1. Introduction to Isostatic Pressing Technology
Isostatic pressing represents a groundbreaking advancement over conventional hot extrusion and molding methods. Utilizing liquid or gaseous media (e.g., oil, emulsions, argon, nitrogen), this technology applies uniform omnidirectional pressure to raw powders or pre-formed compacts encapsulated within flexible molds (rubber or aluminum skins). By eliminating directional stress gradients, it enables the
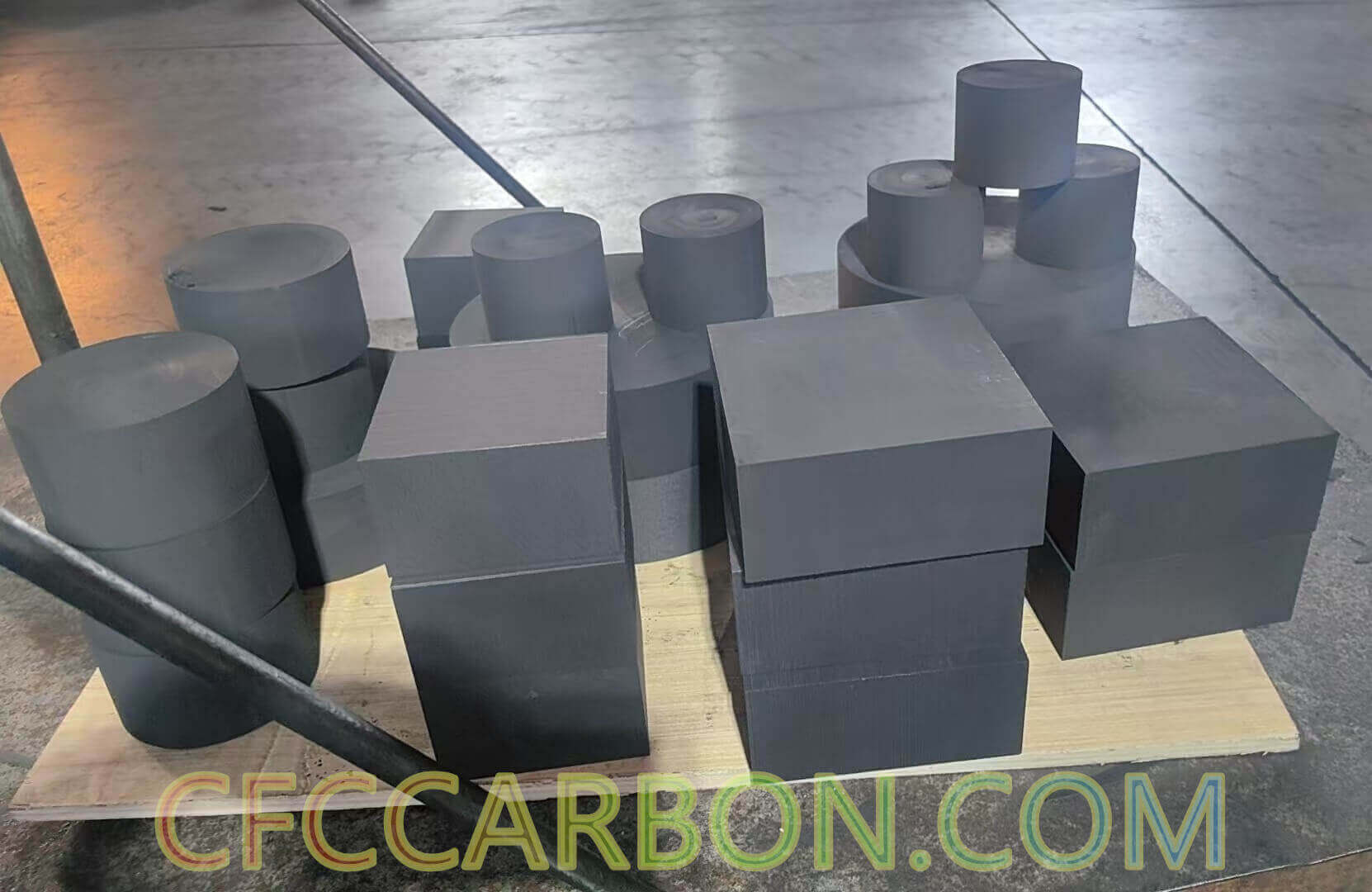
isostatic graphite rods blocks plates material manufacturer factory China
production of carbon graphite materials with unparalleled density homogeneity and structural stability, particularly for complex geometries and large-scale industrial applications.
2. Classification of Isostatic Pressing Machines
Modern isostatic pressing systems are classified by operational temperature:
-
Cold Isostatic Pressing (CIP): Room-temperature processing for ceramics and powder metallurgy.
-
Warm Isostatic Pressing (WIP): Moderate temperatures (80–100°C) balancing energy efficiency and material integrity.
-
Hot Isostatic Pressing (HIP): High-temperature (>1,000°C) densification for aerospace alloys and nuclear-grade graphite.
Innovations like steel wire pre-stressed cylinders now support pressures up to 1,050 MPa and diameters exceeding 2,000 mm (Explore: CFCCARBON HIP Systems).
3. Global Historical Development
Originating in Sweden (1939), isostatic pressing initially served powder metallurgy and ceramics. By the 1960s, it revolutionized carbon graphite manufacturing. Early limitations – 200 MPa pressure and 200 mm cylinder diameters – gave way to today’s mega-scale solutions.
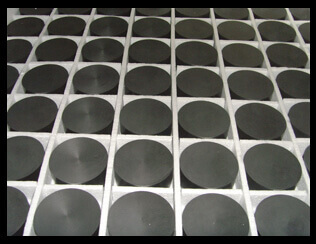
high purity isostatic graphite rods blocks rounds blocks material manufacturer factory China (7)
CFCCARBON Ltd., for instance, now produces 1,500 × 2,000 mm isostatic graphite blocks, with plans for 2,000 mm diameter units by 2025.
4. China’s Technological Progress
China’s journey began in the 1970s with 200 MPa CIP machines. By the 1980s, domestic production scaled to 500–800 mm cylinders. Current milestones include:
-
Cylinder Size: 1,500 mm diameter HIP machines.
-
Annual Capacity: 6,000 tons at CFCCARBON’s facility, including Φ500 × 600 mm graphite.
-
Dual-Function Systems: HIP machines now integrate asphalt impregnation, sealing products and bitumen in metal containers under heated gas compression to achieve zero-porosity carbonization (CFCCARBON Impregnation Technology).
5. Industrial Applications and Advantages
Critical sectors leveraging isostatic pressing include:
-
Semiconductors: Ultra-pure graphite crucibles for monocrystalline silicon.
-
Nuclear Power: Isotropic graphite neutron moderators.
-
Aerospace: C/C composites for rocket nozzles.
Industry data shows 40% fewer defects and 30% longer service life versus traditional methods, as reported by CFCCARBON’s clients.
6. Future Trends and Challenges
Projected to grow at 8.5% CAGR (2023–2030), the market faces evolving demands:
-
Automation: AI-optimized pressure profiling.
-
Eco-Efficiency: Closed-loop hydraulic media recycling.
-
Material Science: Graphene-enhanced composites.
China’s roadmap targets 90% HIP component localization by 2030, overcoming high-pressure seal import dependencies.
7. Conclusion
From Swedish innovation to China’s manufacturing leadership, isostatic pressing underpins modern high-tech industries. CFCCARBON Ltd. epitomizes this progress through its high-purity graphite solutions and commitment to “reliable quality, best service.” As material science advances, this technology will continue driving the frontiers of performance-critical applications worldwide.
related news /articles:
Isostatic Pressing graphite rods Technology Development
Characteristics of Isostatic Graphite rods
Characteristics of Isostatic Graphite material