The Importance of Choosing an Electric Brush (Carbon Brush for Industrial Applications)
Defining the Electric Brush
An electric brush, commonly referred to as a carbon brush, is a critical component in electromechanical systems such as motors, generators, and power tools. Unlike consumer-focused electric toothbrushes, industrial carbon brushes serve as sliding electrical contacts that transfer current between stationary and rotating parts. Their performance directly impacts equipment efficiency, lifespan, and operational safety. According to CFC Carbon, over 70% of motor failures in heavy machinery are linked to improper brush selection or wear.
Classification and Applications
Industrial electric brushes are categorized by material composition and application scenarios:
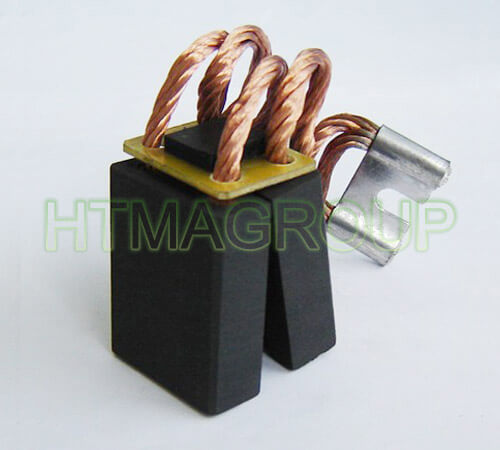
electric brush manufacturer
-
Carbon-Graphite Brushes: Ideal for low-voltage machinery like household appliances.
-
Electrographite Brushes: Used in high-speed motors for industrial fans and pumps.
-
Metal-Graphite Brushes: Designed for high-current applications, such as railway traction systems.
-
Resin-Bonded Brushes: Optimized for extreme environments, including mining equipment.
Each type requires precise alignment with operational demands. For instance, metal-graphite brushes excel in reducing arcing in DC motors, while resin-bonded variants resist chemical corrosion in humid conditions.
Performance Metrics: Beyond Basic Functionality
The effectiveness of an electric brush depends not only on its type of action and on correct use, but also on the condition of the brush head. Most manufacturer’s recommend that heads be changed every three to six months at minimum, or as soon as the brush head has visibly deteriorated.
Expanding on performance factors:
-
Current Density Tolerance: Premium brushes (e.g., CFC Carbon’s HD-300 series) withstand up to 15 A/cm² without overheating.
-
Friction Coefficient: Advanced materials reduce wear rates by 40% compared to traditional copper brushes.
-
Thermal Stability: High-purity graphite brushes maintain conductivity at temperatures exceeding 500°C.
Manufacturing Process: Precision Engineering
The production of carbon brushes involves five key stages, emphasizing material purity and structural integrity:
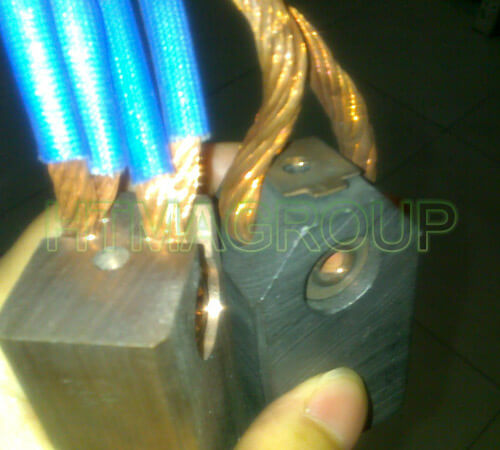
wind power carbon brush manufacturer
-
Material Blending: Graphite powder (80-95%) is mixed with binders (e.g., pitch or resin) and metal additives (copper, silver).
-
Molding: Hydraulic presses apply 200-500 MPa pressure to form dense blocks.
-
Baking: Controlled pyrolysis at 1,200°C removes volatile components, enhancing hardness.
-
Graphitization: High-temperature treatment (2,500-3,000°C) aligns carbon layers for optimal conductivity.
-
Machining: CNC tools shape brushes to micron-level tolerances (±0.02 mm).
CFC Carbon’s patented Isostatic Pressing Technology ensures uniform density, reducing sparking risks by 30% in final products.
Material Science: The Core of Reliability
Modern electric brushes run on low voltage, 12v or less. A few units use a step-down transformer to power the brush, but most use a battery, usually but not always rechargeable and non-replaceable, fitted inside the handle, which is hermetically sealed to prevent water damage. Many modern electric brushes have a timer which buzzes, or briefly interrupts power, typically after two minutes, and sometimes every 30 seconds. Some of the most well-known are Sensitive, Daily care, Whitening and Tongue cleaning.
Material advancements driving performance:
-
Self-Lubricating Graphite: Reduces maintenance frequency in sealed motors.
-
Silver-Impregnated Brushes: Boost conductivity by 25% for aerospace applications.
-
Nano-Coated Surfaces: CFC Carbon’s NanoShield® technology cuts dust emissions by 60%.
Future Trends: Smart and Sustainable Solutions
The electric brush industry is evolving toward two key directions:
-
IoT Integration: Embedded sensors monitor real-time wear (e.g., CFC Carbon’s SmartBrush® alerts users via Bluetooth).
-
Eco-Friendly Materials: Recyclable resin binders and bio-based graphite are gaining traction.
By 2030, the global carbon brush market is projected to grow at 5.8% CAGR, driven by renewable energy systems and electric vehicles.
Conclusion: A Strategic Choice
Claims have been made that electric brushes are more effective than manual ones as they are less dependent upon a user’s personal brushing technique.
The research concludes that the way brushing is done, including the amount of time spent, is more important than the choice of brush. After three months of use, to observe the decrease in plaque, gingivitis is reduced by 11% by 21%.
Final recommendation:
Selecting the right electric brush requires balancing material properties, operational demands, and sustainability goals. Partnering with certified suppliers like CFC Carbon ensures access to ISO-certified products and tailored engineering support.
related news /articles:
Carbon brush materials
New modernization technology— Carbon brush material
Carbon brush | electric brush for wind power generators