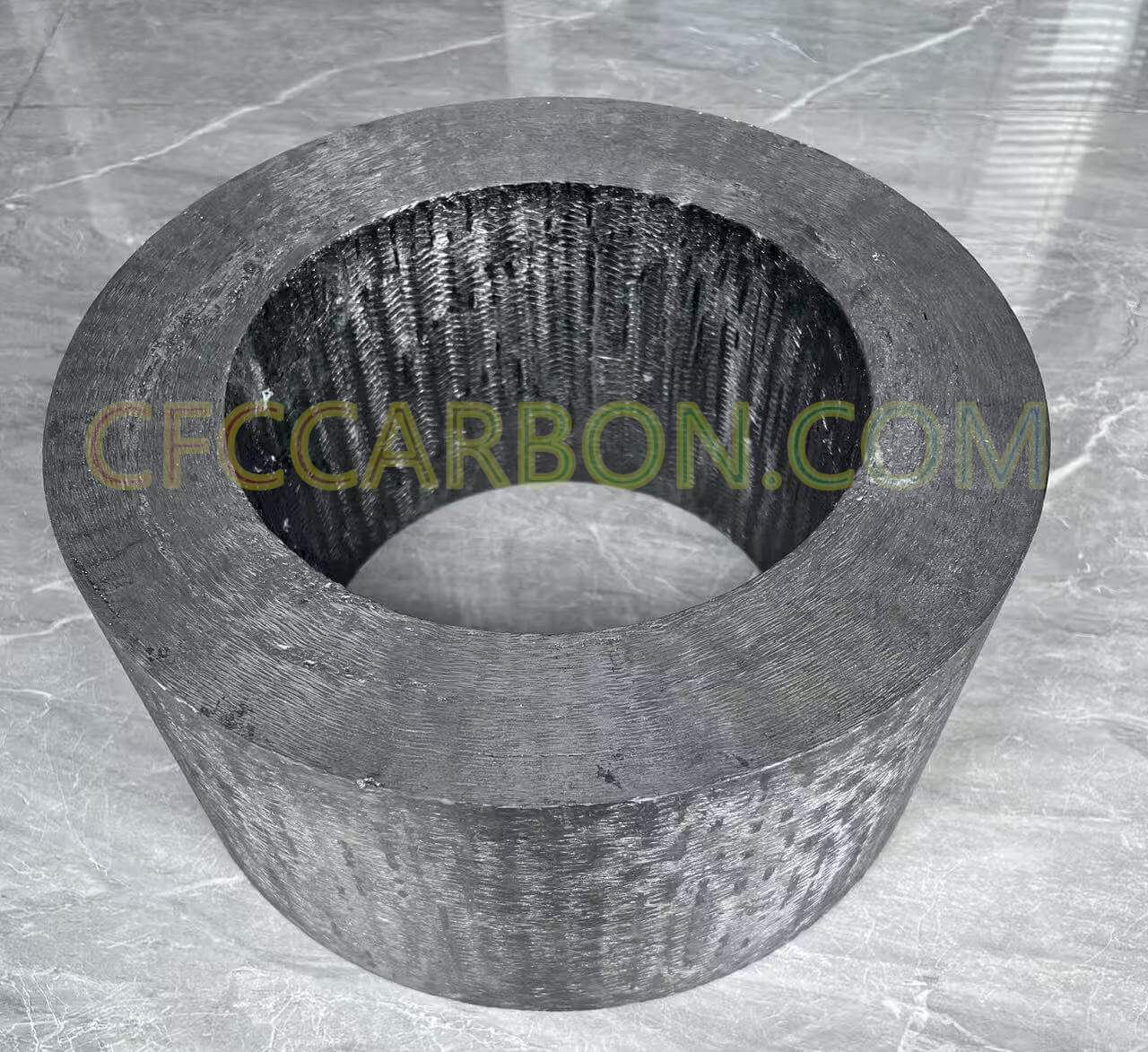
high performance carbon fiber composite mould-2D structure-material manufacturer China
characteristics of raw materials and processing parameters that define the composite’s behavior. This article explores how input properties shape CFRP performance across manufacturing, product classification, and applications, while addressing challenges in modeling and optimization.
1. What Are Input Properties?
Input properties refer to the initial attributes of constituent materials (e.g., carbon fibers, resins, additives) and processing conditions that influence the final composite’s mechanical, thermal, and chemical behavior. These include fiber modulus, resin viscosity, curing temperatures, and alignment techniques. Critically, these properties are not static; they evolve during manufacturing due to high-temperature treatments, chemical reactions, and mechanical stresses112. For instance, graphitization temperatures above 2,200°C alter fiber crystallinity, enhancing stiffness but introducing anisotropic thermal expansion414.
2. Manufacturing Processes and Their Impact on Input Properties
The production of CFRPs involves multiple stages, each modifying input properties:
a. Precursor Selection
-
PAN-Based Fibers: Polyacrylonitrile (PAN) precursors dominate the market, offering high tensile strength (3–7 GPa) and modulus (200–500 GPa). These fibers undergo stabilization, carbonization, and graphitization, where processing temperatures directly affect crystallite alignment and void formation.
3D 4D 5D Hoops, Loop, weaving, stucture, drawing, carbon fiber, carbon, composite, CFC, CC, manufacturer, China, (1)
-
Pitch-Based Fibers: Derived from petroleum or coal tar, these fibers achieve ultra-high modulus (>500 GPa) but require precise thermal control to minimize defects.
b. Fabrication Techniques
-
Wet Layup vs. 3D Printing: Traditional wet layup allows flexibility in resin-fiber ratios but struggles with consistency. In contrast, 3D-printed CFRPs show superior tensile strength due to optimized fiber alignment, though flexural performance may lag.
-
Compression Molding: High-pressure molding reduces voids, enhancing interlaminar shear strength but demanding exacting control over resin flow and fiber orientation.
-
Vacuum Bagging/Autoclave Curing: These methods minimize air bubbles, critical for aerospace components, but require costly equipment and energy-intensive cycles.
Key Consideration: Post-processing steps like graphitization induce microcracks between matrix subcells, reducing shear modulus. Analysts must account for these changes when modeling in situ properties.
3. Product Classification and Input Property Requirements
CFRPs are categorized by fiber type, matrix composition, and end-use demands:
a. Fiber Types
-
High-Strength (HT): Used in automotive chassis (e.g., T300, tensile strength: 3,500 MPa).
-
High-Modulus (HM): Ideal for satellites (e.g., M55J, modulus: 540 GPa).
-
Ultra-High-Modulus (UHM): Reserved for specialized aerospace applications.
b. Matrix Materials
-
Epoxy Resins: Provide strong adhesion but limited thermal stability.
-
PEEK Thermoplastics: Offer superior toughness and temperature resistance, though at higher costs.
4. Application-Specific Input Property Optimization
Aerospace
-
Input Focus: High modulus (≥300 GPa), fatigue resistance, and oxidation stability.
-
Challenge: Galvanic corrosion at metal-CFRP interfaces necessitates insulating coatings.
Automotive
-
Input Focus: Cost-effective PAN fibers (e.g., T700, tensile strength: 4,800 MPa) and rapid manufacturing (e.g., compression molding).
Renewable Energy
-
Input Focus: Pitch-based fibers for wind turbine blades, balancing stiffness and thermal conductivity.
5. Performance Characteristics Shaped by Input Properties
-
Mechanical: Tensile strength and modulus depend on fiber volume fraction (typically 50–60%) and alignment7. For example, cross-ply laminates achieve isotropic stiffness via 0°/90° layering.
-
Thermal: Negative axial CTE in carbon fibers counteracts resin expansion, critical for dimensional stability.
-
Electrical: Anisotropic conductivity (high axial, low transverse) enables EMI shielding but risks short circuits in electronics14.
6. Overcoming Modeling Challenges
Predicting CFRP behavior requires reconciling initial input properties with post-processing changes:
-
Fiber-Matrix Interaction: Pitch impregnation enhances matrix alignment, boosting composite modulus.
-
Multi-Cycle Processing: Repeated thermal cycles induce residual stresses, necessitating final graphitization to stabilize properties.
Conclusion
The interplay of input properties and processing history defines CFRP performance, making material selection and manufacturing precision paramount. As industries push for lighter, stronger composites, advances in 3D printing and hybrid matrices (e.g., carbon nanotube-enhanced resins) promise to mitigate traditional limitations. For tailored solutions, explore CFC Carbon’s product portfolio, offering cutting-edge CFRPs optimized for diverse applications.
related news /articles:
Classification of carbon-carbon composite preforms / structures
Application of Carbon fibers on new structures with cfrp
Introduction of manufacturing of carbon fibers-Pan-based carbon fibers
characteristics and classification of Graphite bipolar plate