the high-purity graphite crucible is one kind of graphite crucibles we produce. see Special Note bellow:
1. Be careful not to give mechanical impact, do not fall from a height or impact.
2. Do not be wet, should be stored in the dry place.
3. Building melting dull, do not make it touch the water.
4. Use the time not to direct the flame at the crucible (spray to the bottom of the crucible), if sprayed to the bottom of the crucible will be
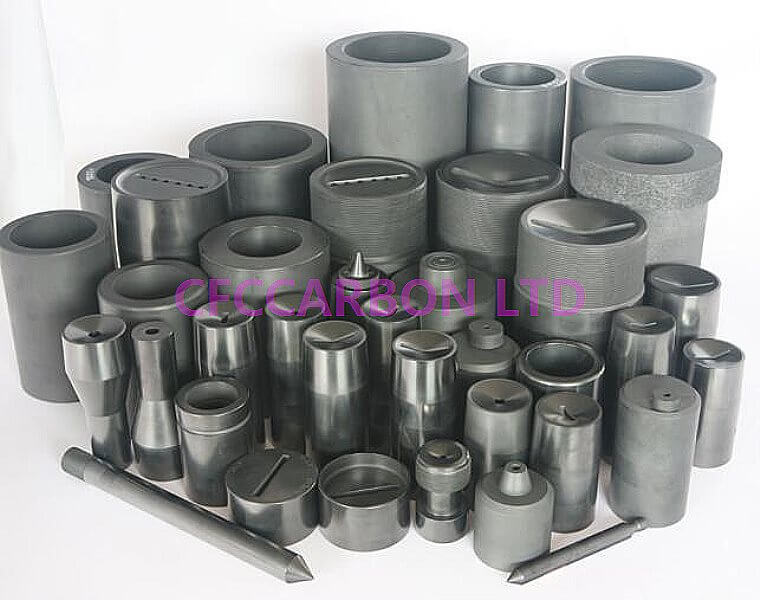
high purity graphite crucibles
significant black marks.
5. After the shutdown of the aluminum, copper material should be removed as far as possible, do not stay within the crucible residue.
6. acidification (slag agent, etc.) the use of appropriate amount to prevent the erosion of the crucible, excessive use will erode the crucible to form a break.
7. Put material into the crucible does not hit, do not use mechanical power.
2. Preservation and transfer:
1. High-purity graphite crucible afraid of water, must be to prevent moisture and water to be.
2. Careful appearance bruises, do not directly put the crucible on the floor, need to be placed on the pallet.
3. Do not roll in the floor horizontal, vertical to the ground when the ground to push the need to pad thick cardboard or rags and other softer things to prevent injury at the bottom of injury.
4. Please pay special attention to the transfer, do not hit the floor or hit.
Third, the crucible device:
1. Crucible base (crucible) and crucible bottom diameter to be the same or larger, the height of the crucible platform to be higher than the ejection port to prevent the fire sprayed into the crucible.
2. With refractory bricks for the crucible should be round refractory bricks, to be flat without bending, do not use half-block or uneven brick material, the best is to use imported graphite crucible is better.
3. Crucible should be placed in melting, the melting of the center point of the above to coke powder, straw ash or fire-resistant cotton pad for the crucible and crucible to prevent the stick, crucible put up, the need to melt in the center, and required Level (the best with the level of scale).
4. Crucible and the size of the furnace to match the crucible and fused wall spacing should be appropriate, at least 40mm or more.
5. A mouth crucible furnace installed, the crucible mouth and firebrick below the touch gap should be reserved for about 30-50MM of the gap, and under the pad can not be anything, mouth and wall with fire-resistant cotton smooth. Furnace wall to be fixed refractory bricks (three points) and the crucible to be padded with a thickness of about 3mm of corrugated cardboard as the heated after the thermal expansion of space.
Fourth, preheating drying:
1. The use of the first 4-5 hours before the crucible to move in the oil furnace preheating, the appearance of the dehulled crucible to help.
2. The new crucible before use in the crucible placed in the charcoal or wood burning four hours or so, on the crucible of the dehumidification have assistance.
3. New crucible furnace heating preheat time is as follows:
0 ℃ – 200 ℃ slow heating 4H
Oil 0 ℃ – 300 ℃ slow heating 1H electric 200 ℃ – 300 ℃ slow heating 4H
Furnace 300 ℃ – 800 ℃ slow heating 4H furnace 300 ℃ – 400 ℃ slow heating 4H
400 ℃ – 600 ℃ rapid warming adhere to 2H
4. After shutdown, the preheating time is as follows:
Oil furnace and electric stove:
0 & lt; 0 & gt; C to 300 & lt; 0 & gt; C
300 ℃ – 600 ℃ slow heating 4H
600 ℃ – rapid heating to the degree of demand
A: electric stove: the best time to continue to heat insulation, the temperature set at about 600 ℃; if not heat, soup should be scooped out as much as possible, not to stay in the crucible too much in case of power outages need to quickly remove the material.
B. Oil stove: After stopping the soup, try to scoop clean the stove lid and furnace vents to be covered, keep the furnace temperature to prevent the crucible damp.
5. Feeding:
High purity graphite crucible top furnace use, the first plus scrap (small material) and then block material, and the need to clamp tightly into the crucible, not too full to prevent a crowded crush crucible.
A. Oil furnace: 300 ℃ in the future to feed;
B. Electric furnace:
A. 200 ℃ – 300 ℃ began to add a small material, 400 ℃ gradually increase in the future block material, such as production continued to feed when not added to a fixed orientation to prevent the formation of oral oxidation.
B. Dedicated to the insulation furnace, after shutdown to be preheated to 500 ℃ before pouring aluminum soup.
Fifth, the use of the Note:
1. Feeding should be gently, and can not be put into the crucible, to prevent crushing crucible.
2. Crucible 24 hours will continue to use life will be longer, to stop the operation of the melting pot in the crucible to be clear, to prevent the molten pool re-ignition heating will produce expansion of the life of the crucible and even break the crucible burst.
3. Melting Aid: Aluminum alloy melt additives (FLLUX) and copper alloy borax, please use a small amount due to large amounts of corrosion will crucible wall. Auxiliaries need to be dissolved in aluminum into the soup noodles minimum 8 minutes full, light into the crucible medium speed stirring, to prevent adhesion to the crucible wall and then pits the crucible.
* Aluminum alloy additives such as containing (NA) ingredients more than 10%, the need for special raw materials of the crucible.
4. In the daily work with the end of the crucible or red, please cut down the clean-up clean crucible wall attached to the metal, to prevent excessive residue affect the heat transfer and add dissolved time, the formation of thermal expansion and burst the crucible.
5. Advice in the crucible melting aluminum alloy for about two months (melting copper alloy per week), that is, hanging out to see whether there is an abnormal appearance, can also clean the furnace, the same into the crucible steering, this operation is conducive to extending high-purity graphite crucible Service life.
related news /article:
EDM graphite and its application–CFCCARBON LTD
PG sheet-pyrolytic graphite plate disc crucible pipe tube
Silicon carbide graphite crucible (3)-SiC graphite crucible