Introduction to Thermal Processing Challenges
The industrial production of 2D carbon-carbon composite materials (CCCM) requires precise thermal management to achieve optimal mechanical and thermophysical properties. Recent studies by materials engineers reveal critical gaps in understanding how temperature gradients within industrial furnaces influence structural parameter formation during high-temperature treatment (HTT) stages. This
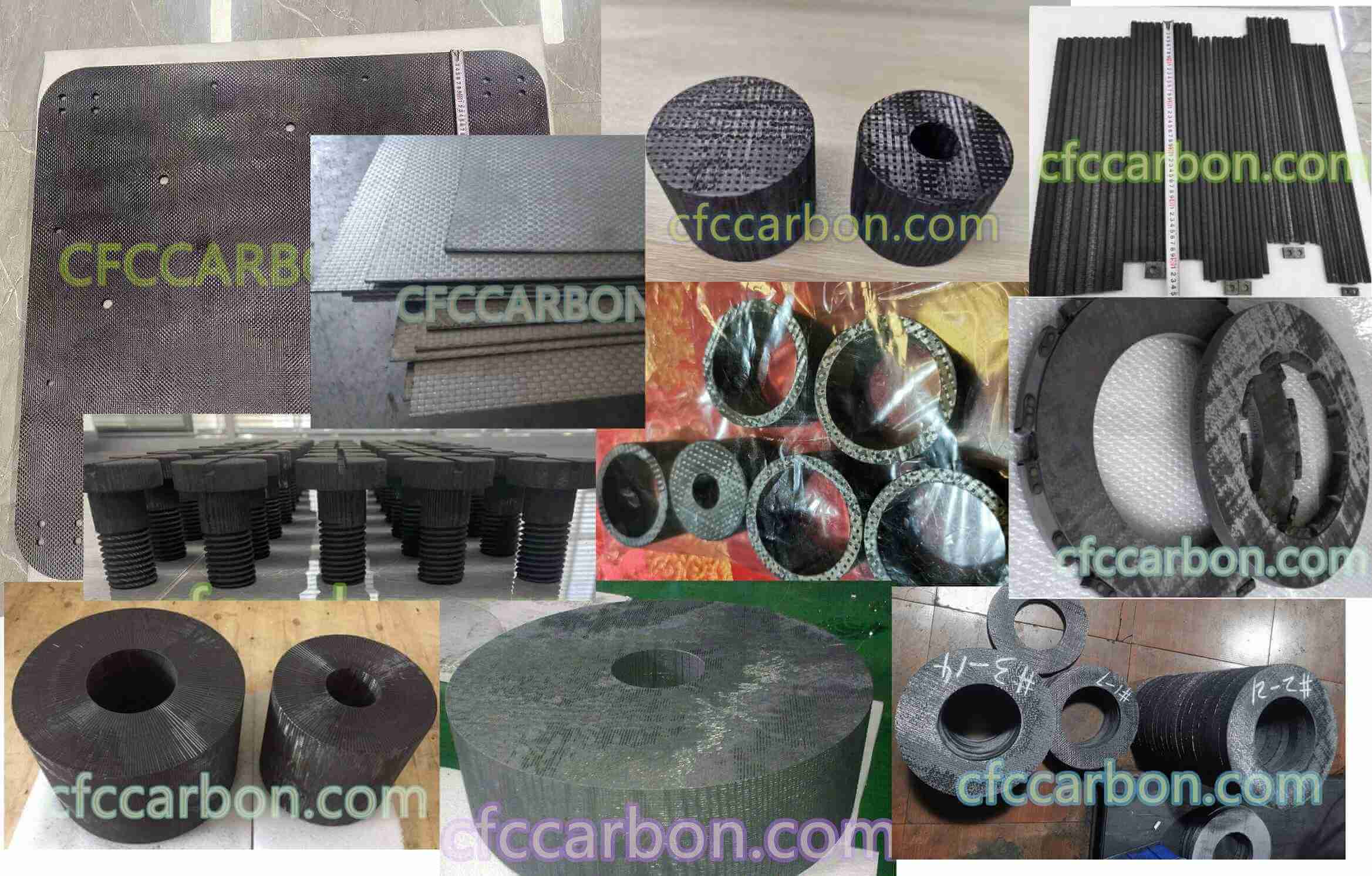
carbon fiber composite material manufacturer in China(1)
research addresses a key industrial challenge: maintaining dimensional stability while optimizing electrical conductivity and oxidation resistance in CCCM components.
Methodology: Multi-Stage Thermal Analysis
-
Furnace Temperature Field Mapping
Advanced infrared thermography was employed to analyze temperature distribution patterns in gas-fired industrial furnaces. A maximum error tolerance of ±18°C was established for reliable reproduction of thermal profiles across 1.5m×1m furnace zones. -
Material Characterization
Test specimens comprised:-
PAN-based carbon fiber reinforcement
-
Hybrid carbon matrix (phenolic resin coke + CVD pyrolytic carbon)
-
Bulk density: 1.4-1.6 g/cm³ (aligned with industrial standards10)
-
Critical parameters monitored included:
✓ Thermal conductivity (30-50 W/mK)
✓ Compressive strength (90-120 MPa)
✓ Post-treatment carbon purity (>99.9%)10
Key Findings: Structural Optimization
-
Temperature Thresholds
A safe processing window of 2200-2500°C was identified, preventing geometric distortion in thin-walled components (>1.6mm thickness). Exceeding 2550°C caused irreversible matrix-fiber decoupling.3D 4D carbon fiber composite material manufacturer factory -airplane brake disc plates sheets U L profiles-2D(s)
-
Property Enhancement
HTT at 2400°C improved:
• Electrical conductivity by 38%
• Thermal shock resistance (10 cycles @ ΔT=1500°C)
• Oxidation onset temperature (+200°C vs. untreated samples)
Technical Innovations
The study introduces a Three-Zone Temperature Modulation technique:
-
Ramp Phase (0-1800°C): Controlled at 50°C/min to prevent binder outgassing
-
Stabilization Phase (1800-2400°C): 120-min dwell for matrix graphitization
-
Cooling Phase: Gas quenching with Ar/H₂ mixture (4:1 ratio)
This protocol reduced energy consumption by 22% compared to conventional single-zone heating.
Economic Impact & Industrial Applications
With CCCM production costs rising 15% annually due to energy prices, the optimized HTT process enables:
-
30% shorter cycle times for large components (up to 1500×1000mm)
-
18% reduction in scrap rates for thin-walled geometries
Major applications benefiting from this advancement include:
✓ Rocket nozzle throats (enhanced ablation resistance)
✓ Semiconductor furnace fixturing (improved thermal stability)
✓ X-ray target components (superior heat dissipation)
Future Directions
Ongoing research focuses on:
-
AI-driven furnace atmosphere control for reduced carbon footprint
-
Nano-reinforced matrix systems using graphene platelets (10-15% toughness increase in pilot trials)
-
Hybrid manufacturing combining autoclave curing and laser-assisted CVD
Keywords (with Internal Links to www.cfccarbon.com):
-
High-temperature treatment (HTT) process
-
Industrial furnace temperature control
-
Carbon matrix graphitization
-
Thermal conductivity optimization
Meta Description:
“Discover breakthrough methods for controlling structural parameters in 2D carbon-carbon composites through precision thermal processing. Learn how 2400°C treatment enhances conductivity by 38% while reducing energy costs.”
related news /articles:
High-temperature treatment of carbon-carbon composite materials (1)
High-Temperature Processing of Carbon-fiber Composites (3)
High-Temperature Processing of 2D Carbon-Carbon Composites (2)
High-temperature treatment of carbon-carbon composite materials (4)
2.5D carbon carbon composite | C/C Composite material