Title: Advanced Internal Coating Technologies for Carbon-Carbon Composites: Enhancing Durability in Extreme Environments
Introduction to Carbon-Carbon Composites (C/C)
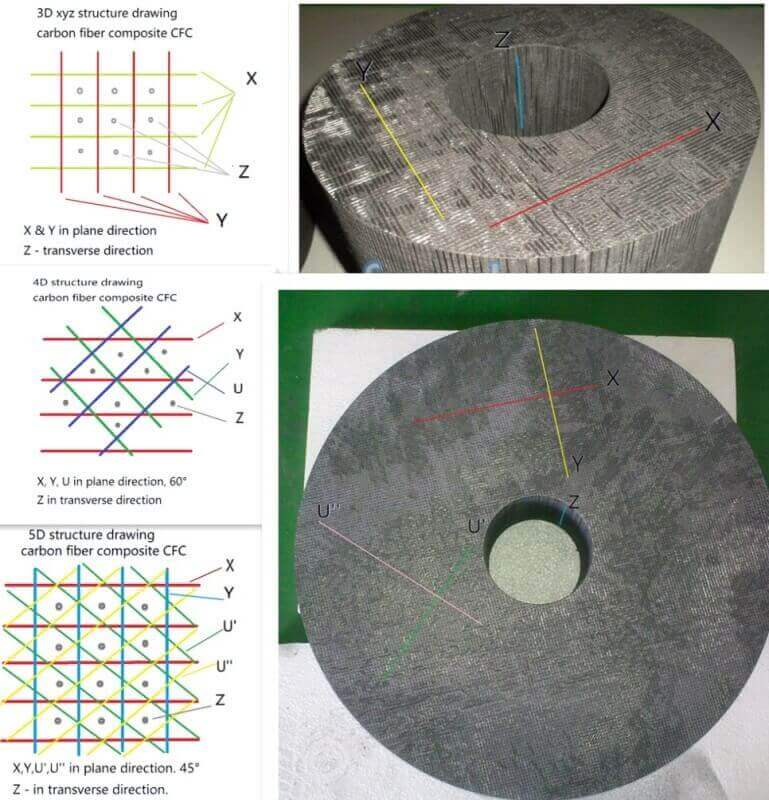
3D 4D 5D carbon fiber composite CFC structural diagram drawing material (1)
Carbon-carbon composites (C/C) are high-performance materials composed of carbon fibers embedded in a carbon matrix. Known for their exceptional strength-to-weight ratio, thermal stability (up to 2,500°C), and resistance to thermal shock, they are widely used in aerospace, defense, and industrial applications such as rocket nozzles, aircraft brakes, and high-temperature furnace components. However, their Achilles’ heel lies in oxidation vulnerability above 500°C, necessitating advanced protection methods like internal coatings to extend service life.
Key Manufacturing Methods for C/C Internal Coatings
-
Solution-Based Impregnation (Liquid Precursor Method)
This technique involves infiltrating porous C/C substrates with organometallic solutions, colloidal suspensions, or metal alkoxides. Through cycles of drying, gelation, and heat treatment, ceramic coatings (e.g., boron-rich layers) form on internal surfaces. For instance, boron oxide (B₂O₃) glass layers effectively seal microcracks and inhibit oxygen diffusion, enhancing oxidation resistance by 40–60% in high-temperature tests. CFCCARBON’s patented multi-cycle impregnation process ensures uniform coating thickness even in complex geometries, such as 3D-reinforced brake discs. -
Matrix Chemical Modifications
By integrating glass-forming additives (e.g., SiC, ZrB₂) into resin or pitch precursors, manufacturers create self-healing matrices. When exposed to oxygen, these additives generate viscous glass phases that fill pores and shield fibers. For example, CFCCARBON’s 2.5D C/C composites use boron carbide (B₄C) powders to form borosilicate glass under oxidative conditions, reducing mass loss by 70% at 800°C. This method is particularly effective when combined with external ceramic coatings like SiC. -
Chemical Vapor Infiltration (CVI)
A cornerstone of C/C production, CVI deposits non-oxide ceramics (e.g., SiC, TiC) directly onto fiber surfaces within the composite. CFCCARBON’s high-density C/C composites (1.9 g/cm³) leverage CVI to replace the carbon matrix with oxidation-resistant SiC, achieving short-term stability up to 1,500°C. Recent advancements, such as forced gas flow and thermal gradient optimization, have slashed processing time from weeks to 24 hours, enabling cost-effective mass production.
Product Classification and Applications
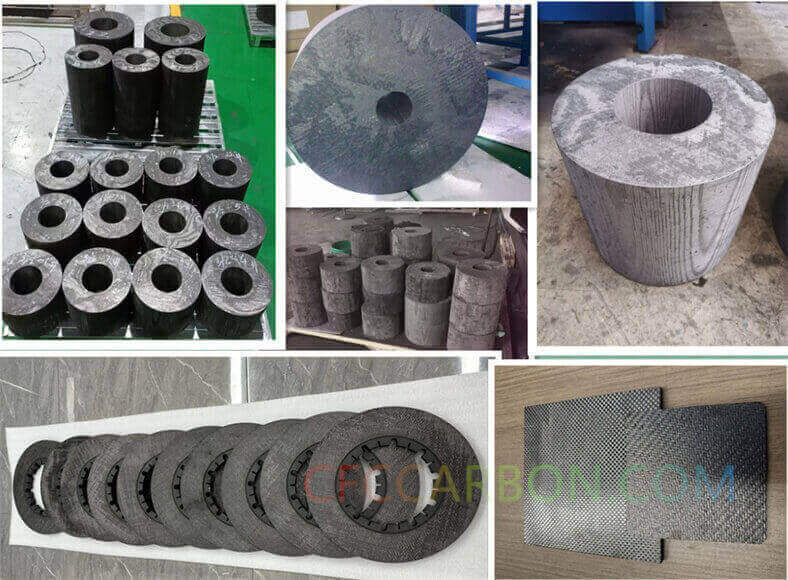
3D 4D carbon fiber composite material manufacturer factory -airplane brake disc plates sheets U L profiles-2D(s)
-
Structural Dimensions:
-
2D/2.5D: Ideal for aircraft brakes and heating elements due to balanced in-plane strength and cost efficiency.
-
3D/4D: Used in rocket nozzles and nuclear reactors for superior through-thickness mechanical properties.
-
-
Density Grades:
-
Low-density (1.4–1.6 g/cm³): Thermal insulation blankets and furnace fixtures4.
-
High-density (1.7–1.9 g/cm³): Critical components requiring ablation resistance, such as hypersonic vehicle leading edges.
-
Performance Advantages and Limitations
Strengths:
-
Thermal Stability: Retains 50% flexural strength at 2,200°C, outperforming metals.
-
Lightweight: 1/4 the density of steel, reducing fuel consumption in aerospace systems.
-
Customizability: Tailored fiber architectures (e.g., 4D hoop-weave) optimize stress distribution.
3D 4D 5D Hoops, Loop, weaving, stucture, drawing, carbon fiber, carbon, composite, CFC, CC, manufacturer, China, (1)
Challenges:
-
Oxidation Sensitivity: Requires hybrid protection (internal + external coatings) for prolonged use above 750°C.
-
Cost: Multi-step densification and coating processes increase production time and expense.
Innovations from CFCCARBON
As a leader in C/C technology, CFCCARBON offers:
-
High-Density 3D Composites: Achieve 1.95 g/cm³ via pitch-based processing, ideal for reusable space vehicle components.
-
Coating Integration: Proprietary ZrB₂-SiC multilayer coatings provide 2,200°C ablation resistance, validated in NASA-funded trials5.
-
Custom Solutions: From 2D insulation barrels to 4D brake discs, their portfolio spans 20+ industries.
Conclusion
The evolution of internal coating technologies—from liquid precursors to CVI—has transformed carbon-carbon composites into a cornerstone of extreme-environment engineering. With companies like CFCCARBON pushing boundaries in material science, C/C composites are poised to revolutionize sectors demanding lightweight, high-temperature resilience. For detailed specifications or collaboration opportunities, visit www.cfccarbon.com.
related news /articles:
Innovations in Carbon-Carbon Composite Internal Coatings
Introduction of high-temperature coatings on CC composite material
Advanced Protective Coatings for Carbon-Carbon Composites
Advanced Coatings for Carbon fiber Carbon Composites