Introduction
Carbon-carbon composites (CCCs) are critical for aerospace and high-temperature applications due to their exceptional thermal stability and mechanical strength. A pivotal stage in their manufacturing is high-temperature treatment (HTT), which removes non-carbon atoms and initiates structural crystallization. This article explores experimental insights into HTT optimization under industrial conditions, focusing on temperature control, furnace design, and challenges in maintaining geometric integrity during graphitization (1,873–2,473 K).
Key Stages of High-Temperature Treatment
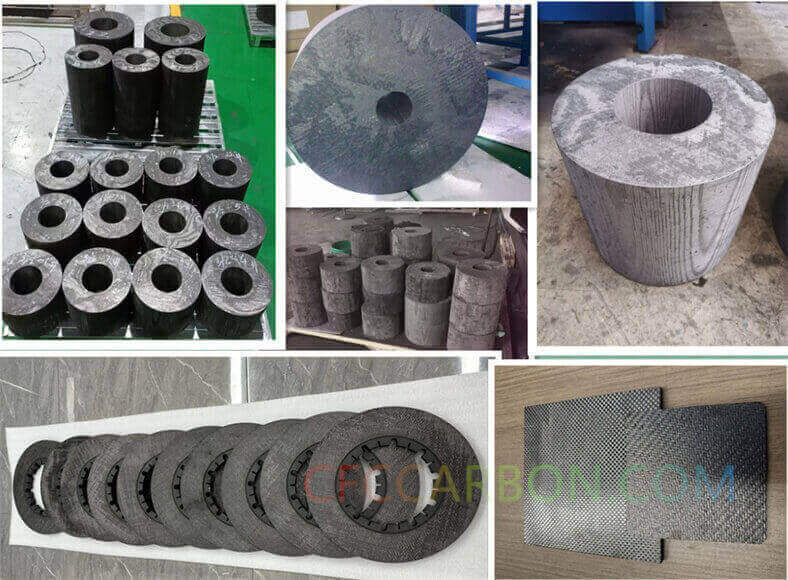
3D 4D carbon fiber composite material manufacturer factory -airplane brake disc plates sheets U L profiles-2D(s)
-
Carbonization (1,173–2,473 K):
-
Removes residual volatiles and non-carbon elements from the matrix.
-
Forms a 2D carbon crystal structure without initiating 3D graphitization.
-
Critical for preserving mechanical properties and minimizing shrinkage-induced deformations.
-
-
Graphitization (>2,473 K):
-
Transforms amorphous carbon into a 3D crystalline graphite structure.
-
Enhances thermal conductivity and oxidation resistance but risks geometric distortion in large components.
-
Industrial Challenges in HTT Process
-
Thermal Gradient Management:
Large-scale components (e.g., conical blanks with 2,250 mm diameter) experience uneven heating in SSHG-type electric furnaces. Heat flux variations arise from radiative zones (direct heater exposure) and conductive zones (inner furnace surfaces), leading to temperature discrepancies up to 50°C across a single blank. -
Energy Efficiency Limitations:
carbon fiber composite material manufacturer in China(1)
-
High heat losses (~450 kW/m²) occur through uninsulated furnace components (e.g., current leads and graphite gas supply systems).
-
Water-cooled metal bodies and graphite fixtures account for ~50% of total energy dissipation.
-
-
Geometric Stability:
Polymorphic transformations during HTT induce microcracks and interfacial stress, necessitating precise control of temperature ramps and dwell times to prevent irreversible warping.
Experimental Setup and Observations
-
Furnace Configuration:
-
Six-level stacking of blanks in a 3,970 mm workspace with graphite heaters and screens.
-
Temperature monitored via optical sensors at multiple heights and radial positions.
-
-
Thermal Behavior:
-
Below 1,800 K: Delayed heating due to low thermal inertia.
-
Above 1,800 K: Rapid temperature convergence driven by T⁴-dependent radiative heat flux.
-
-
Critical Findings:
-
Isothermal soaking at 2,150–2,200°C achieved uniform carbonization but required dynamic adjustments to mitigate edge cooling.
-
Graphite-grade GMZ components demonstrated superior thermal conductivity but limited insulation efficiency.
-
Technological Solutions for Process Optimization
-
Enhanced Thermal Insulation:
-
Replacing lamp black with advanced ceramic-fiber composites reduces sidewall heat losses by 30%.
-
-
Dynamic Temperature Control:
-
Real-time adjustments using AI-driven models to predict thermal gradients, minimizing blank distortion.
-
-
Material Innovations:
-
Functionally graded materials (FGMs) with tailored thermal expansion coefficients improve geometric stability during graphitization.
-
Applications in Aerospace Engineering
-
Reentry Vehicle Components:
CCCs treated at 2,200°C exhibit retained strength at 1,300°C, making them ideal for leading-edge thermal protection systems. -
Rocket Nozzles:
Optimized HTT cycles reduce porosity by 15%, enhancing ablation resistance in hypersonic environments.
Future Directions
-
Machine Learning Integration:
Predictive models for pyrolysis kinetics (e.g., Gaussian Process Regression) could reduce experimental efforts by 40% while optimizing HTT parameters. -
Sustainable Manufacturing:
Recycling joule heat from furnace cooling systems to power auxiliary processes, cutting energy consumption by 25%.
related news /articles:
High-temperature treatment of carbon-carbon composite materials (1)
Thermal stabilization of 2D carbon-carbon composite object geometry (3)
High-temperature treatment of carbon-carbon composite materials (4)
Thermal stabilization of 2D carbon-carbon composite object geometry (2)