Advanced Protective Coatings for Carbon-Carbon Composites: Innovations in High-Temperature Applications
By CFC Carbon | Updated: May 16, 2025
What Are Coatings on Carbon-Carbon Composites?
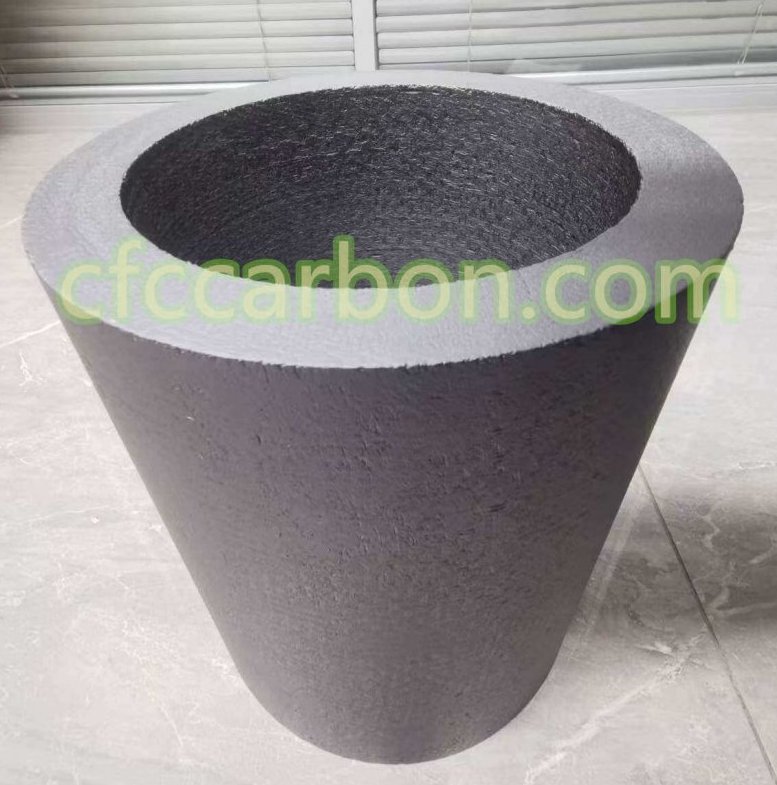
SiC coating carbon fiber composite material-CC-CFC (2)
Carbon-carbon (C/C) composites are high-performance materials renowned for their exceptional strength-to-weight ratio and thermal stability in inert environments. However, when exposed to oxidizing conditions above 500°C, these composites require protective coatings to prevent rapid degradation. As noted by CFC Carbon, coatings serve as critical barriers against oxidation, erosion, and ablation, enabling C/C composites to function in extreme environments like aerospace propulsion systems and hypersonic vehicle components.
Historically, uncoated C/C composites excelled in short-duration, ultra-high-temperature applications (e.g., rocket nozzles) due to their innate ablative properties. However, the emergence of reusable systems—such as the Space Shuttle’s thermal protection tiles—demanded durable coatings to extend material lifespan under cyclic heating and mechanical stress.
Manufacturing Techniques for C/C Coatings
Modern coating technologies leverage advanced deposition methods to enhance performance:
-
Chemical Vapor Deposition (CVD)
SiC coating carbon fiber composite material-CC-CFC (1)
-
A hydrocarbon gas is used to deposit carbon or ceramic layers onto C/C surfaces, creating dense, oxidation-resistant barriers. This method is ideal for complex geometries.
-
-
Plasma Spraying
-
High-velocity plasma jets melt and project ceramic powders (e.g., zirconia, silicon carbide) onto composites. NASA’s research highlights plasma-sprayed multilayer coatings that reduce ablation rates by 90% in oxyacetylene torch tests.
-
-
Slurry-Based Processes
-
Low-cost techniques like dip-coating or spin-coating apply ceramic slurries (e.g., mullite or rare-earth disilicates) followed by sintering. These coatings demonstrate 500+ hours of steam oxidation resistance at 1482°C.
-
Classification and Functional Properties of Coatings
Coatings are tailored to specific operational demands:
Coating Type | Key Materials | Performance Features |
---|---|---|
Anti-Oxidation | SiC, ZrB2-SiC | Blocks oxygen diffusion; withstands 1600°C+ |
Thermal Barrier | Sm2O3-ZrO2, Yttria | High emissivity (ε >0.9) for radiative cooling |
Ablation-Resistant | HfC-TaC, Ultra-HTC ceramics | Reduces mass loss by 70-90% in hypersonic flows |
Environmental Barrier | Rare-earth disilicates | Protects against water vapor and corrosive gases |
Cutting-Edge Applications
-
Aerospace & Hypersonics
-
Coated C/C composites are integral to reusable spacecraft (e.g., heat shields) and hypersonic vehicle leading edges. NASA’s bilayer coatings combining SiC and Sm2O3-ZrO2 have shown 71% lower ablation rates during re-entry simulations.
-
-
Turbine Engines
-
Oxidation-resistant coatings enable C/C use in turbine blades and combustor liners, reducing fuel consumption by 10% in next-gen engines.
-
-
Rocket Propulsion
-
Advanced coatings enhance longevity in rocket nozzles and thrust chambers, meeting demands for higher-thrust systems.
-
Performance Advantages of Modern Coatings
-
High-Temperature Stability: Retain mechanical properties up to 2000°C.
-
Thermal Shock Resistance: Low CTE mismatch minimizes delamination risks.
-
Customizability: Multilayer architectures balance ablation resistance and emissivity.
-
Cost Efficiency: Slurry-based methods cut production costs by 30% compared to plasma spraying.
The Future of Coated C/C Composites
Recent innovations focus on self-healing coatings and nanomaterial-enhanced barriers. For instance, carbon nanotube (CNT)-reinforced coatings improve interfacial adhesion in polymer matrices, while graphene layers offer unparalleled thermal conductivity714. CFC Carbon’s R&D team is also exploring hybrid systems combining CVD ceramics with rare-earth modifiers for extended durability in nuclear reactor components.
Conclusion
From the Space Shuttle’s pioneering thermal tiles to tomorrow’s hypersonic platforms, protective coatings have transformed C/C composites into structural materials capable of withstanding extreme environments. As industries demand lighter, reusable, and higher-performance solutions, advancements in coating technology will continue to drive innovation.
For technical specifications on CFC Carbon’s coated C/C products, visit www.cfccarbon.com.
related news /articles:
Introduction of high-temperature coatings on CC composite material
High-Performance Coatings for Carbon fiber Carbon Composites
Advanced Coatings for Carbon fiber Carbon Composites
Thermal stabilization of 2D carbon-carbon composite object geometry (6)