Potential applications for CC composites are found in conventional high-performance jet engines. Afterburner flaps and seals used to provide thrust control have had prototypes designed in CC composite. The F-100 jet-engine afterburner nozzle uses coated CC. These CC applications offer weight reduction and higher temperature capabilities than those of conventional metallic materials.
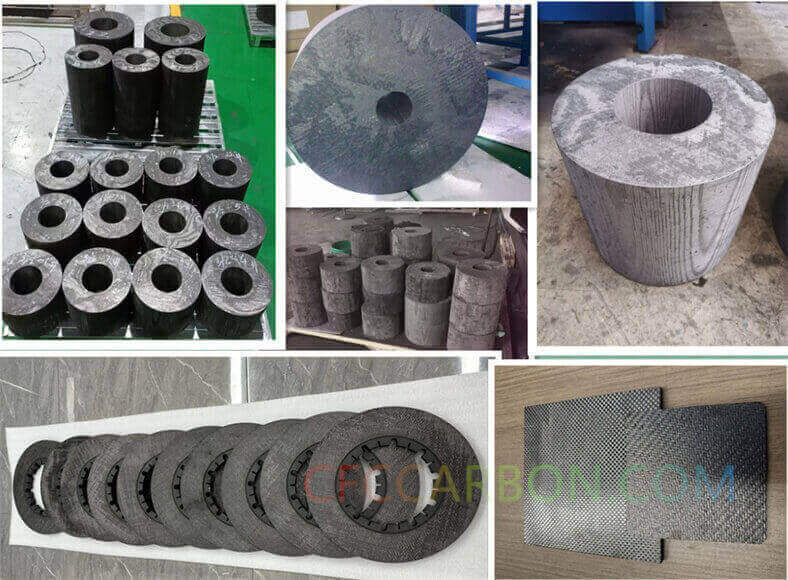
3D 4D carbon fiber composite material manufacturer factory -airplane brake disc plates sheets U L profiles-2D(s)
Piston-driven engines such as gasoline and diesel engines could operate at increased efficiency and reduced weight if cooling requirements were minimized through the use of high-temperature capability materials. Carbon-carbon has been proposed and is under evaluation for many applications in this area. A CC piston has been tested successfully at NASA Langley Research Center, and a U.S. patent has been issued convering this composite piston concept. Carbon fiber reinforcements of four-dimensional (4D) angle interlock and a knitted multilayer warp sock were evaluated with resin infiltration and chemical vapor deposition (CVD) carbon densification to complete the CC composite processing. The CC piston has a lower density than the conventional aluminum lightweight piston. This reduced weight improves internal combustion engine efficiency. However, the very low thermal expansion of CC composite, relative to aluminum, and the high-strength retention of CC composite at elevated temperatures allow a piston-to-cylinder wall clearance that is small enough to eliminate the need for piston rings. Lightweight CC pistons permit the use of lighter weight reciprocating components, allowing possible higher engine speeds and improved engine performance. Issues such as oxidation life, oil, and fuel infiltration effects and cyclic endurance require continued study, but the prognosis for CC pistons is very promising.
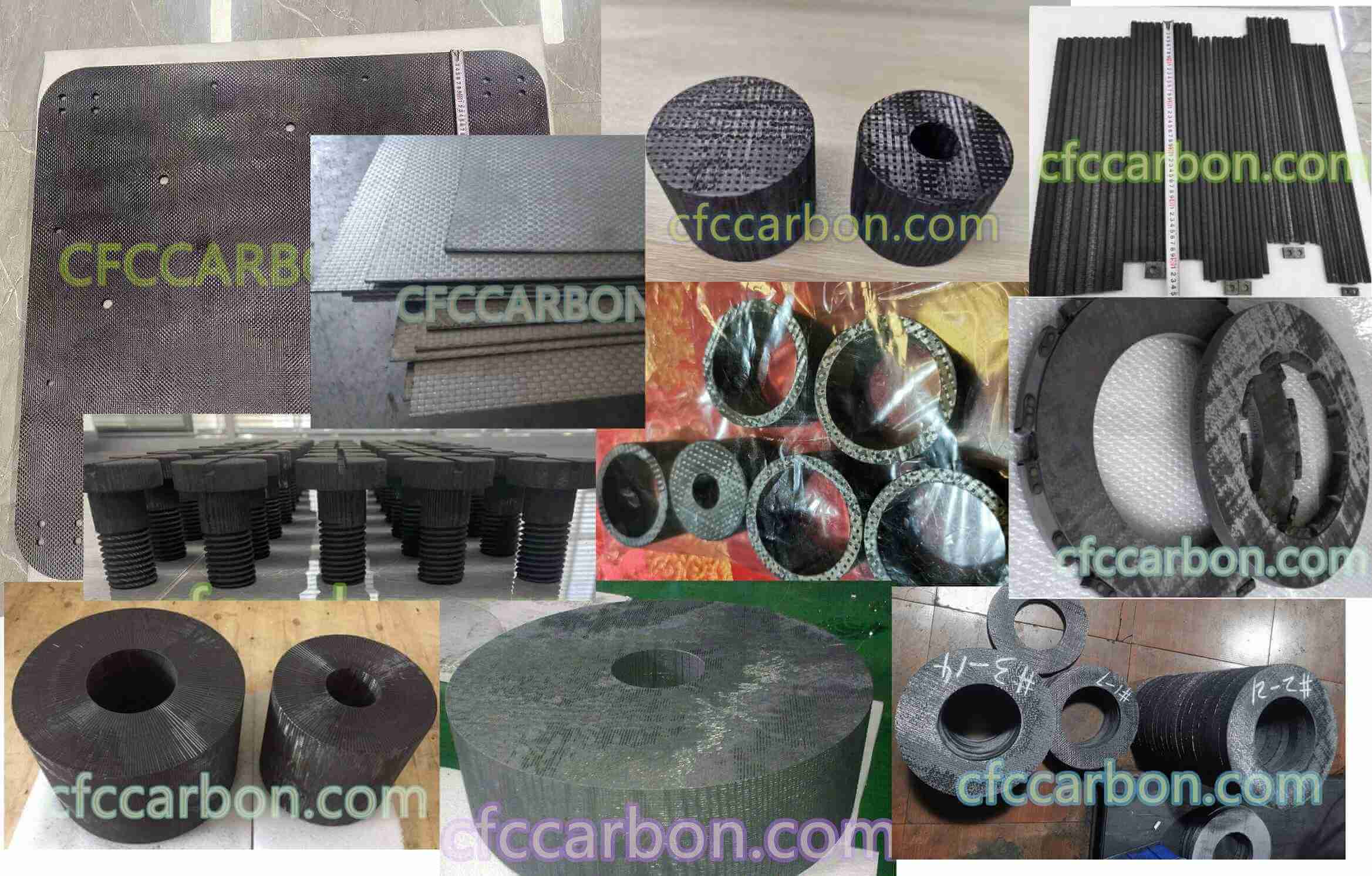
carbon fiber composite material manufacturer in China(1)
In another engine application, CC composite is being evaluated for use on rotary valves in two- and four-stroke-cycle small engines. The CC composite rotary valve drives off the crankshaft and, as a replacement for the conventional poppet valve, it offers weight savings, quieter engine operation, and a reduced torque load. As in the CC piston, the achievable low thermal expansion and good strength retention at high temperatures allow the close tolerances needed for the rotary valve function.
A very promising area for CC composite engine components is in diesel engines. Potential benefits that could be derived from CC components have been identified in both adiabatic and low-heat rejection designs. The adiabatic diesel engine is based upon the adiabatic or no-heat-loss process. Essentially, this process involves an insulated combustion chamber from which the high-temperature exhaust gases are passed, first through an insulated duct system and then through turbine wheels, to extract additional energy before finally being expelled. The turbines power the compressor and the crankshaft. A basic diesel engine has approximately 36 percent thermal efficiency and the adiabatic diesel has approximately 48 percent thermal efficiency; this thermal measurement is equivalent to a terbine inlet temperature of over 4000F for a gas turbine engine.
The turbocharger and pistons are CC components. The maximum temperature anticipated, with advanced materials, is approximately 2000F compared with current maximum diesel temperatures of approximately 600F. High-temperature resistant materials such as CC composite would permit reduced airflow and reduced engine volume. Thermal shock-resistant material is required and, because reduced heat transfer is a key consideration, low thermal conductivity CC composite or shield materials also may be required.
Other diesel-engine designers have considered CC composite to be a viable material for use on advanced engines but have emphasized a low-heat-rejection diesel design rather than an adiabatic diesel design. A low-heat-rejection diesel engine retains heat within the engine and is a passive means fro improving efficiency. The temperatures of interest are on the order of 1600F. The low-heat-rejection engine would offer a thermal efficiency of 45 percent; this efficiency is achieved with less complexity than would be required for the adiabatic diesel engine to achieve an anticipated 48 percent thermal efficiency.
related news /articles:
Applications of CC composite material–piston
Carbon fibers for carbon-carbon applications (4)
Carbon-carbon composite application for aircraft, rocket, engineer, and in industry
Carbon composite material applied in Missile engineer