For a traditional cast iron brake disc, when it is tested against typical organic or sintered pads, s friction transfer layer, typically composed of a dense mixture of iron oxides and compounds such as lubricants, fillers and abrasives that originated from pads, is fairly easily developed with a strong bond through fusing with iron matrix. Therefore, the focus of a cast iron brake has always been on the friction layer
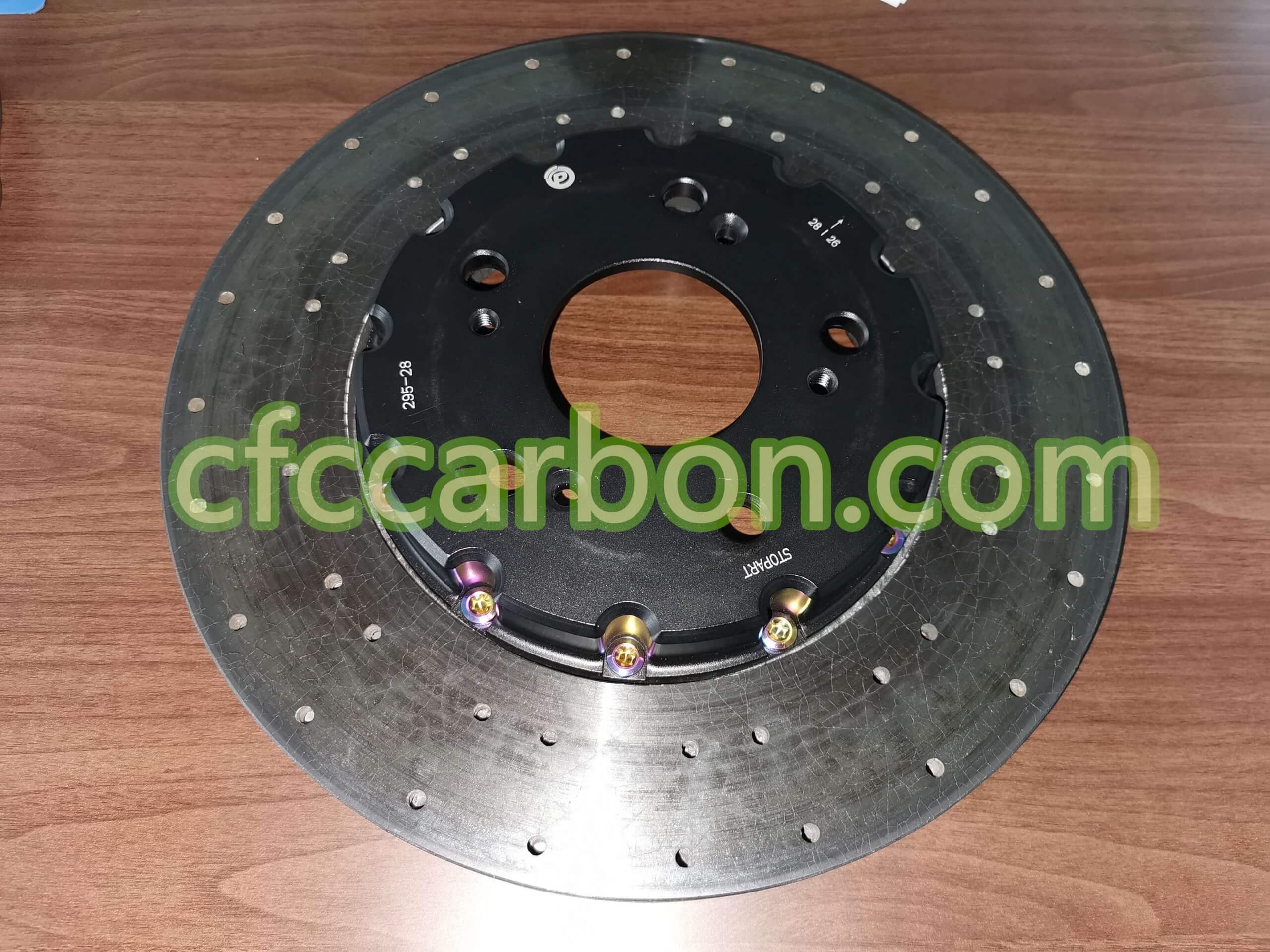
carbon ceramic-racing car brake disc-CSiC-CFC-CC
development on the contact surface of a pad, because it is the friction surface of a pad that largely dictates the bedding time required for a cast iron brake, as well as the level of friction coefficient after bedding. For a carbon ceramic brake, however, this is not the case, as demonstrated already, and brake disc could take longer time than pad to complete the bedding. Therefore, attention on friction surface of the disc is necessary.
On the other hand, the weak bond of a friction transfer layer on surface of a carbon ceramic disc likely makes the layer very susceptible to solvents, like water, when they are involved in friction contact regions. When friction transfer layer becomes a key factor in defining the friction performance of a brake, the loss of a friction transfer layer might bring significant change of friction coefficient of a carbon ceramic composite brake. By now, all studies on carbon ceramic composite brakes are conducted in ambient air atmosphere, their friction behavior in wet is remained as unknown at least in literature, if not in industry. We will therefore examine its friction behaviour when a carbon ceramics brake is tested in a wet environment.
However, friction performance in solvent for a cast iron brake does not seem to be a main concern. For the mostly used testing standard, SAE J2522, testing in wet environment is not even included in the suggested testing programme. However, recent studies demonstrated that
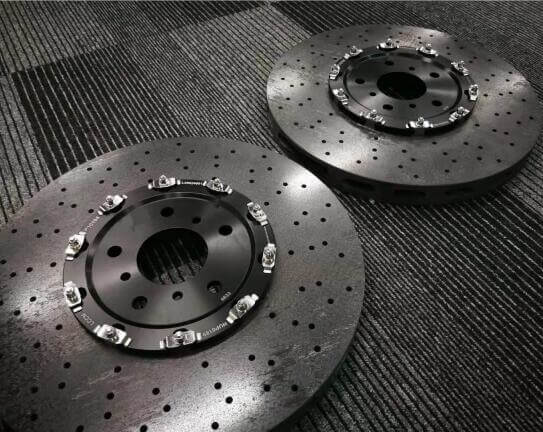
carbon ceramic composite (C-SiC) brakes for racing car-3
friction coefficient of a cast iron brake could fall in wet environment, and the fall was enhanced by the increase of sliding speed or the reduction of braking pressure. The underpinned mechanism for the fall was believed to be associated to (a) the loss of friction transfer layer from friction surfaces of disc and pads; (b) the formation of water film that can reinforce the hydrodynamic process of contact surfaces; (c) the cooling of the friction surfaces that might reduce friction contact region. Therefore, it is interesting to know how the friction coefficient of a carbon ceramic composite brake is governed when it is operated in a wet environment.
Experimental procedures:
2.1 Materials for brakes: Two commercial C/SiC composites were chosen to be brake discs on the basis that they provide significantly different contents of SiC/Si and Cf/C constituents. Information on their microstructure was analyzed, and is reported in Results and discussion section. For a brake including a composite disc with a high fraction of SiC/Si, we hereafter called Brake-H, and the one with a low friction called Brake-L. Grade BS EN 1561 grey cast iron was chosen to be manufactured into a brake disc, and then tested under same conditions as for the composite discs.
A commercial brake pad was selected, and machined into a pad fitting to the testing set up. Same pad was tested against all ceramic composite and cast iron discs. Due to commercial reasons, it is unlikely to know the details of chemicals in this pad. However, its main chemical elements and microstructure were analysed, and reported in section 3.
related news /articles:
Friction performance of C/SiC brakes in different environment (7)