Title: Understanding Oxidation Mechanisms in Aircraft Carbon-Carbon Composites: A Kinetic Study
Aircraft Brake Oxidation Challenges
Carbon-carbon composite (C-C) discs in commercial aircraft face extreme thermal stresses during operation, reaching temperatures of approximately 1,000°C during routine landings and spiking to 1,400°C in emergency scenarios like aborted takeoffs. Recent studies, reveal that thermal oxidation accounts for over 60% of total material degradation in these components – a significantly greater factor than
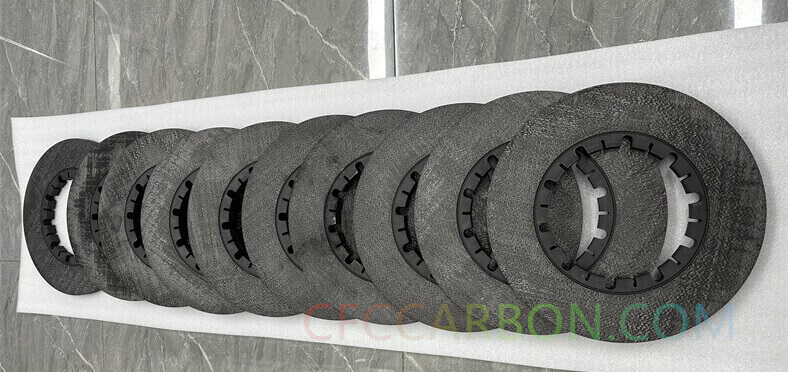
airplane brake disc-aircraft carbon fiber composite material manufacturer- (2)
mechanical wear from friction. This oxidative breakdown not only erodes the carbon matrix and fibers but critically weakens fiber-matrix interfaces, compromising structural integrity.
Temperature Thresholds and Kinetic Behavior
Like conventional graphite, C-C composites initiate oxidation at temperatures as low as 400°C, with degradation rates escalating exponentially as heat intensifies. While historical research has extensively documented oxidation kinetics in coal and coke systems, the aerospace industry’s growing reliance on C-C composites has spurred new investigations into their unique degradation patterns. As noted in a recent publication by CFCCarbon (www.cfccarbon.com), material microstructure variations present significant challenges in developing universal kinetic models for these engineered composites.
Key Oxidation Reactions
The primary oxidation pathways generate carbon monoxide and dioxide through:
Water vapor introduces secondary reactions at elevated temperatures:
3. (≥667°C)
4. (≥623°C)
Moisture’s Dual Role
While most aircraft braking occurs in dry conditions, adsorbed moisture within composite microstructures remains a critical concern.
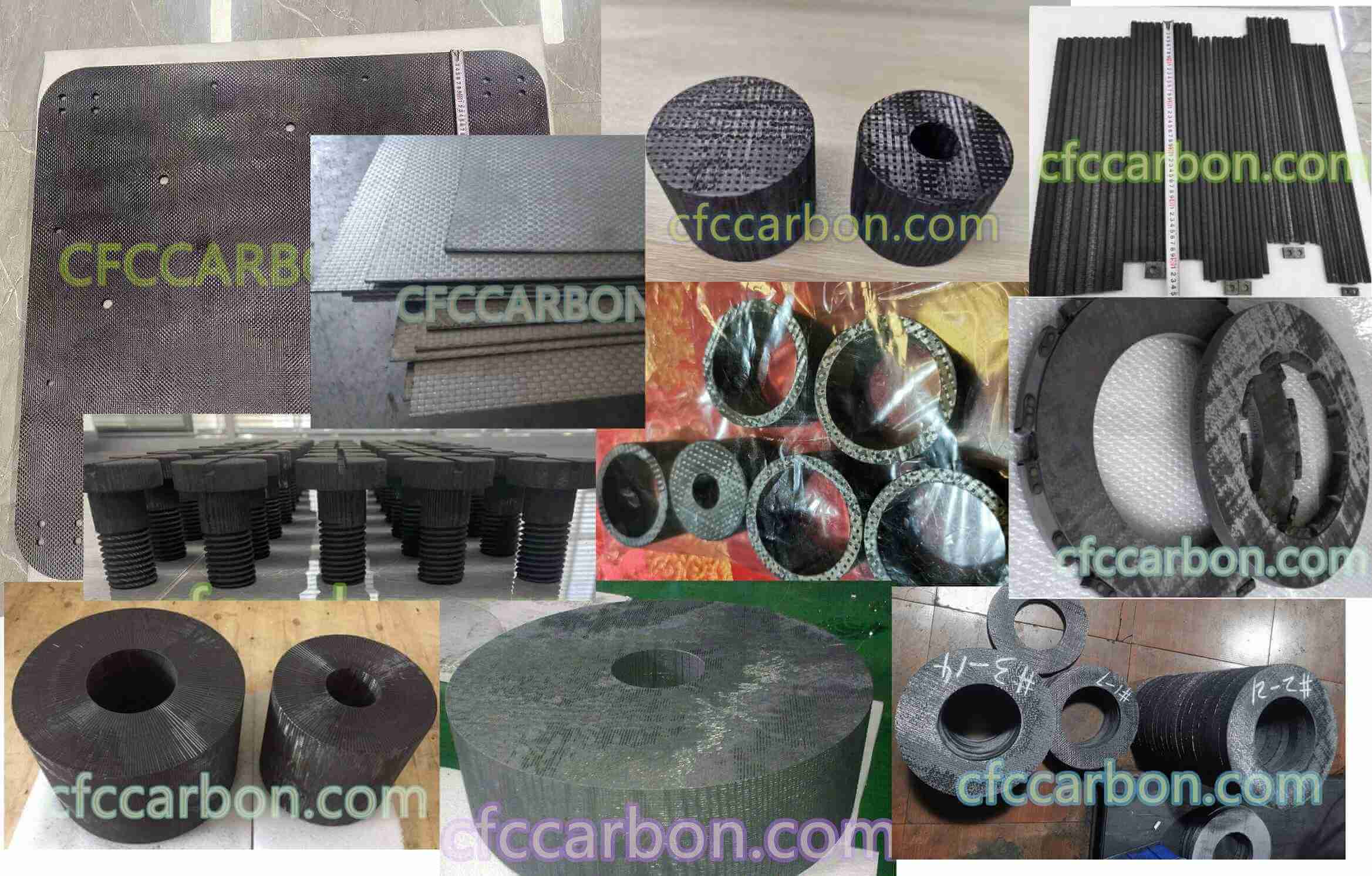
carbon fiber composite material manufacturer in China(1)
Research by Duvivier et al. demonstrates that even 5% ambient humidity can accelerate oxidation kinetics tenfold at 500-650°C, particularly in catalyst-containing systems. This aligns with Blanco’s findings that water enhances active site polarity, facilitating carbon breakdown – a phenomenon less relevant to steam-free operational environments.
Industrial Implications and Research Frontiers
The aviation sector’s push toward higher-performance brakes has intensified focus on oxidation mitigation strategies. Current studies explore:
-
Microstructural engineering to delay oxidation onset
-
Protective coatings resistant to thermal cycling
-
Catalytic inhibitors targeting reaction pathways
As emphasized in CFCCarbon’s technical briefs, future applications in hypersonic systems and reusable spacecraft will demand deeper understanding of these kinetics. The complex interplay between manufacturing variables (fiber orientation, density gradients) and oxidation resistance remains a key research priority.
Conclusion
With C-C composites playing increasingly critical roles in aerospace and emerging technologies, resolving oxidation kinetics challenges represents both a materials science imperative and an engineering necessity. Ongoing research continues to refine predictive models while developing next-generation composites capable of withstanding extreme thermal-chemical environments.
related news /articles:
Oxidation kinetics and mechanisms of a 2D C/C composite (1)
Research and development direction for CC composite
Oxidation kinetics and mechanisms of a 2D C/C composite (3)