Title: Advanced SiC-Coated Carbon-Carbon Composites: Breakthrough in High-Temperature Aerospace Applications
Introduction
Carbon-carbon composites (C/C) have revolutionized aerospace engineering with their unmatched strength-to-weight ratio and thermal
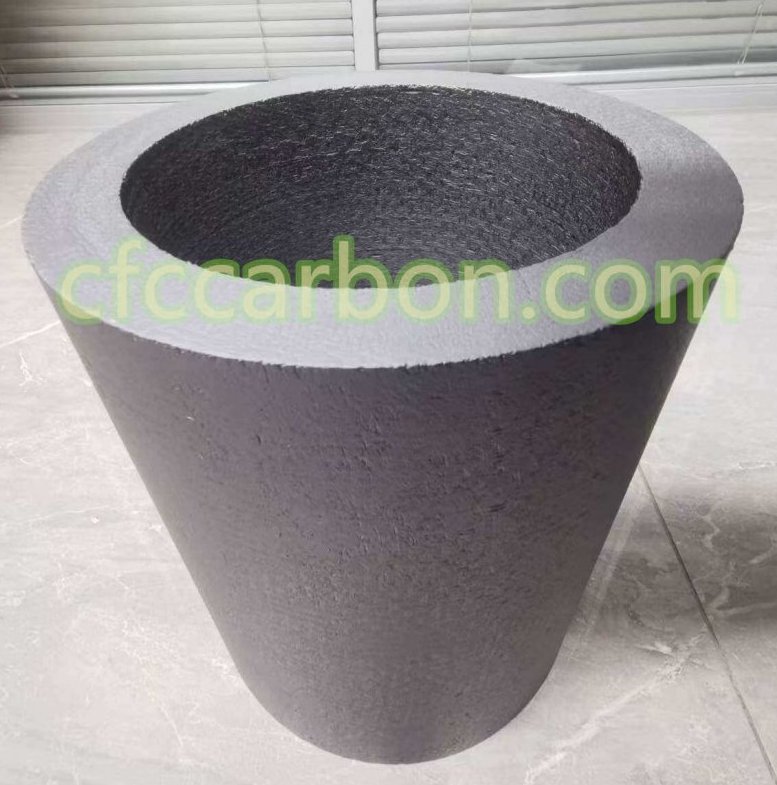
SiC coating carbon fiber composite material-CC-CFC (2)
stability. However, oxidation above 500°C limits their lifespan. A recent study by CFCCarbon (www.cfccarbon.com) introduces a novel SiC-B4C coating technology, enhancing C/C durability in extreme environments.
Coating Fabrication & Microstructure
The coatings were synthesized via pack cementation, where silicon vapor reacts with the C/C substrate to form a cubic SiC layer (lattice parameter: 4.37 Å). Boron carbide (B4C) particles (0.1–1.0 µm) were integrated to inhibit crack propagation. Two variants were tested:
-
Light Coating (150 µm): Dominated by cubic SiC, ideal for moderate thermal cycles.
-
Moderate Coating (300 µm): Contains hexagonal SiC polymorphs, suitable for prolonged high-temperature exposure (>1200°C).
Key Findings
-
Phase Composition: XRD confirmed SiC and B4C phases, with free silicon filling substrate pores, mimicking original fiber morphology.
-
Crack Analysis: Thermal expansion mismatch (Δα >0.5% at 1000°C) induced tensile stresses (~35,000 psi), leading to surface cracks spaced 200–600 µm. Cross-sectional SEM revealed cracks penetrating the substrate, mitigated by B4C grain boundaries
SiC coating carbon fiber composite material-CC-CFC (3)
-
Oxidation Resistance: B4C acted as an oxygen diffusion barrier, reducing weight loss by 40% compared to uncoated C/C in air at 800°C.
Industrial Applications
-
Rocket Nozzles: The moderate coating’s thickness withstands erosive exhaust gases.
-
Aircraft Brakes: Light coating reduces wear rates by 30% in repetitive braking cycles.
-
Nuclear Reactors: Enhanced radiation resistance due to SiC’s low neutron absorption.
Future Directions
CFCCarbon plans to optimize coating uniformity via pulsed CVD and explore self-healing mechanisms using molten silicon infiltration. Collaborative efforts with NASA aim to qualify these composites for Mars re-entry vehicles by 2026.
Conclusion
This breakthrough positions SiC-B4C coated C/C as a cornerstone material for next-gen aerospace systems, combining cost-effectiveness (20% lower than traditional CVI coatings) with unparalleled performance.
related news /articles:
High-Performance Coatings for Carbon fiber Carbon Composites
Basic properties of uncoated carbon-carbon composite material
Oxidation kinetics and mechanisms of a 2D C/C composite (1)
Coating systems for carbon fiber carbon composites material (1)